Table of Contents
Aluminum Extrusion Process
The aluminum extrusion process is a highly efficient and versatile manufacturing technique used to produce aluminum parts with varying cross-sectional profiles.
Of all the tooling involved, the most crucial component is the extrusion die. It plays a pivotal role in the process, shaping the aluminum as it is forced through the die opening under immense pressure, and requires incredible precision and reliability.
The extrusion process typically involves the following steps:
- Billet preheating: Aluminum billets (solid cylindrical logs) are preheated to the desired temperature depending on the alloy, typically around 700-930°F (370-500°C), to achieve the required plasticity for extrusion.
- Container loading: The preheated billet is loaded into a heat container, which is part of the extrusion press.
- Ram advancement: A hydraulic ram applies immense pressure, typically ranging from 1,000 to 15,000 tons, to force the softened aluminum through the die opening.
- Profile extrusion: As the aluminum is pushed through the die, it takes on the shape of the die opening, forming the desired profile.
- Profile cooling and handling: The extruded profile is cooled, either by air or water, and then transferred for further processing, such as stretching, machining, and surface treatments.
Throughout the extrusion process, the die plays a critical role in maintaining dimensional accuracy, surface finish, and overall product quality. Factors such as die design, material flow, and thermal management significantly influence the extrusion quality and efficiency.
What is an Aluminum Extrusion Die?
Types of Aluminum Extrusion Dies
Aluminum extrusion dies can be broadly classified into three main categories based on their design and intended use: solid, hollow, and semi-hollow. Each one is comprised of multiple components, together referred to as the “die stack.”
Solid Dies
Solid dies are used for producing solid aluminum profiles without any cavities. These dies are suitable for simple shapes, such as bars, angles, and channels. Solid dies are typically less complex and more cost-effective compared to other die types.
The three components of a solid die stack include the feeder, the die itself, and the backer.
- Feeder: In some cases, a feeder, also known as a weld plate, is needed to provide additional control over the flow of the aluminum, facilitating the continuous flow from one billet to the next and controlling the contour and the spread of the aluminum.
- Die: The die itself contains the final opening the aluminum passes through, creating the finished profile shape.
- Backer: The backer is used to reinforce the die during the extrusion process. It can also aid as a thermal barrier from the bolster, preventing the die from losing too much heat.
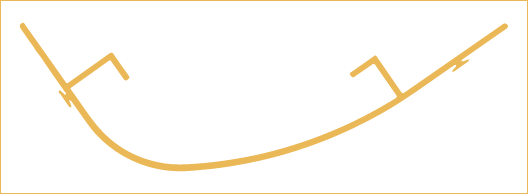
Hollow Dies
Hollow dies are designed to produce aluminum profiles with internal cavities or hollow sections. These dies are ideal for complex shapes, such as tubes, window frames, and structural members with internal reinforcements.
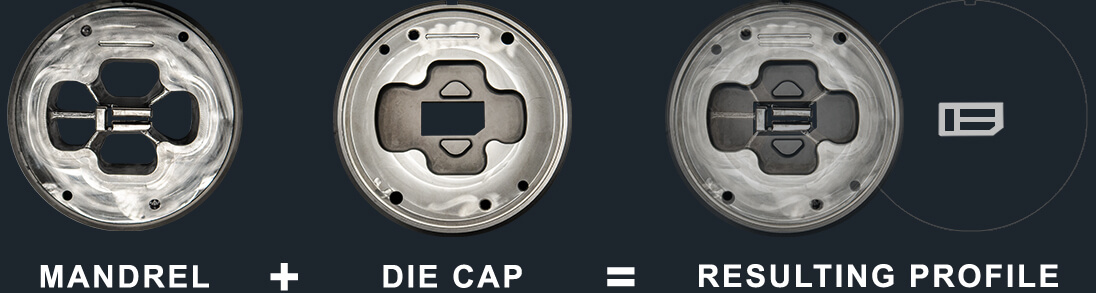
The three components of a hollow die stack include the mandrel, the die cap (or die plate), and backer.
