GPI, GT Plastics, Sierra, GPM
EXTRUDED SEALS AND WEATHERSTRIPPING
Our extruded seals are 100% thermoplastic, an excellent alternative to rubber for many sealing and weatherstripping applications. Using the most advanced plastic compounds available today, we can help solve your toughest sealing challenges.
EXTRUDED SEAL SPECIALISTS YOU CAN RELY ON
Automotive and industrial customers across North America consistently rely on us to help them choose the most cost-effective design and materials for their sealing applications. We have the experience and technology to help you, too.
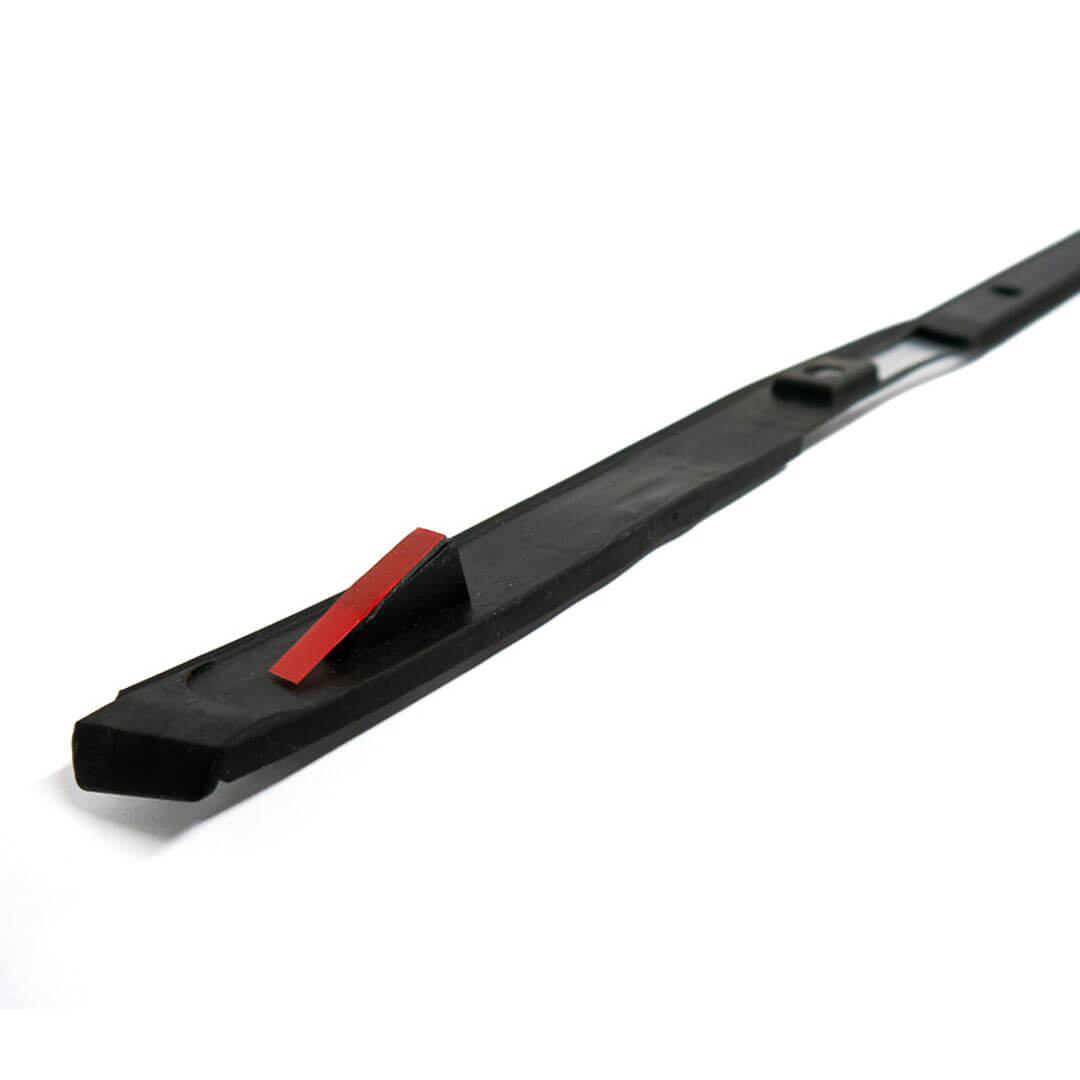
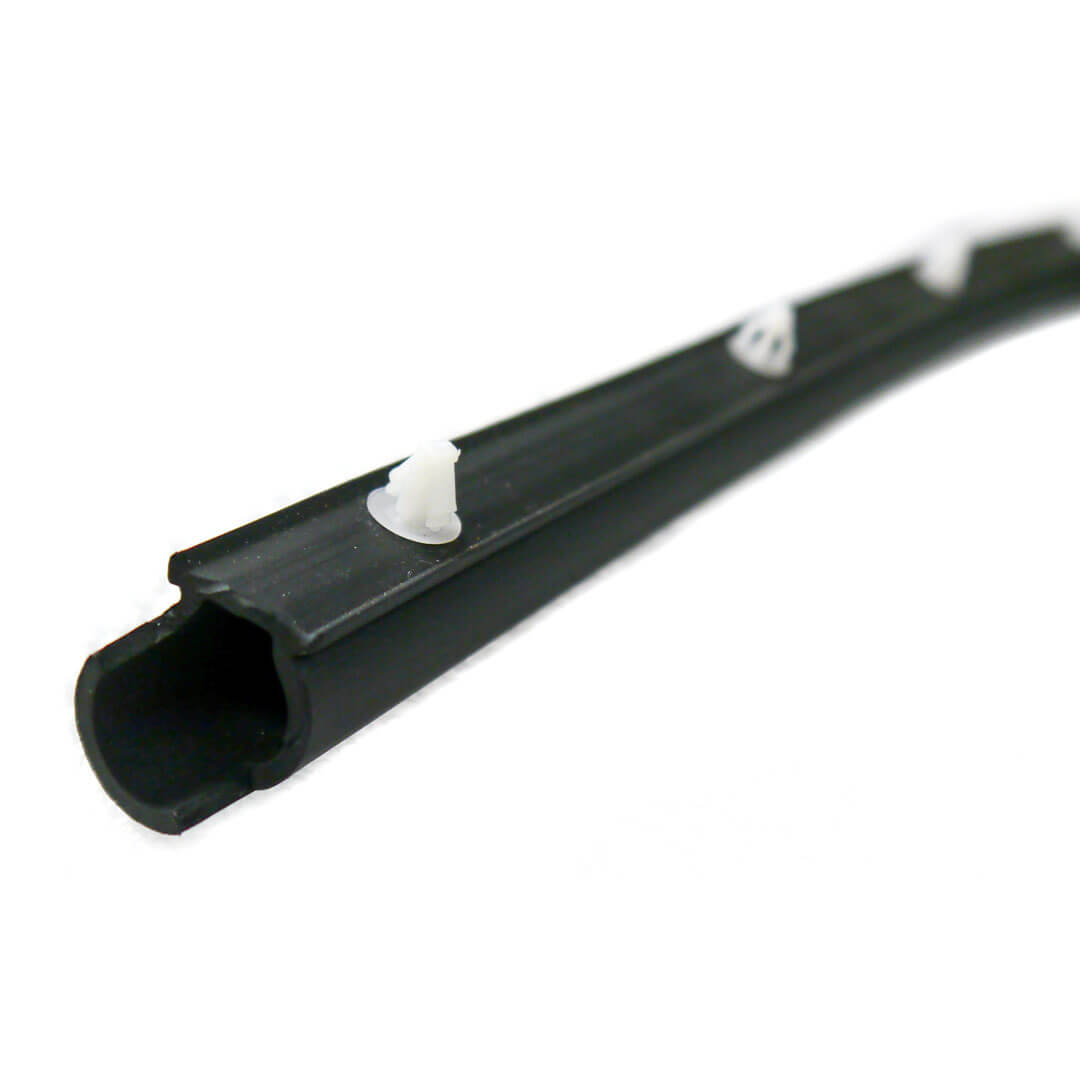
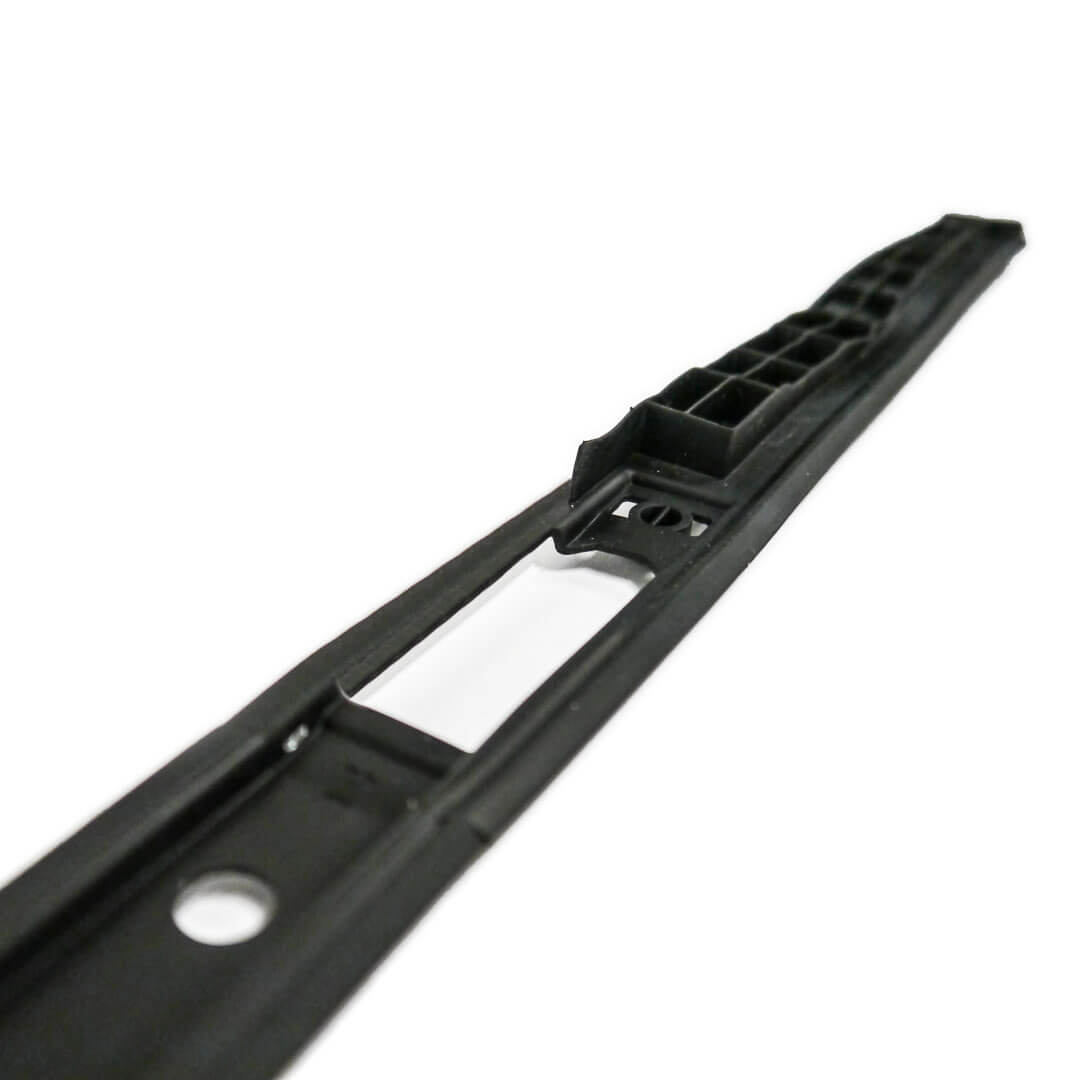
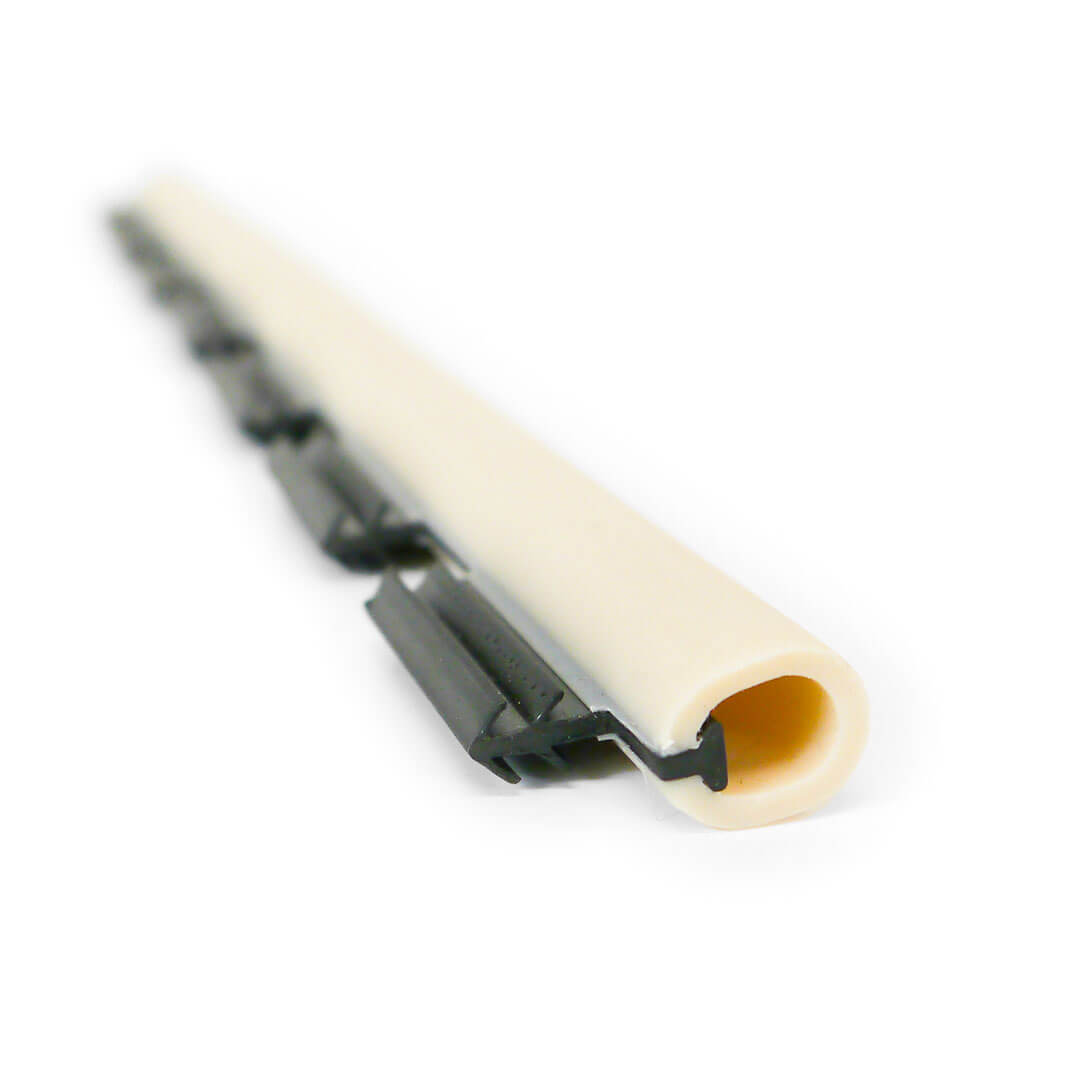
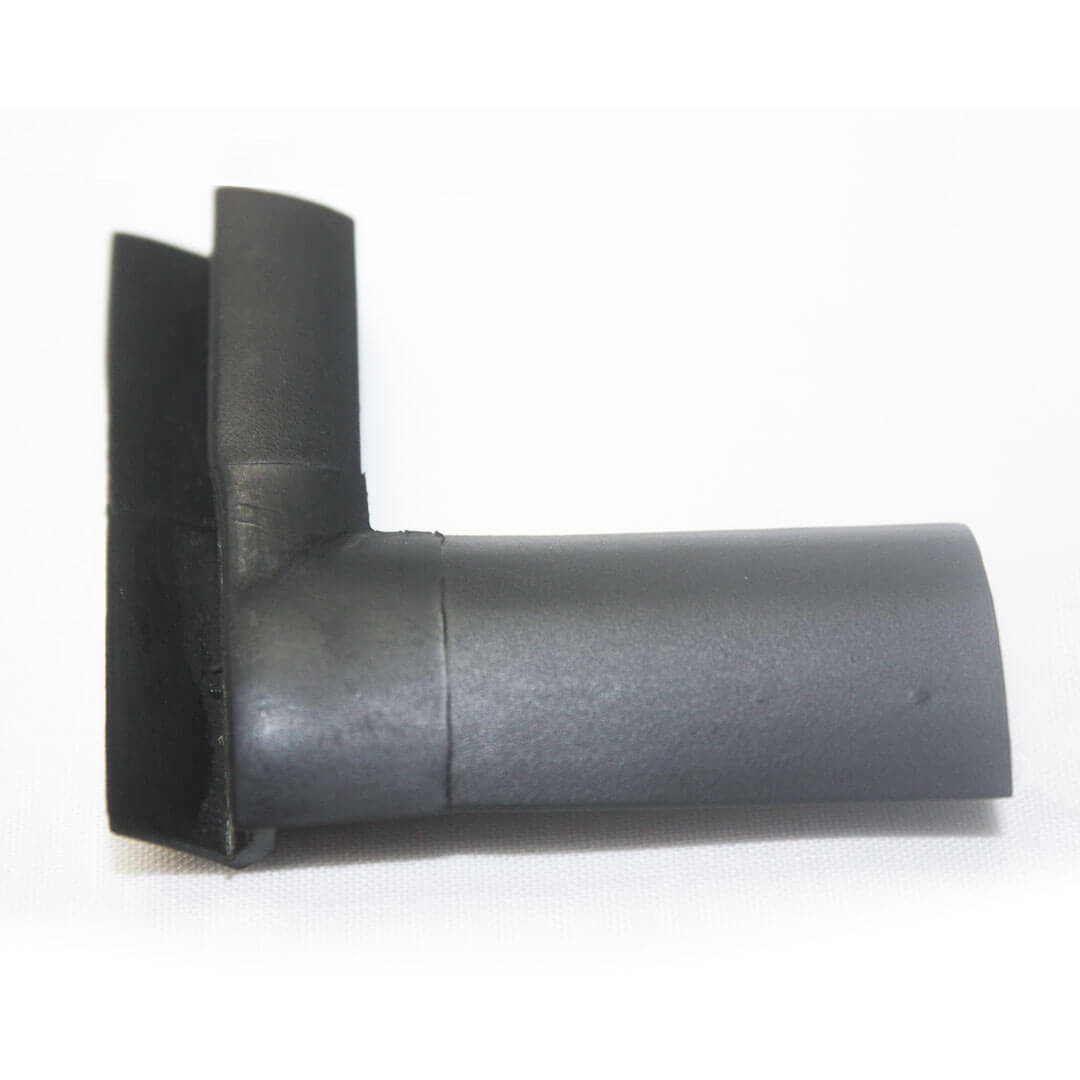
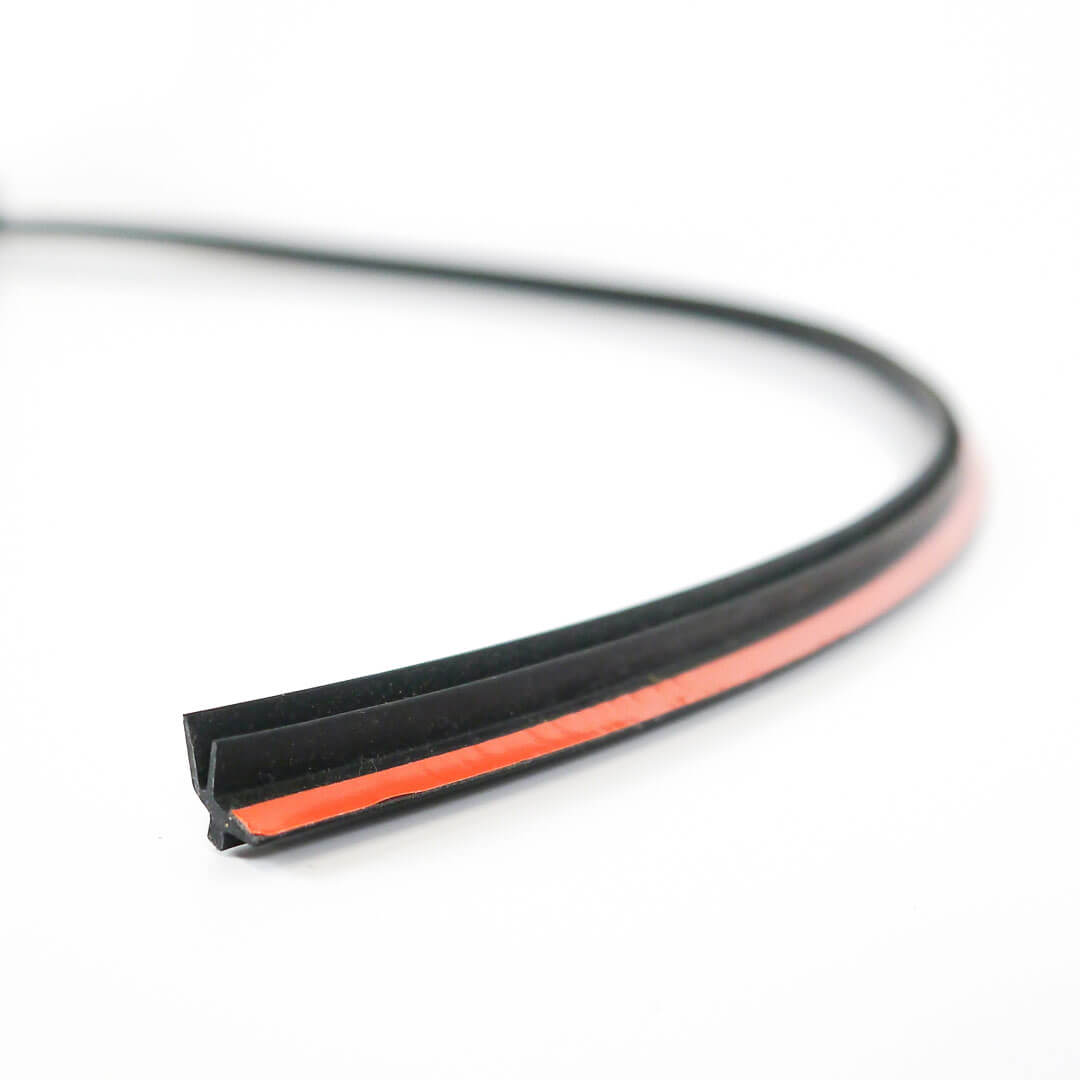
