GPI, GT Plastics, Sierra, GPM
STRUCTURAL PLASTIC EXTRUSIONS
Engineers turn to us every day to reduce mass with strong, lightweight, durable structural plastic extrusions. Our experienced team can help you optimize your design and material for the most demanding applications.
Applications
- Pillars
- Rockers
- Reinforcements
- Running Boards
- Construction
- Flooring
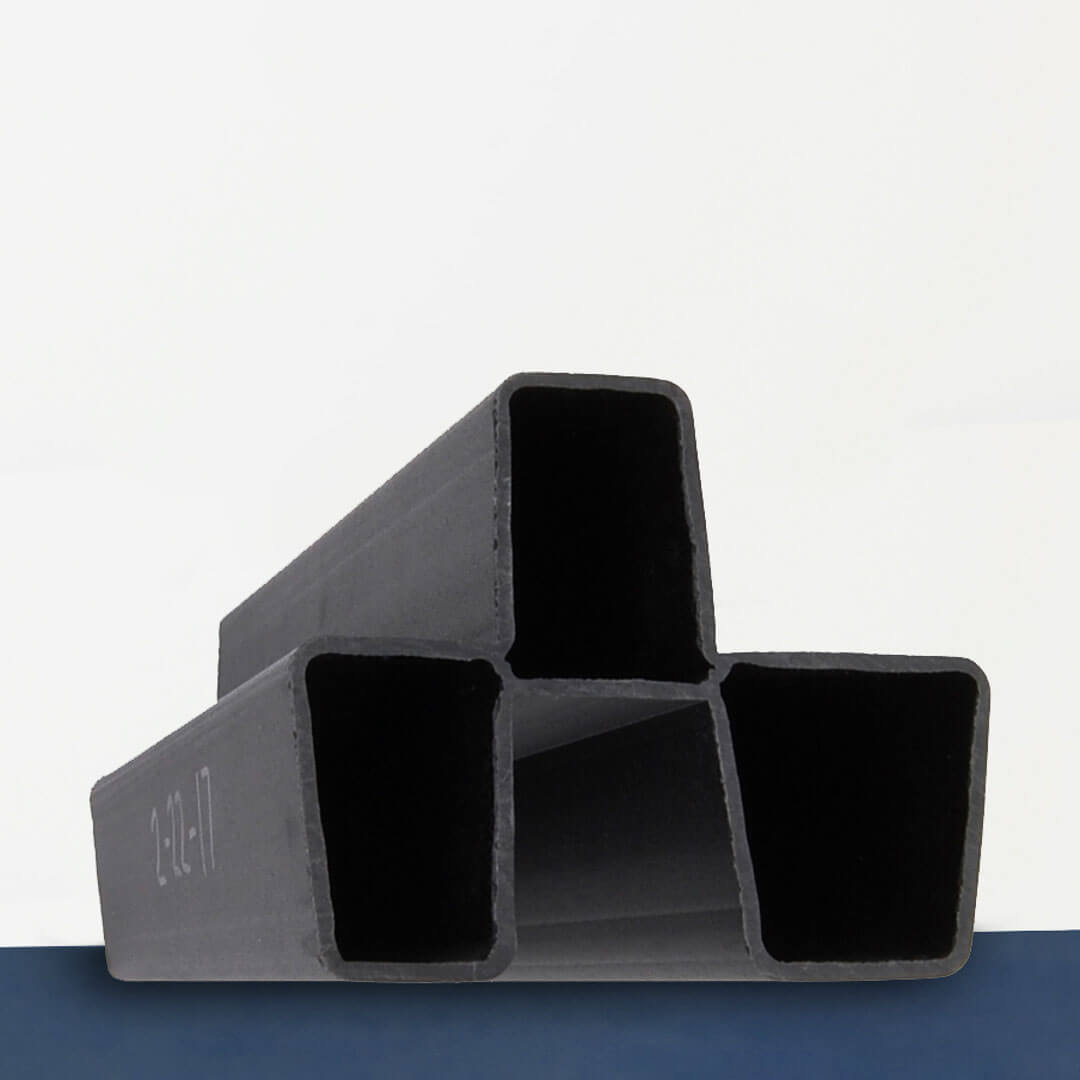
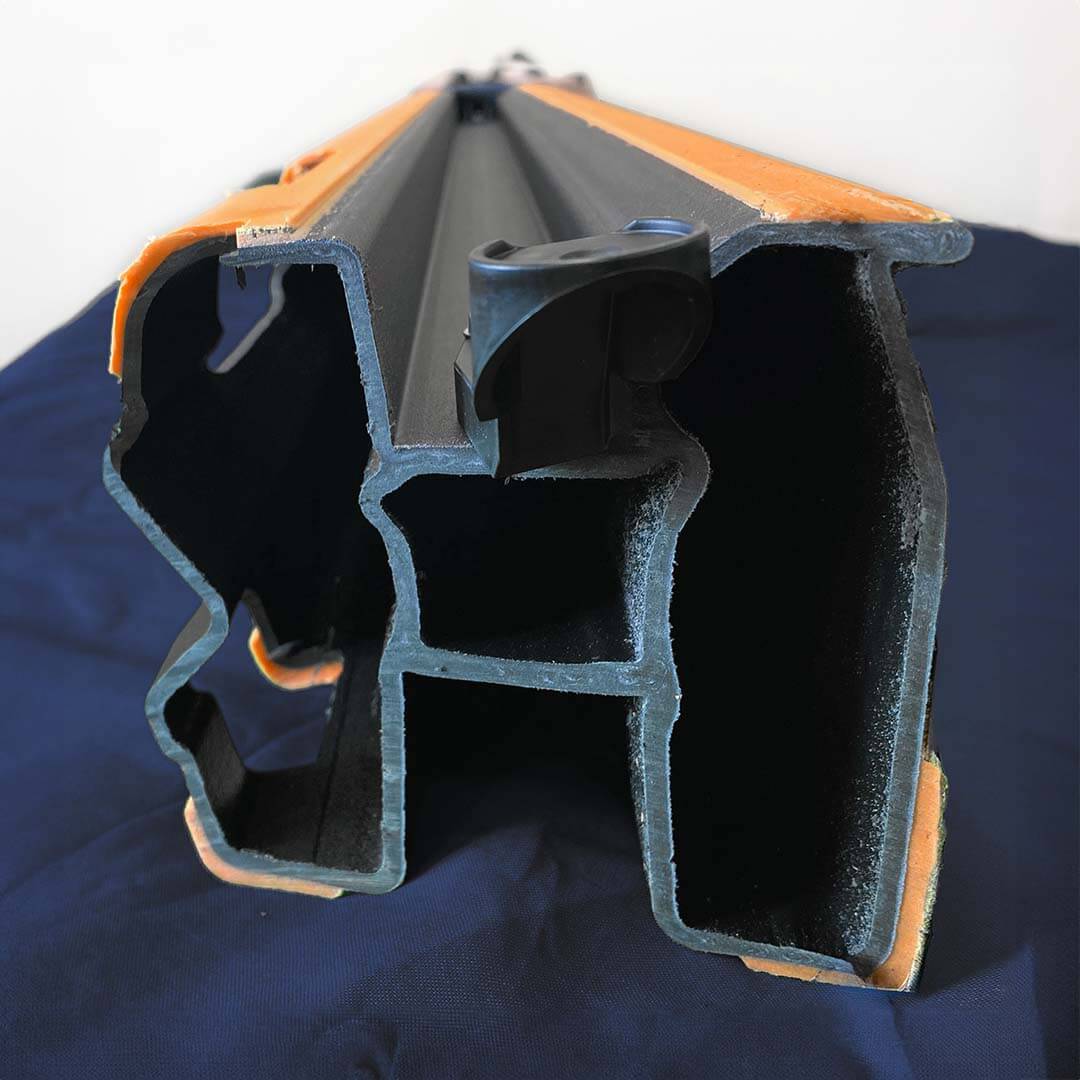
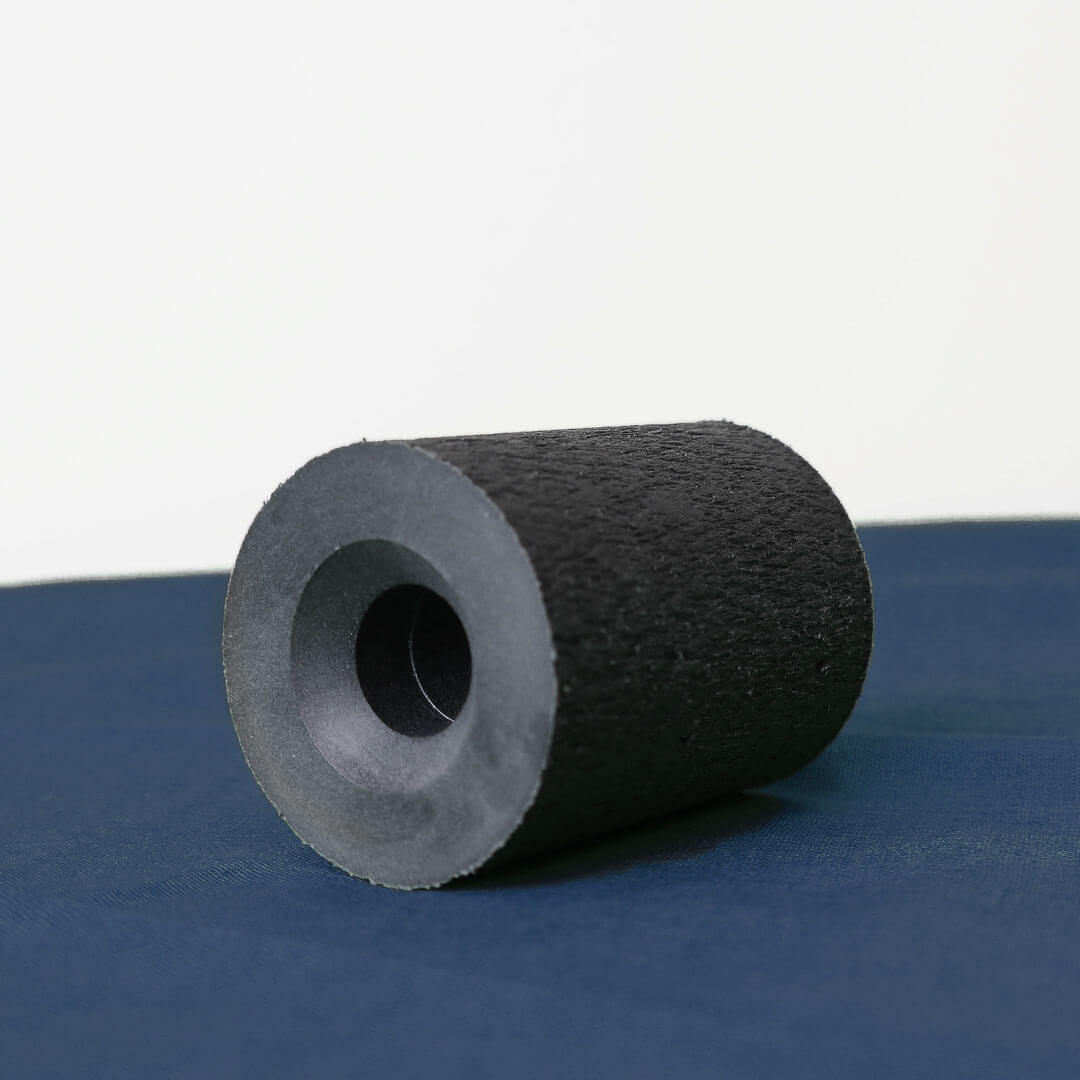
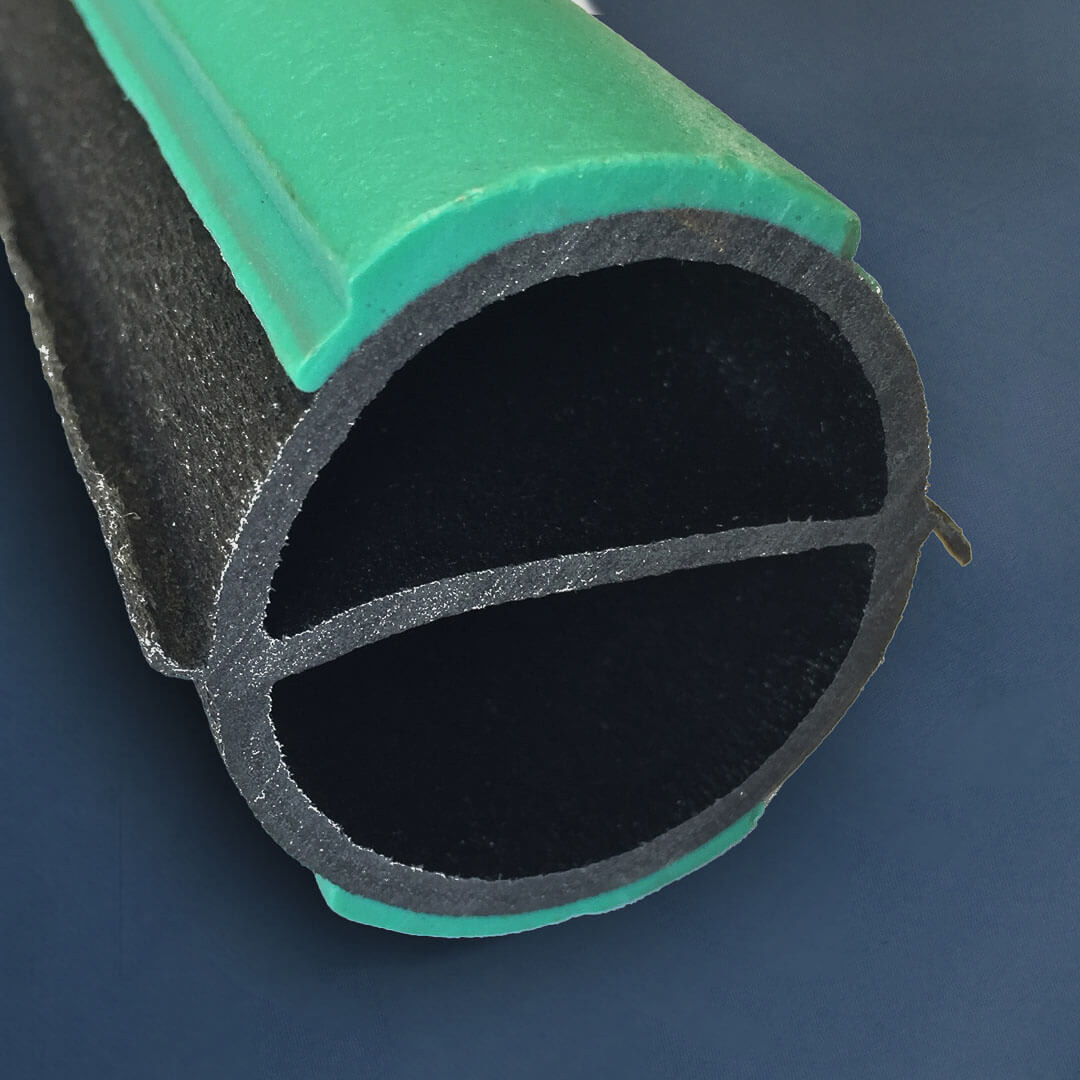
STRENGTH IN DESIGN AND ENGINEERING
Our structural plastic extrusions are designed and engineered to provide strength and support while functioning as a load-bearing element within a structure.
We start with high-quality thermoplastic resins, such as PVC, HDPE, PP, ABS, Nylon, and others, that are blended with additives, stabilizers, and pigments to meet your performance requirements, then optimize your design for performance and manufacturability.
The result is a versatile, lightweight, and customizable alternative to metal components.