- Mandrel: The mandrel holds a void that creates the hollow section of the die. Aluminum flows around the void to form the desired hollow shape.
- Die Cap/Plate: The die cap, also known as the die plate, is the outer part of the die that holds the mandrel in place and shapes the outer contour of the aluminum profile. It has an opening that matches the desired outer shape of the final product.
- Backer: Just like a solid die, hollow dies require a backer to reinforce the die during the extrusion process. It can also help with thermal management, preventing the die from losing too much heat.
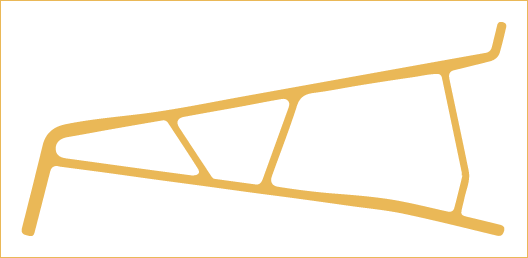
Semi-Hollow Dies
Semi-hollow dies combine elements of both solid and hollow dies. They’re used to produce aluminum profiles that have both solid and hollow sections within the same cross-section. These dies offer versatility in profile design and can accommodate complex geometries with varying wall thicknesses.
Profile Shapes
Aluminum extrusion dies can be designed to produce a wide range of profile shapes and configurations, ranging from standard profiles to highly customized designs.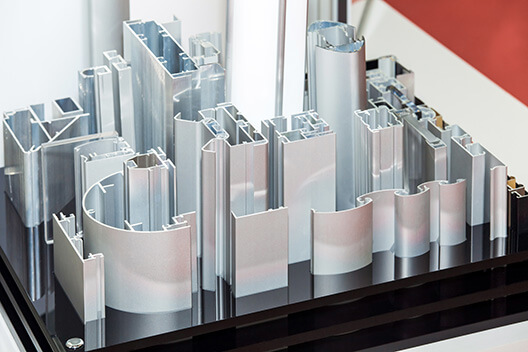
Common die profile categories include:
- Channels and angles
- Rod and bar
- Architectural/building construction profiles
- Automotive and transportation (truck/trailer/RV) profiles
- Industrial and structural profiles
- Custom profiles for specific applications
Additional Tooling
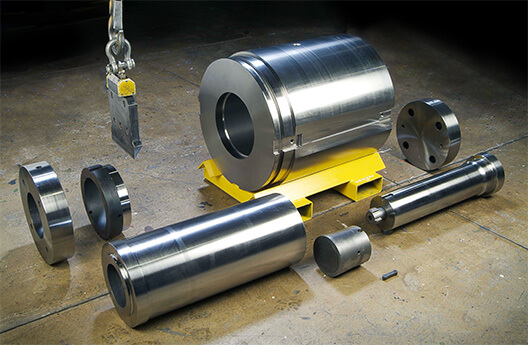
Support Tooling
It takes 300 tons to crush your average pickup truck; the force on the die could crush 50. For this reason, the die requires heavy support tooling to ensure it stays perfectly aligned and secure during the process.
For this reason, the die requires heavy support tooling to ensure it stays perfectly aligned and secure during the process.Support tooling requirements vary greatly depending on the type of die being used and the operating parameters of the press.
Key support tooling components often include the die ring, backer, bolster, and sub-bolster.
- Die ring: The die ring is a sleeve that encases the die, and when present, the feeder and backer. It provides additional support and alignment, ensuring the die assembly remains in the correct position during extrusion.
- Backer: The backer is a steel disk with the same diameter as the die, but usually two-three times as thick. It’s used to reinforce the die against the pressure from the billet.
- Bolster: A bolster is similar to the backer, but much thicker. It provides support, alignment, and even pressure distribution.
- Sub-bolster: A sub-bolster is a second bolster that is used when the die stack is too short to fit the extrusion press. It extends the length of the die stack to meet length requirements.
Press Tooling
The aluminum extrusion process relies on a comprehensive set of press tooling to control the temperature of the billet and push the aluminum through the die.
Press tooling is required regardless of what type of die being used. Key press tooling components include the stem, dummy block, container, container liner, die slide, and horse shoe.
