When thinking through a seal application design, don’t forget about slipcoat, flock, tape, attachments, and adhesion promoters.
Slip Coat
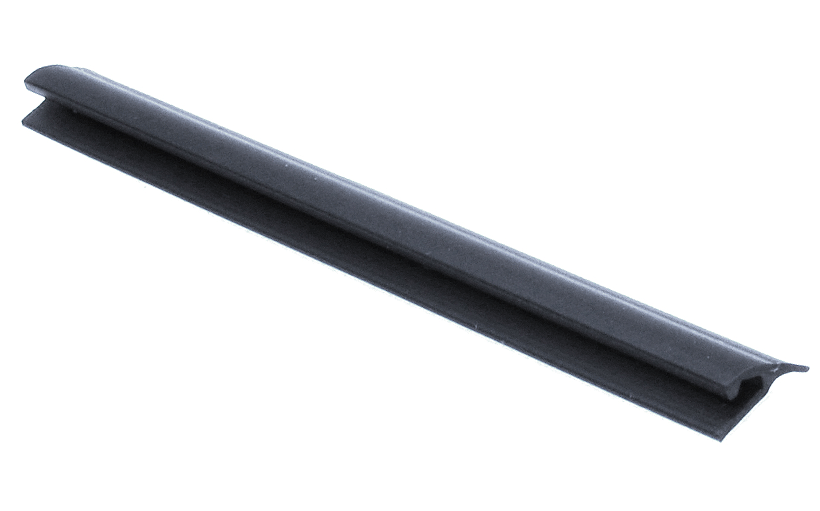
A slip coat is a coating applied to the surface of a seal in order to reduce abrasion and increase seal life. Usually slip coating is applied to glass run channel and other dynamic seal applications. The job of the slip coat is to keep the seal working – allowing, for example, a glass window to move in and out – while not scuffing or marring the material running in and out of its channels. Slip coats keep seals from being harmed by cleaning products, they don’t fade over time, and generally are weatherproof.
Flocking
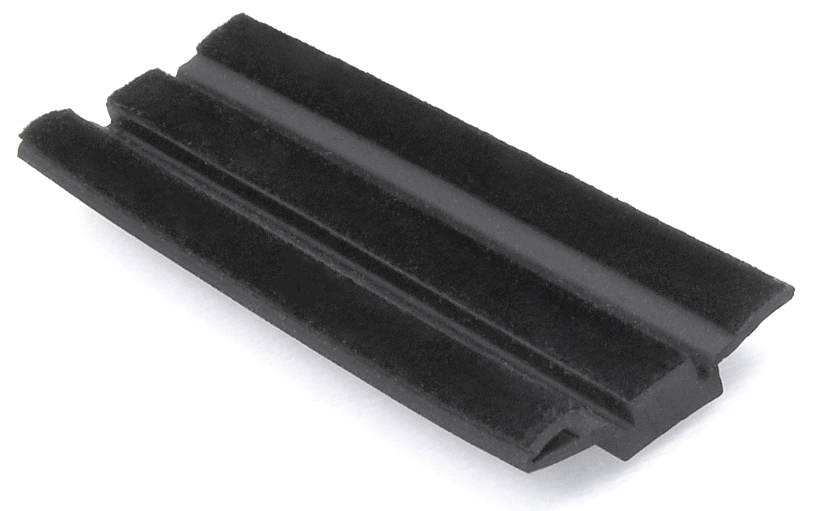
Flocking is similar to slip coating but has a definite look and texture – similar to velour. The process involves applying a flocking spray or flocking powder to the surface of the seal to insulate, absorb water, dampen vibration, and reduce friction. Most flocking is black because the seal it is attached to is also black. But, depending on the application, it can be dyed to match most other colors. Flocking is found in auto and home windows – and in many other applications demanding weatherproofing of some sort.
Tape
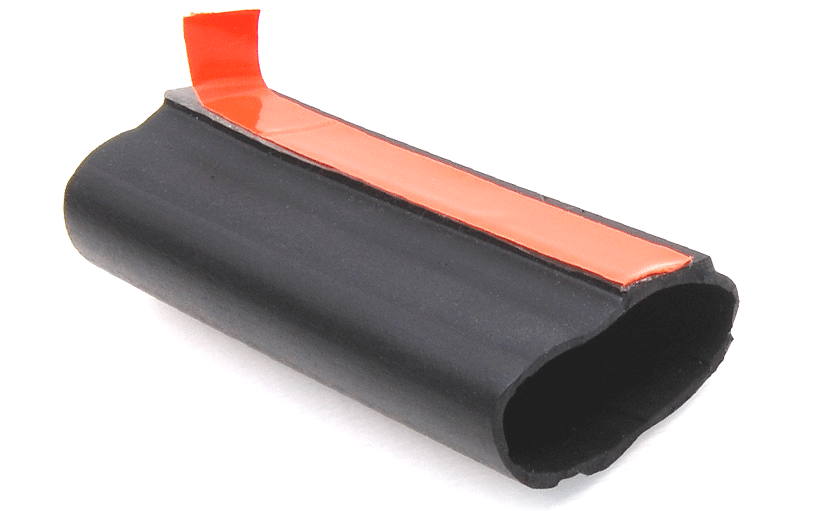
Tape is a means of attaching a seal to another surface. Usually the seal is manufactured with an adhesive side affixed in place on the seal and a second adhesive side protected by a covering which is removed during a later stage of the manufacturing or assembly process.