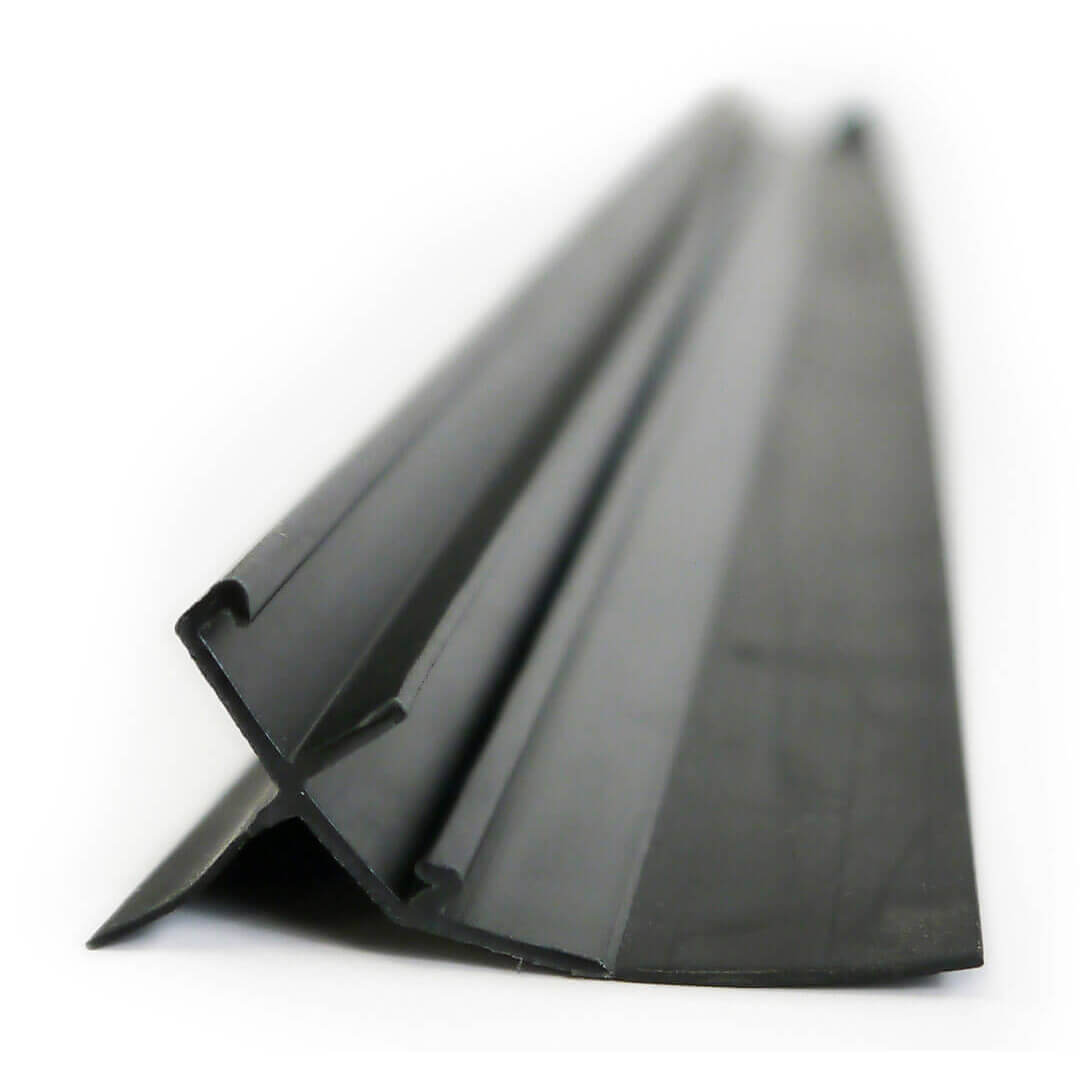
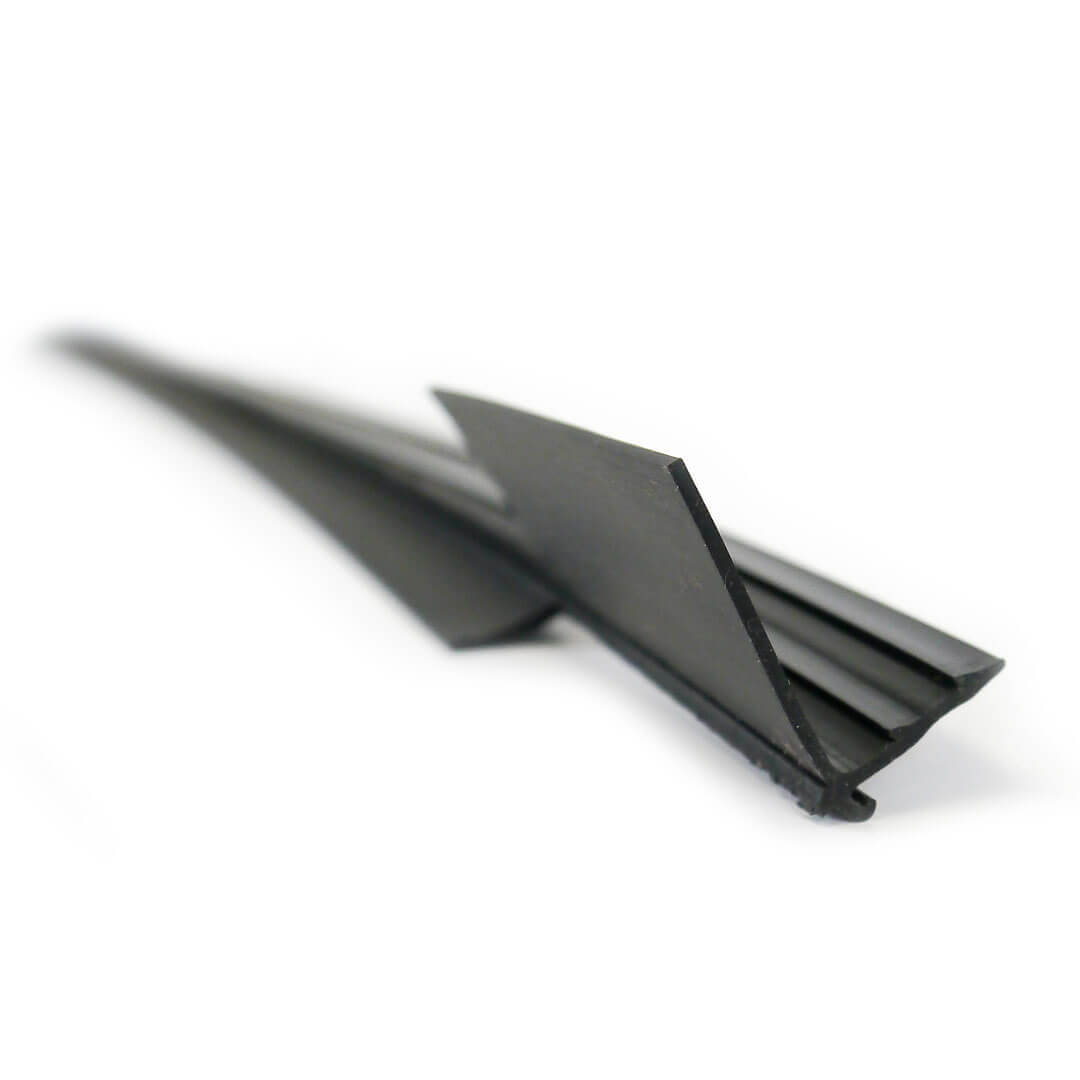
Engineering Support
We’re not just a manufacturer, we’re a partner in engineering. We take a DFMA approach to everything we do. This allows us to simplify, re-engineer, and drive cost out of your extruded seal, all while maintaining or improving its form, fit, and function.
Stringent Standards
With dozens of automotive OEM and Tier 1 customers across the globe, we’re more than capable of meeting and surpassing tough quality standards, delivery demands, and budget constraints for high-volume orders. You can rest easy knowing we’ll get the job done right.
In-House Tooling
If your seal design can’t be matched to one of our existing 7,000+ extrusion profiles, we’ll design and build the tooling in house. This