- Stem: The stem is placed between the ram and the dummy block to extends the reach of the ram as it moves the billet through the length of the heat container and die stack.
- Dummy block: The dummy block is placed between the stem and the billet to shield the stem, prevent back feeding of the hot billet, and help distribute pressure evenly across the billet.
- Container: The container holds the aluminum billet and helps maintain optimal temperature as it is pushed through the die stack by the dummy block.
- Container liner: The container liner is a protective sleeve inside of the heat container that reduces wear and improves the performance of the container.
- Die slide: Located between the container and press, the die slide supports and aligns to the press and retains the die tooling for the profile, as a unit.
- Horse shoe: The horseshoe is U-shaped device with that holds and aligns the die ring or housing in the die slide.
Proper tooling design and maintenance are essential for achieving optimal extrusion performance and minimizing downtime and production disruptions.
Effective Die Design
Effective die design is a critical aspect of the aluminum extrusion process, as it directly impacts quality, efficiency, and cost-effectiveness.
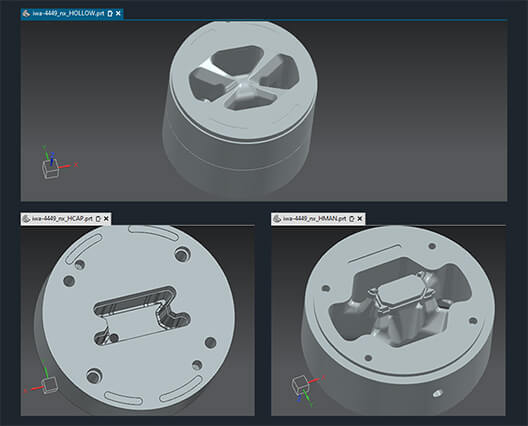
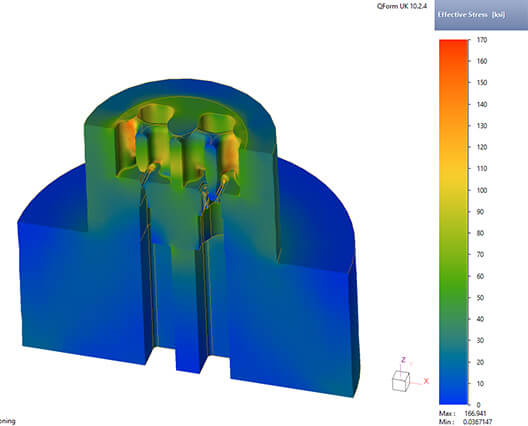
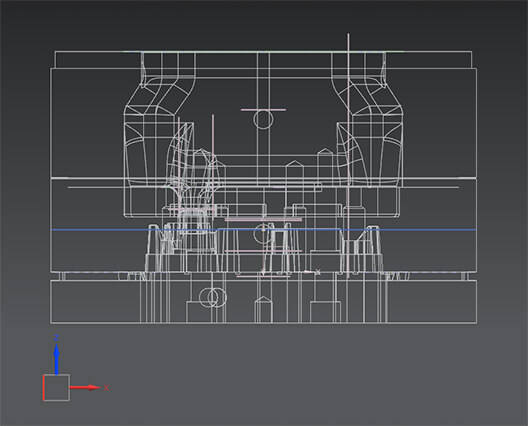
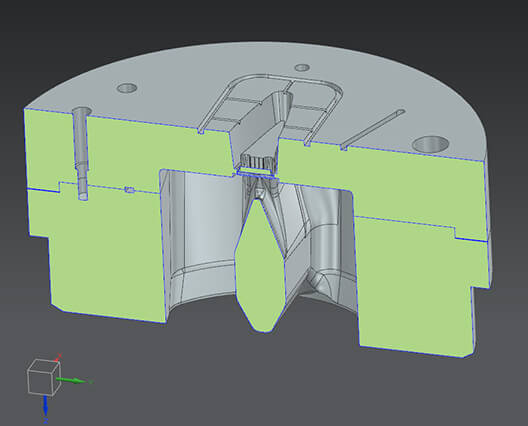
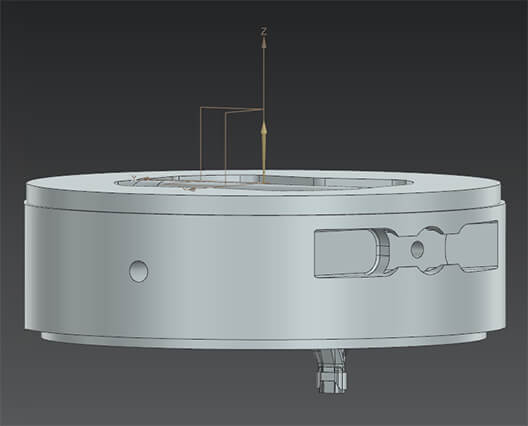
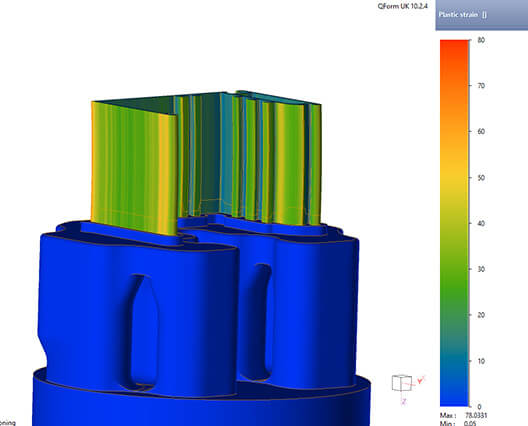
In practice, the design process relies heavily on the experience and intuition of the designers. However, there are several key principles and techniques that designers consider in every die design.
- Uniform material flow velocity: The most important factor to improve the quality of the extrusion and extend die life is to ensure smooth and uniform material flow. This minimizes turbulence, dead zones, and potential defects like warping. Techniques include modifying die bearing lengths, adjusting land lengths, and incorporating flow channels or feeders.
- Optimal bearing length: The bearing length, or the distance the aluminum travels within the die, should be carefully calculated so that all parts of the profile exit the die at the same speed. Longer bearing lengths increase resistance to the flow of aluminum, thus slowing it down, while shorter lengths do the opposite. Therefore, thicker areas of the profile should be slowed with longer bearing lengths to match the speed of thinner areas.