Attachment
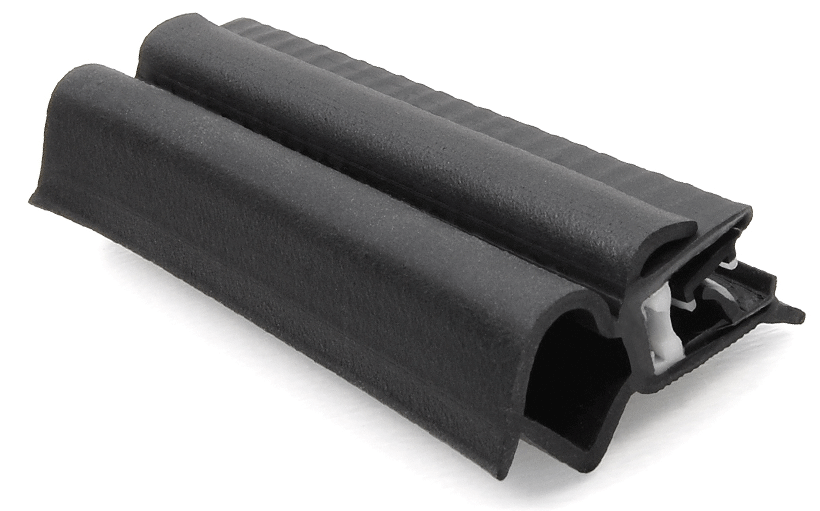
A seal attachment includes adhesives and mechanical fasteners. Both are meant to join a seal to another surface and each as its pro’s and con’s. Adhesive attachments (including tape) can be temporary or permanent and may work in conjunction with mechanical fasteners. Mechanical fasteners include wire carrier seals, kerf insertions, multi-durometer extrusions, and push-pin seals, one of the most common in the auto industry.
Adhesion Promoters
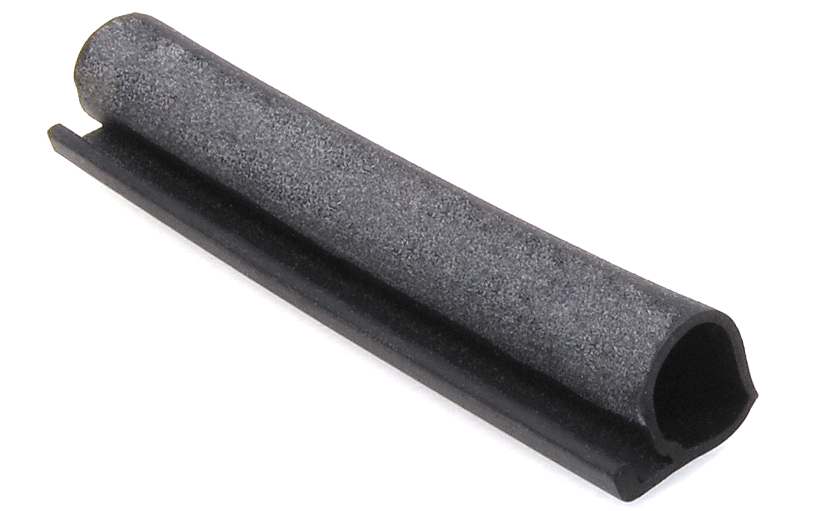
An adhesive or adhesion promoter applied to a seal does exactly that — promotes adhesion of a tape or other material to a seal. Adhesion promoters improve bonding between substances that would normally resist bonding together, provides a quick-stick solution for two materials, and promotes bonding in curved or irregular surfaces.
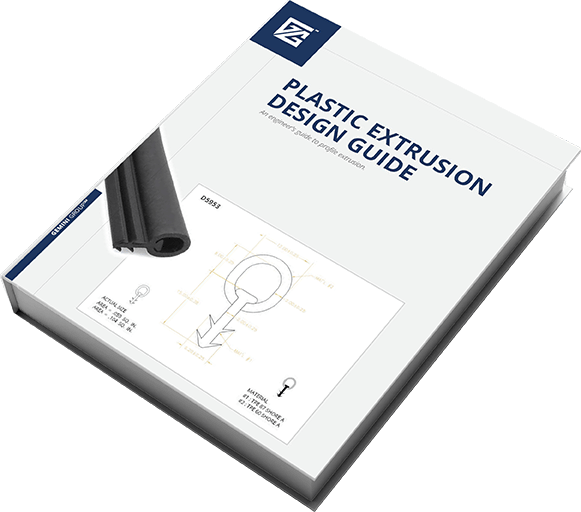
PROFILE EXTRUSION DESIGN GUIDE
We are proud to present to you the cumulation of over 50 years of experience in extrusion. We’ve helped thousands of engineers just like you with their extruded profile design – and this guide truly is the next best thing to working directly with our extrusion specialists.