includes prototype and production dies, trim and fabrication tools, fixtures and gauges, and anything else we need to meet the requirements of your custom extruded seal.
Co-Extrusion
Complex sealing challenges don’t require complex solutions. The co-extrusion process gives us the ability to extrude two or more materials at once on a single extrusion line. Need a soft-grip seal with a rigid base or carrier, and a nearly unbreakable molecular bond between the two? Easy. Co-Ex.
In-Line Processing
We can apply tape, flock, and slip coat to your seal right on the extrusion line, reducing the need for secondary processes and operations.
Secondary Operations
Welding, insert/over molding, and other secondary operations for your seal are done in-house to reduce lead times and non-value added costs such as shipping to another facility.
Minority-Owned
As a Women’s Business Enterprise National Council (WBENC) certified minority-owned business, we proudly contribute to our customers’ supplier diversity programs.
Process Simulation Software
Our extrusion simulation software allows us to balance the material flow before any tooling is cut. This reduces the number of tool iterations, allows for a quicker completion of production tooling, shortens your time-to-market, and ultimately saves on manufacturing costs.
ONE OF MANY EXTRUDED SEAL APPLICATIONS: AUTOMOTIVE
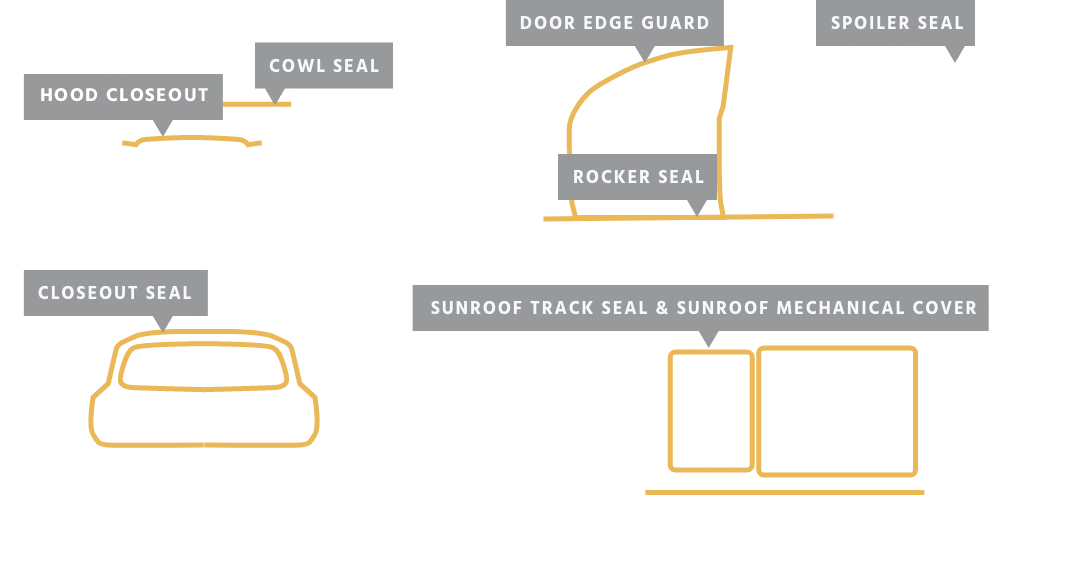
From your home to the office, from school to the sports field, beneath your feet and above your head, extruded seals are everywhere! There are hundreds of applications in automotive, alone. Let’s take a look.