- Finite Element Analysis (FEA): FEA simulations should be used to model the extrusion process and analyze the die’s structural integrity, thermal behavior, and material flow characteristics to identify potential issues before manufacturing the die.
- Thermal management: The temperature of the aluminum as it exits the die largely influences the mechanical properties and surface quality of the extrusion. Effective cooling and heating strategies should be incorporated into the die design to maintain consistent temperatures and prevent defects caused by thermal variations.
- Surface engineering: Advanced surface treatments and coatings like nitriding, chromium plating, or hard coating enhance die performance, improves wear resistance, extends die life, and contributes to the smoothness of the extrusion.
- Material selection: Choosing the right material is crucial to ensure performance and durability. H13 is sufficient for nearly all dies due to its excellent thermal conductivity, wear resistance, and toughness.
Cost Considerations
The cost of an aluminum extrusion die is influenced by various factors that affect both the initial investment and ongoing expenses.
- Design and planning: Efficient die design and process planning are essential for reducing overall costs. Utilizing advanced design tools such as feature-based neural networks and CAD systems helps optimize the design process, minimizing errors and rework.
- Die maintenance and rework: Routine maintenance and repair must be accounted for. Efficient die correction operations help extend die life, minimize downtime, and reduce costs associated with die failures.
- Die material: Material selection is a balancing act of initial production costs, performance, and die life. Despite their higher initial cost, high-quality tool steels like H13 is usually preferred due to superior wear resistance and durability, leading to long-term savings in downtime, maintenance, and repair.
- Complexity of the profile: More complex profiles with intricate details or internal features generally require more extensive manufacturing processes, increasing the cost of the die. Further, the more complex the die, the higher the maintenance and wear, thus increasing ongoing expenses.