FEATURES
Used widely in the automotive industry, our structural plastic extrusions can withstand some of the harshest environments and most demanding applications and feature a number of benefits.
- High strength-to-weight ratio
- Impact resistance
- Resistance to deformation
- Resistance to corrosion
- Chemical resistance
- UV Stability
ADVANTAGES OF STRUCTURAL PLASTIC OVER OTHER MATERIALS
Structural plastic extrusions offer many advantages over other traditional materials such as metal, wood, and concrete.
LIGHTWEIGHT
Structural plastic extrusions are up to 10 times lighter than metal and wood, making them easier to handle, transport, and install, and a choice alternative for lightweighting.
CUSTOMIZATION AND FLEXIBILITY
Plastic offers a high level of design flexibility, allowing us to create complex shapes, geometries, and textures that are difficult or costly to achieve with metal.
SUPERIOR FUNCTIONALITY
Structural plastic extrusions are non-magnetic and offer thermal and electrical insulation.
CORROSION AND CHEMICAL RESISTANCE
Many plastics, especially reinforced plastics like glass-filled Nylon, are highly resistant to corrosion and chemical degradation.
EASE OF MACHINING
Plastic extrusions are easier to machine than metal, which can lead to faster production cycles and reduced lead times.
LOWER MAINTENANCE COSTS
Plastics extrusions do not require the same level of maintenance as metal since they do not corrode or deteriorate in the same way. This can lead to lower long-term maintenance costs.
WHY CHOOSE US?
We’re staffed by extrusion specialists that have helped develop over 7,000 profiles. Our team is driven, innovative, and capable of finding the most cost-effective solution for your structural application.
MATERIAL EXPERTISE
We specialize in hard-to-process materials such as 60% glass-filled nylon (PA-60), polypropylene (PP), proprietary heat-expandable materials, and over 50 specialty resins. This allows us to recommend the most suitable materials for structural plastic extrusions, ensuring optimal performance and durability.
CUSTOMIZATION AND FLEXIBILITY
We excel in manufacturing complex and hollow profiles that that are specifically engineered for structural applications. These profiles can be customized with reinforcements such as internal ribs, gussets, or flanges to enhance strength and load-bearing capabilities, providing structural integrity and optimizing overall product performance.
MULTIPLE IN-HOUSE PROCESSES
In addition to plastic extrusion and co-extrusion, we employ number of complimentary processes in-house such as in-line processing, machining, fabrication, and assembly, allowing us to deliver finished components ready for integration into your final product.
Wherever You’re Located, We’re Here to Help
18 strategic locations in North America to meet the needs of our diverse customer base.
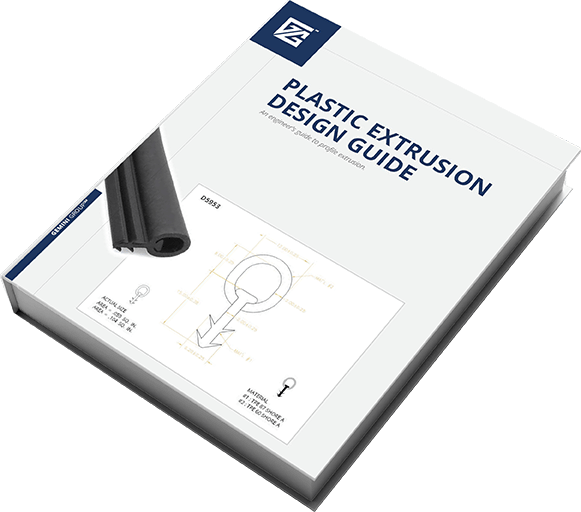
PLASTIC EXTRUSION DESIGN GUIDE
Is your extrusion design optimized to meet the constraints of the extrusion process? This free guide offers a solid foundation in the requirements for successful extrusion design. Created by engineers for engineers, and based on decades of extrusion development and manufacturing experience.
Insights
Get to know us. Get in touch today.
We have the resources to meet any part or production challenge. Let’s talk about what that means for you.
"*" indicates required fields