automotive extruded seals
- Air Guides/Deflectors
- Sunroof seals
- Hood seals
- Cowl seals
- Instrument panel seals
- Pillar seals
- HVAC seals
- Condenser seals
- Closeout seals
- Windshield laces
- Rocker Seals
- Roof Line Seals
- Radiator seals
- Belt Line Seals
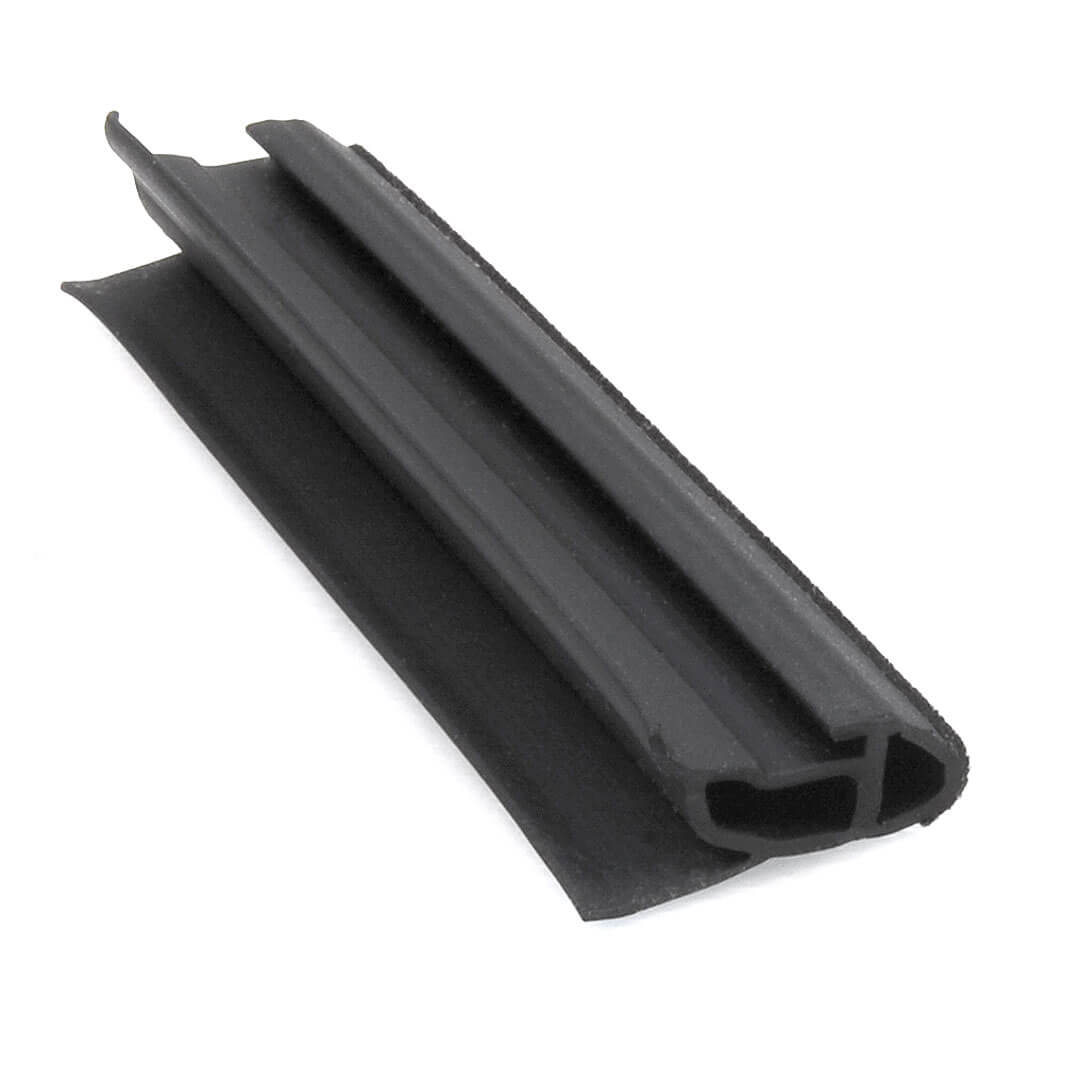
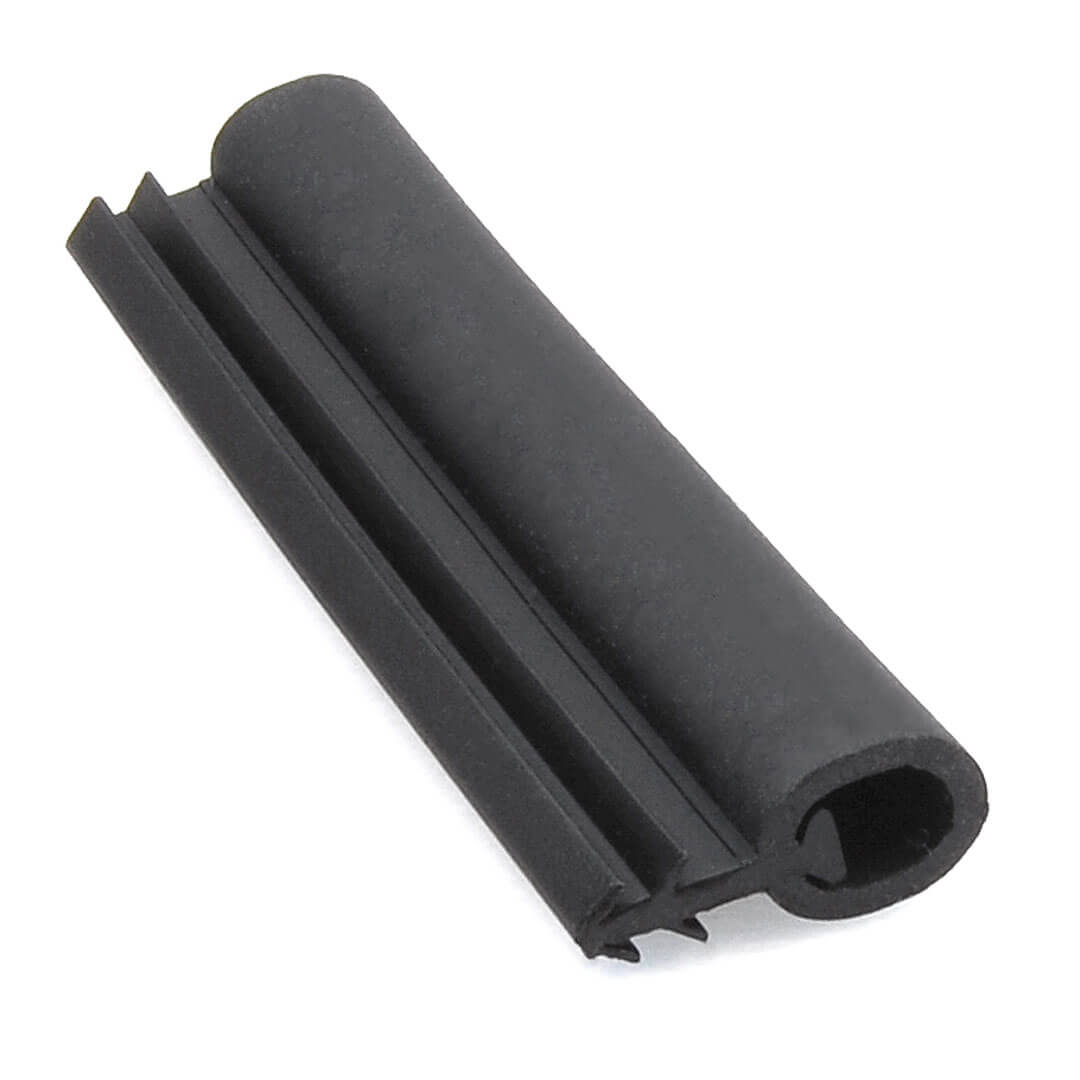

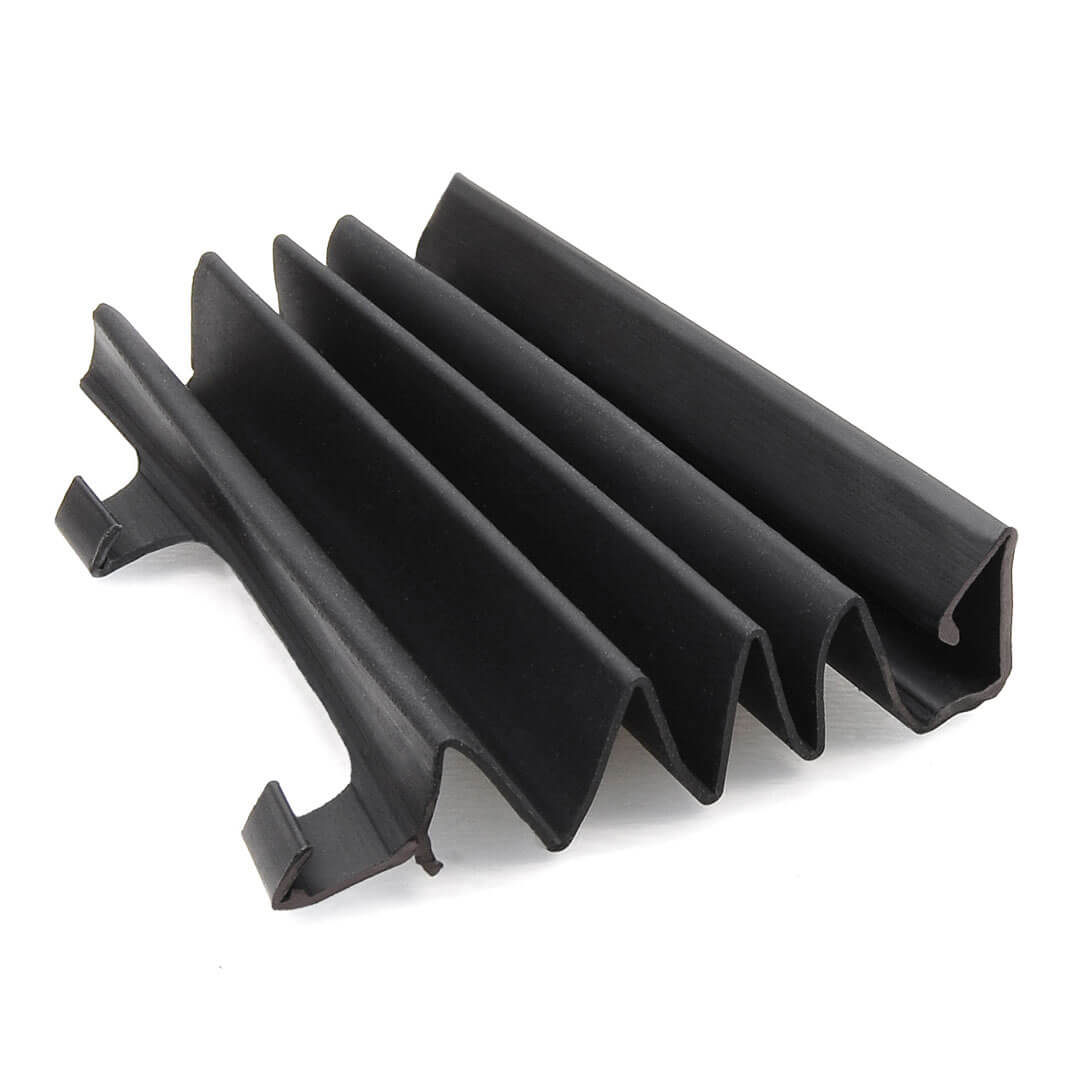