- Manufacturing process: The specific manufacturing techniques employed, like CNC machining, wire EDM, or surface treatments, can influence the die cost. Advanced machining processes can increase precision, but come with higher initial costs. Surface treatments such as nitriding or coatings enhance durability but add to the initial manufacturing cost.
- Production volume: Higher production volumes may justify investing in more expensive die materials or manufacturing processes to extend die life and reduce overall cost per unit.
To balance cost and performance, manufacturers often employ cost-saving strategies, such as:
- Utilizing standardized die profiles when possible
- Optimizing die design for improved material flow and reduced wear
- Implementing preventive maintenance and rework programs to extend die life
Maintenance and Troubleshooting
Proper maintenance and troubleshooting of aluminum extrusion dies are essential for ensuring consistent performance, maximizing die life, and minimizing downtime.
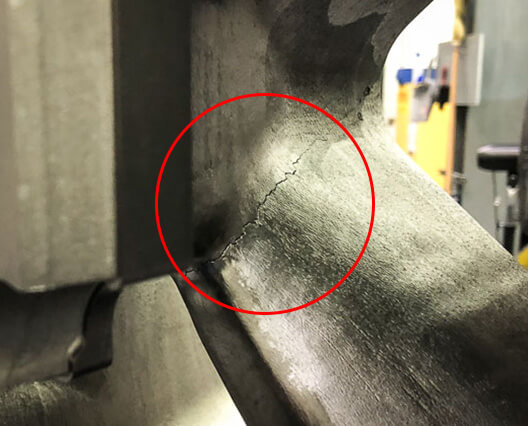
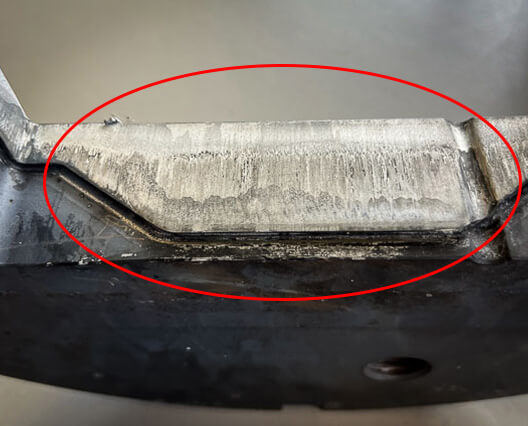

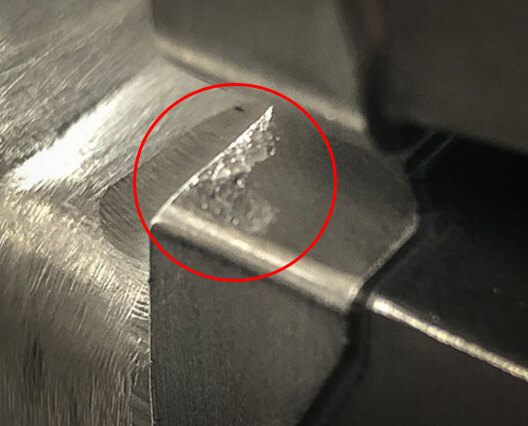
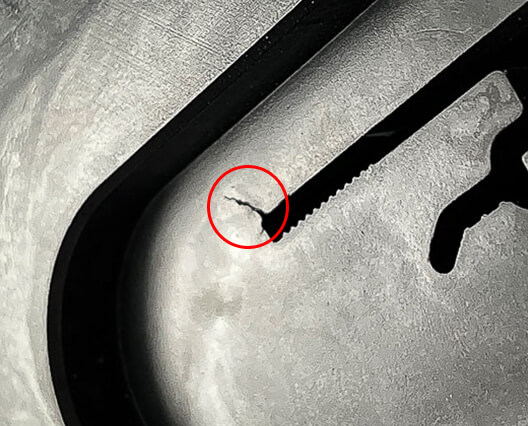
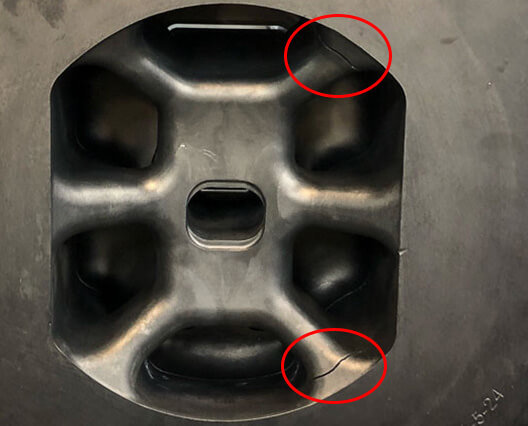
Some common die issues and maintenance practices include:
- Wear and tear: Over time, the die opening experiences wear due to the high pressures and temperatures involved in the extrusion process. Regular inspections and preventive maintenance, such as resurfacing or repolishing, can extend die life.
- Surface defects: Defects like scratches, dents, or buildup on the die surface can lead to imperfections in the extruded profile. Proper cleaning and surface treatment can help mitigate these issues.
- Thermal management: Uneven heating or cooling of the die can cause distortion, cracking, or inconsistent material flow. Ensuring proper thermal management through effective cooling systems and insulation is crucial.
- Alignment and support: Misalignment or inadequate support for the die assembly can result in dimensional inaccuracies or premature die failure. Regular checks and adjustments are necessary to maintain proper alignment.
- Preventive maintenance: Implementing a comprehensive preventive maintenance program, including regular inspections, cleaning, and refurbishment, can significantly extend die life and reduce unplanned downtime.
Collaboration and Communication
Successful aluminum extrusion projects often involve a collaborative effort among various stakeholders, including die designers, manufacturers, extruders, and end-users.
Effective communication and coordination is essential for achieving desired outcomes.
- Designers: Die designers play a crucial role in translating product requirements into optimized die designs that meet performance, quality, and cost objectives. Close collaboration with manufacturers and extruders is necessary to ensure that the die design is compatible with the available manufacturing processes and extrusion capabilities.
- Manufacturers: Die manufacturers, on the other hand, contribute their expertise in die fabrication, material selection, and production processes. They work closely with in-house or external die designers to ensure that the design is manufacturable and can be produced within the specified tolerances and quality standards.
- Extruders: Extruders bring their extensive knowledge of the extrusion process, including press capabilities, tooling requirements, and process parameters. Their input is invaluable in ensuring that the die design and fabrication align with the intended extrusion conditions and production requirements.
- End-users: End-users or customers provide critical insights into the functional requirements, performance expectations, and application-specific considerations that should be factored into the die design and extrusion process.
By fostering open communication channels and encouraging regular information exchange among these stakeholders, potential issues can be identified and addressed early in the project lifecycle.
This collaborative approach not only ensures successful die design and fabrication but also facilitates continuous improvement and innovation in the aluminum extrusion industry.
Industry Standards and Best Practices
Adhering to industry standards and best practices is essential for ensuring product quality, safety, and compliance with regulatory requirements.
Some notable organizations and associations responsible for setting these guidelines for the aluminum extrusion industry include:

Aluminum Extruders Council (AEC)
The AEC publishes guidelines and best practices for aluminum extrusion processes, including die design, tooling, and extrusion parameters.

European Aluminium Association (EAA)
The EAA has developed standards and guidelines specific to the European aluminum industry, covering aspects such as alloy specifications, extrusion practices, and quality assurance.

International Organization for Standardization (ISO)
ISO standards cover various aspects of aluminum extrusion, including material specifications, dimensional tolerances, and quality management systems.

ASTM International
ASTM provides standards for aluminum alloy designations, mechanical properties, and testing methods, which are widely recognized and adopted globally.
In addition to adhering to industry standards, implementing best practices in die design, manufacturing, and extrusion processes is crucial for achieving optimal performance and quality.