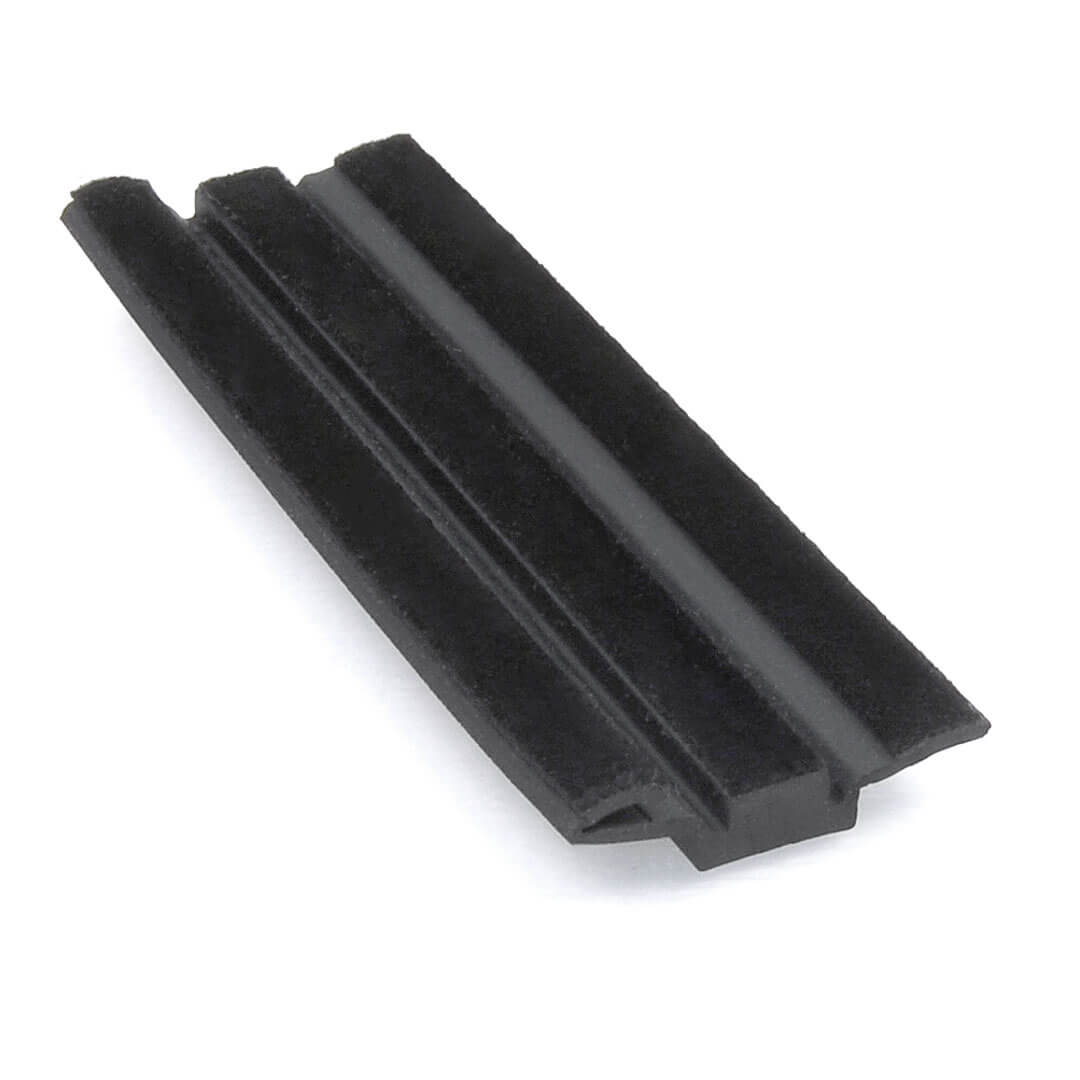
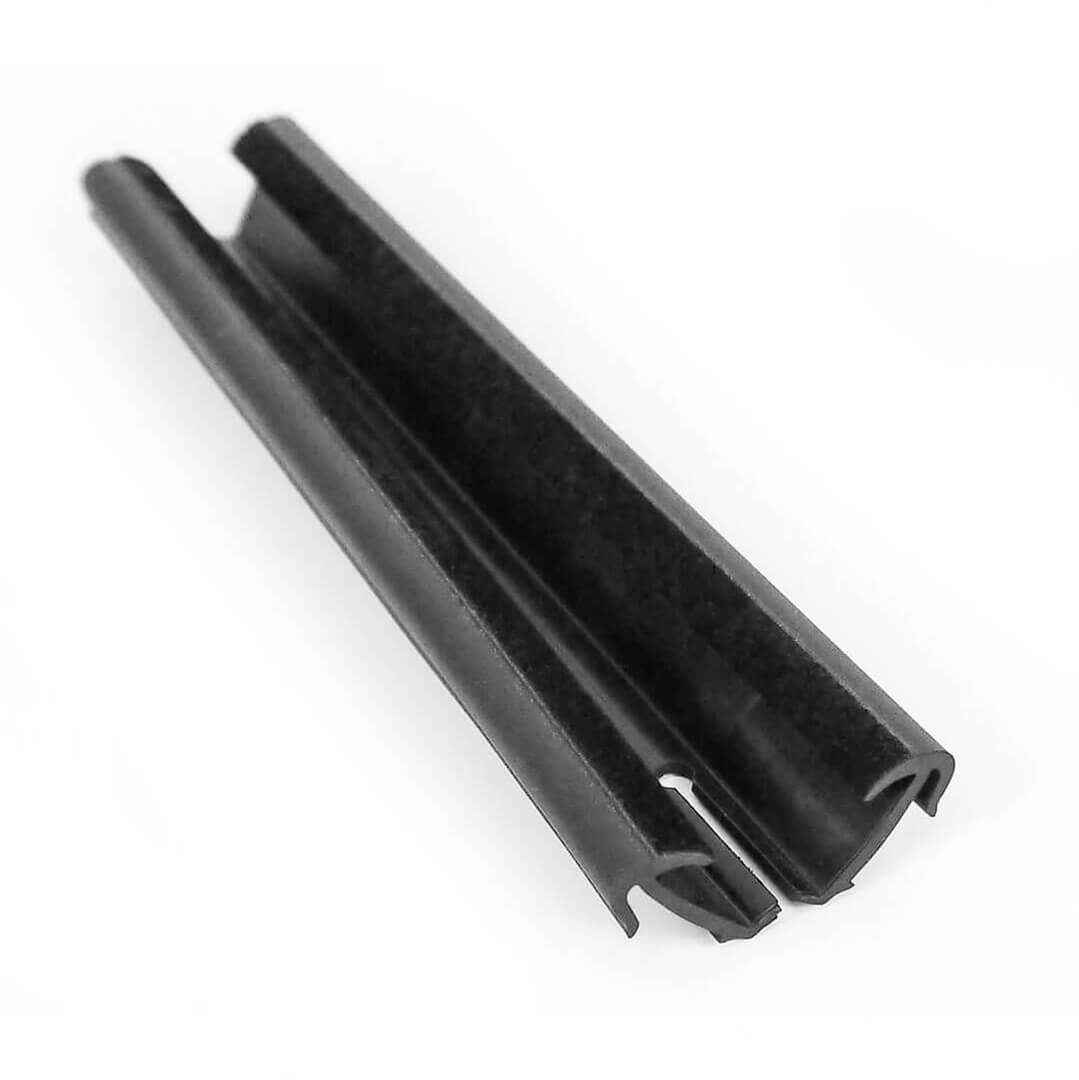
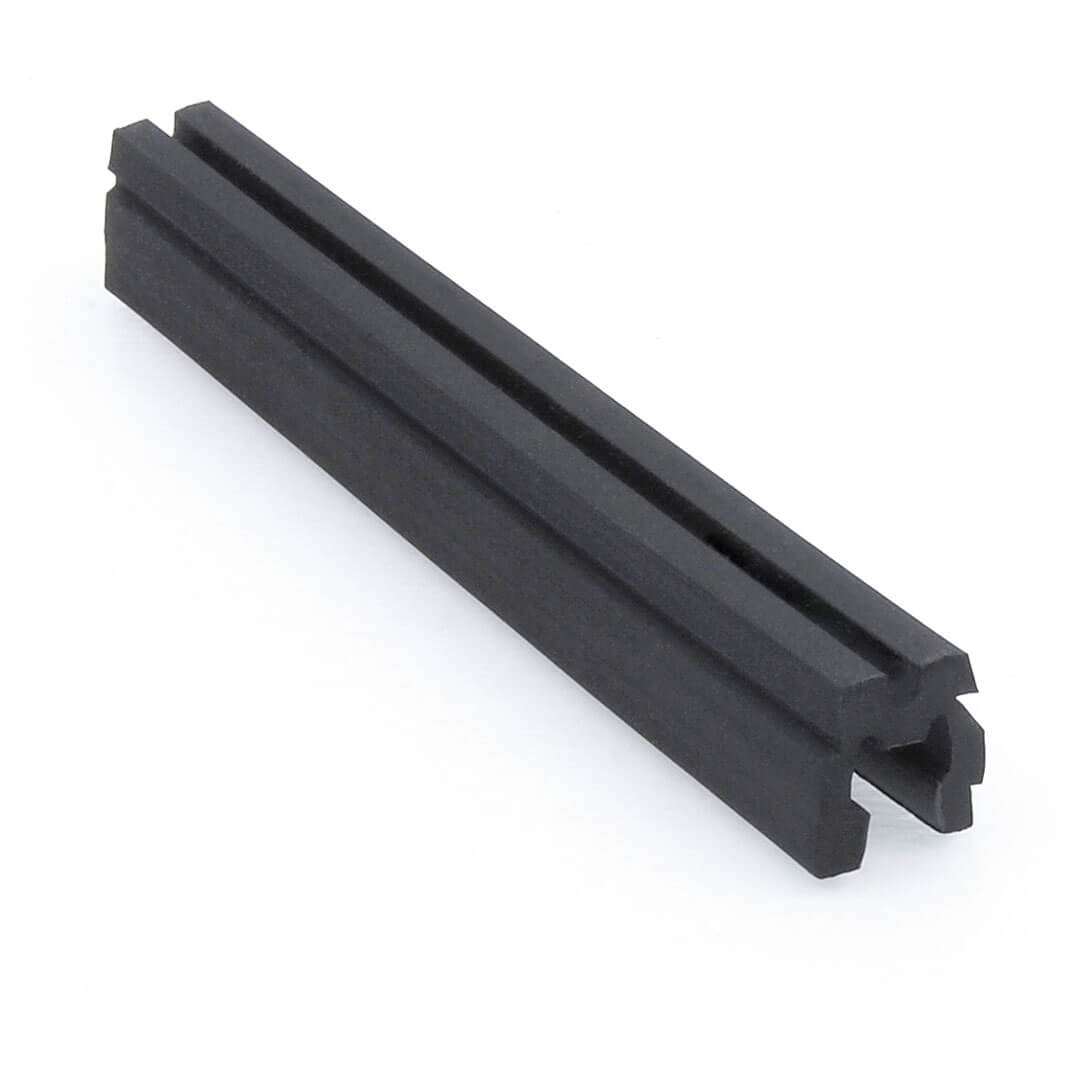
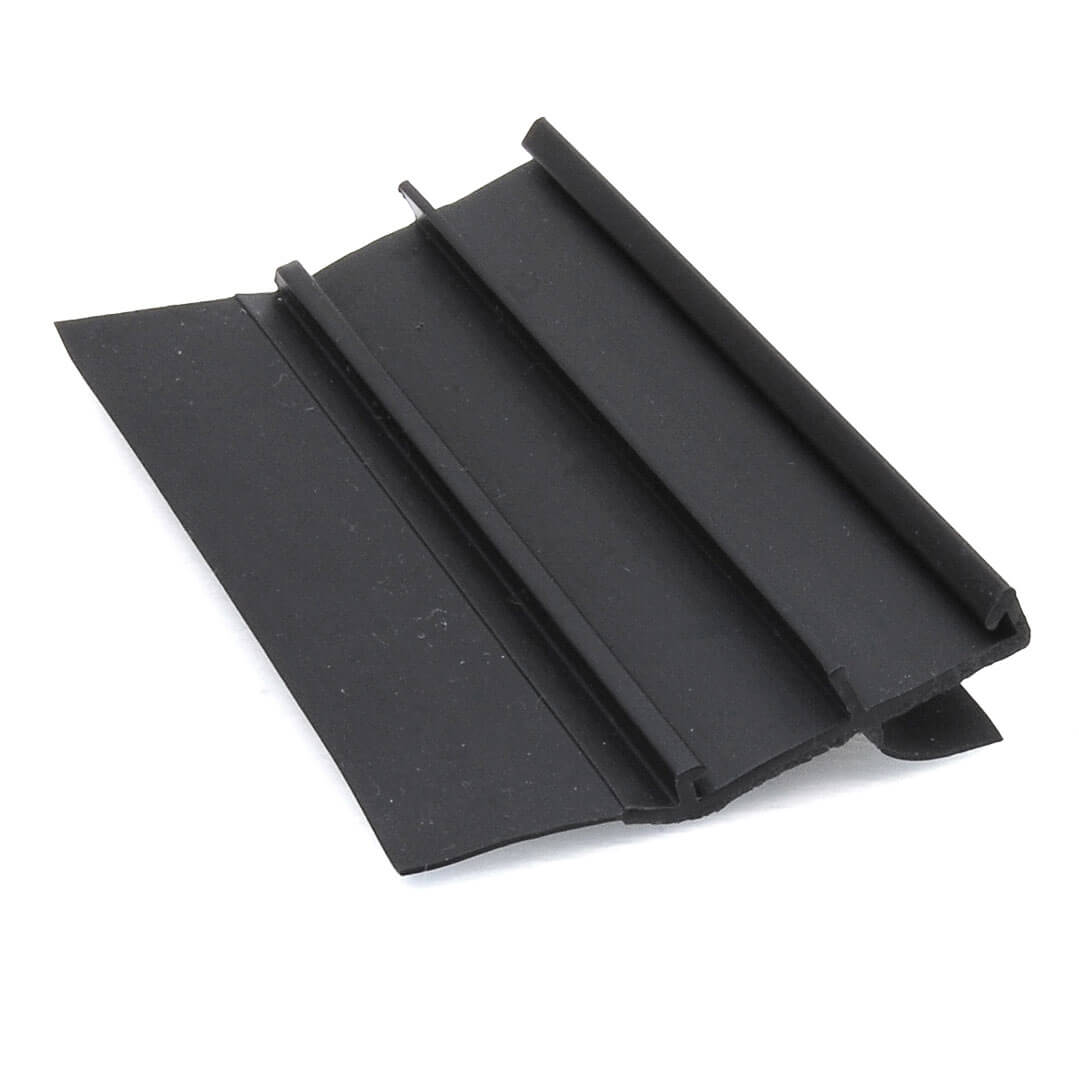
EXTRUDED SEAL COST-DRIVERS
Cost creep can kill your extruded seal program. While it’s impossible to predict every single cost an extruded plastic seal program will incur, you can minimize unpredictability and cost-creep by simplifying your design. The following list is by no means exhaustive, but it does cover the major cost-drivers that you should consider:
DESIGN
Typically, the more complex the seal, the more expensive it will be to engineer and manufacture. Features such as hollows, semi-hollows, narrow die sections, non-identical thickness, tight tolerances, and living hinges should be avoided whenever possible.