Best practices include:
- Utilizing advanced design tools and simulation software for die optimization
- Implementing robust quality control measures during die fabrication
- Conducting thorough testing and validation of new die designs
- Establishing preventive maintenance and refurbishment programs for die tooling
- Promoting continuous improvement through regular process reviews and knowledge sharing
By embracing industry standards and best practices, manufacturers can ensure compliance, enhance product quality, and foster a culture of excellence within the aluminum extrusion industry.
Emerging Trends and Future Developments
The aluminum extrusion industry is continuously evolving, driven by technological advancements, changing market demands, and a focus on enhancing efficiency, precision, and the lifespan of dies.
Several emerging trends and future developments are shaping the landscape of aluminum extrusion technology:
- Artificial intelligence: AI and machine learning are increasingly used to optimize die design and process parameters to improve efficiency and reduce waste. These systems leverage data analytics and machine learning algorithms to identify potential design and process issues, predict optimal extrusion parameters, and facilitate predictive maintenance.
- Advanced coatings: There is ongoing development of new coatings, however in our experience as aluminum extrusion tooling specialists, more R&D is required before they’re viable or cost-effective for most applications.
- Additive manufacturing for die production: One significant advancement is the application of additive manufacturing for creating complex die geometries. Technologies like selective laser melting (SLM) allow for the production of dies with integrated conformal cooling channels, which enhance thermal management and increase productivity.
- Simulation and modeling: The use of advanced simulation software and modeling techniques is becoming increasingly prevalent in die design and optimization. These tools allow for virtual prototyping, predictive analysis of material flow and thermal behavior, and streamlined design iterations, ultimately leading to more efficient and cost-effective die solutions.
- Sustainable and energy-efficient practices: With a growing focus on environmental sustainability, the aluminum extrusion industry is exploring ways to reduce energy consumption, minimize waste, and implement eco-friendly practices throughout the die lifecycle. This includes optimizing die designs for energy efficiency, exploring alternative materials and manufacturing processes, and implementing recycling and reuse initiatives.
These advancements are driving the aluminum extrusion industry towards greater precision, efficiency, and sustainability, meeting the evolving demands of various sectors such as automotive, aerospace, and construction.
A Final Word
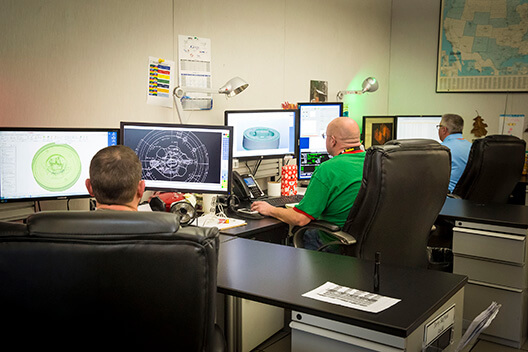
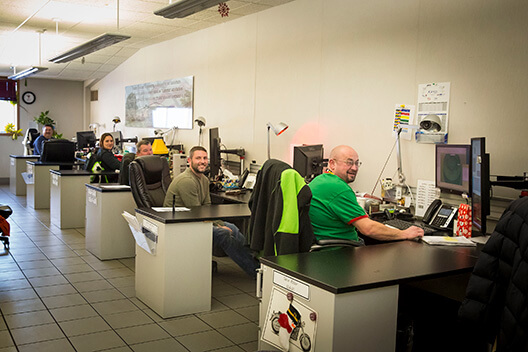
In conclusion, the aluminum extrusion process relies heavily on the precision and reliability of extrusion dies. Understanding the different types of dies, their components, and the supporting and press tooling involved is essential for optimizing the extrusion process.
Effective die design, maintenance, and collaboration among stakeholders ensure high-quality, cost-effective, and efficient production of aluminum profiles. As the industry continues to evolve, embracing emerging trends and developments will be key to maintaining competitiveness and meeting the increasing demands for precision, efficiency, and sustainability.
The aluminum extrusion tooling specialists at Gemini Group are at the forefront of these advancements. Contact us today to learn more and discover how we can help you achieve your production goals.
Get to know us. Get in touch today.
We have the resources to meet any part or production challenge. Let’s talk about what that means for you.
"*" indicates required fields