DESIGN CHANGES
Any change to the quoted extruded seal design can result in increased cost, especially if it happens after the initial tooling has been built. For this reason, we conduct extensive feasibility testing and simulations for our customers before the manufacturing process begins to minimize the risk of expensive design changes.
TOOLING
There is more to tooling than the extrusion die itself. Of course, the more complex the die the more expensive it will be to make, but you should also consider the cost of any trim or fabrication tools you’ll need after the initial seal is extruded, as well as fixtures and gauges to support the seal during secondary operations.
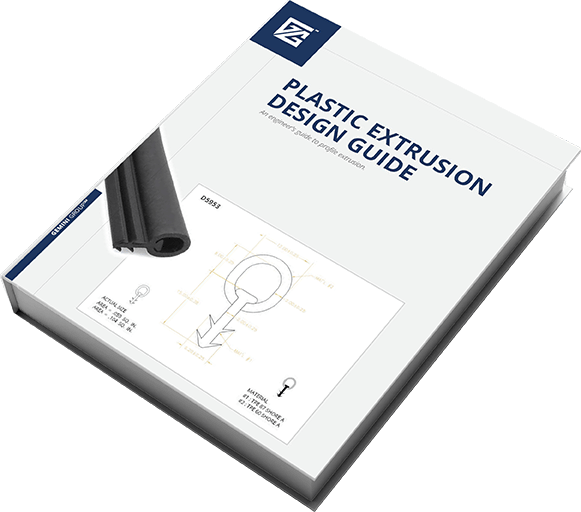
EXTRUDED SEAL DESIGN
We are proud to present to you the cumulation of over 50 years of experience in extrusion. We’ve helped thousands of engineers just like you with their extruded seal design – and this guide truly is the next best thing to working directly with our seals specialists.
Quality & Accuracy
We’re deeply rooted in the automotive industry, and it’s a core part of who we are. With all the necessary certifications, we add value into every product we make. With a track record of shipping over 600 million parts annually, we’re dedicated to delivering successful extruded seals.
That’s why we use the latest in quality control technology before, during, and after the seal extrusion process. But many mistakes happen outside of manufacturing that can negatively impact your seal, too:
Failure to consider all failure modes:
- Exposure to chemical, heat, fatigue, abrasion, tear, set, ozone
- Stresses and strains from the surrounding systems
- Effect of surrounding water management systems
- Packaging and shipping requirements
- Assembly, installation, and service constraints
SUPPLIER INEXPERIENCE:
- Inadequate material options and recommendations
- Inattention to detail or a “shoot-and-ship” culture
- Overestimation of seal tolerances and capabilities
- Lack of experience in packaging and shipping seals
- Underestimating high-volume logistical needs
- Lack of certifications and processes for quality control
Miscommunication:
- Changes with interfacing components and surfaces
- Mismanaged timing, specification, tolerance, and cost expectations
case study
MATERIAL MATTERS: RESCUING A FAILED SEAL IN 5 DAYS
When a Tier 1 OEM supplier had an extruded seal fail just weeks before delivery, we stepped in to help. Five days later, they had a part with improved performance and reduced cost. More importantly, they had a seal that actually worked.
EXTRUDED SEAL TERMINOLOGY
- Blooming: A phenomenon that occurs when compounding agents in rubber migrate, or bloom, to the surface, causing a dusty or milky looking film. This is due to the agents’ limited compatibility with the rubber elastomer and affects the tensile strength, adhesion properties, and appearance of your part.
- Slipcoat: A non-drip lubricant applied to the surface of seals to reduce friction and increase surface smoothness and abrasion resistance.
- Flock tape/spray: An adhesive tape or with a non-woven coating on one side or an adhesive non-woven spray that is used to reduce friction between two surfaces or reduce reflection.
- Hollow: A hollow area, usually ¼” to 5” in diameter, in a profile design made by placing a pin or mandrel inside the die.
- Durometer: A measurement used to indicate the hardness of a material, defined as a material’s resistance to permanent indentation.
- Compression set: The permanent indentation remaining when a force that was applied to a material is removed. There are two ways to measure compression set: Compression set A measures the materials thickness before and after pressure is applied. Compression set B measures the material thickness after the material is compressed to 25% of its original height.
- Insertion/extraction forces: The forces applied to the seal during assembly and disassembly in its final application.
- Insert molding: Molding one material (plastic) around another (metal) such that the final component is single unit with reduced assembly and labor costs, reduced the size and weight of the part, improved component reliability, and improved part strength and structure with enhanced design flexibility.
EXTRUDED SEAL FAQS
What material is best for sealing?
There is no “one size fits all” material that works for every seal application. That’s why we’ve developed The Engineers’ Guide to Selecting an Extruded Seal Material. It provides stats and specs for dozens of extrusion materials and will guide you through the most critical considerations so you can make the best choice possible for your unique application.
How can I prevent my extruded seal from buzzing, squeaking, and rattling (BSR)?
Buzzes, squeaks, and rattles (BSRs) are 100% preventable, yet they remains a major source of warranty claims. This is typically the result of improper material friction characteristics, chemical reactions, and/or environmental factors.
To prevent seal chatter, take a look at the surrounding system.
- To what, and how, will the extruded seal be attached?
- What is its proximity to other components?
- Will it be exposed to extreme temperatures, chemicals, or ozone?
Once you have an understanding of the application’s environment, you can predict potential BSRs and determine the best method of prevention. Some of the most common solutions include the application of a slip-coat, blending a slip-agent directly into the seal material, and applying flock tape or spray to exposed surfaces.
How can I prevent a rubber seals from staining or bleeding?
Staining and bleeding have long plagued rubber seal applications. Fortunately, you can prevent it.
Staining happens when additives in the rubber have some solubility with a mating surface; such is the case with the infamous rubber-footed table stain in the linoleum-floored kitchen. You can prevent this by creating a barrier between the mating materials.
Bleeding is the seepage of rubber additives, namely oils. There are some rubber compounds that are resistant to bleed, but the only way to prevent it entirely is to use an alternative material such as TPV.
What is the white powdery substance that builds up on the surface of a rubber part?
This phenomenon is referred to as “blooming,” and occurs when compounding agents in the rubber migrate, or bloom, to the surface. This is due to the agents’ limited compatibility with the rubber elastomer. It affects the tensile strength, adhesion properties, and appearance of your part.
What are the alternatives to rubber seals?
Depending on your seal application, you may have numerous alternatives to rubber. The most common is thermoplastic vulcanizate (TPV), a rubber-like material that can be processed and recycled like plastic, but without the stain, smell, and blooming you see with rubber. It’s like a simplified rubber, allowing for more flexible part design, quicker manufacturing, reduced part/system costs, and weight reduction.
Other thermoplastic alternatives to rubber include TPO, TPU, TPZ, and PVC.
To help you navigate the sea of options, we’ve developed the The Engineers’ Guide to Selecting an Extruded Seal Material.
Wherever You’re Located, We’re Here to Help
17 strategic locations in North America to meet the needs of our diverse customer base.
Insights
Get to know us. Get in touch today.
We have the resources to meet any part or production challenge. Let’s talk about what that means for you.
"*" indicates required fields