INTRICATE DESIGNS WITHOUT THE HEADACHE
Fluid reservoirs and tanks require complex geometries in order to fit between existing system components under hood. Oftentimes last minute engineering changes in the surrounding environment require a design change to the reservoir or tank.
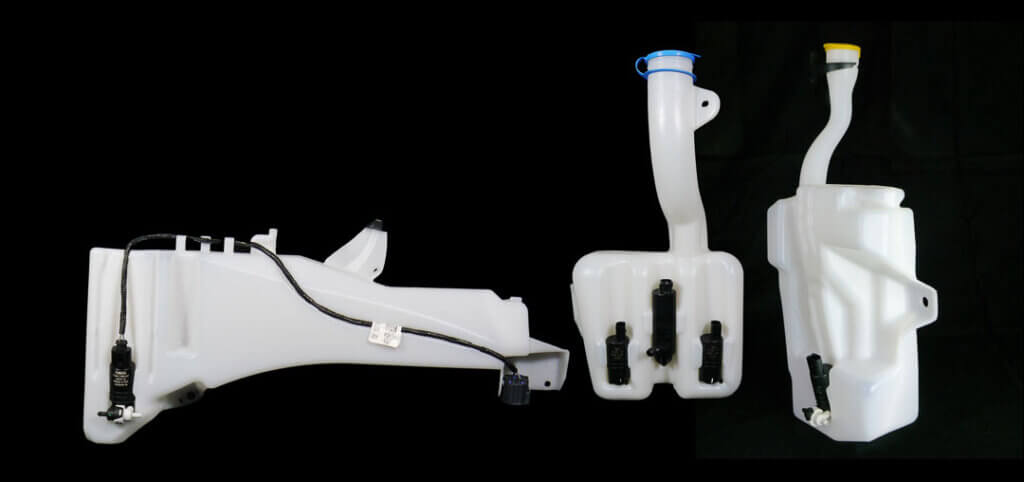
Working with a supplier who understands these nuances will help you mitigate risk and ensure the timely delivery of high-quality parts. That’s why OEM’s and Tier 1 automotive suppliers choose on us to assist with the development and refinement of their part designs.
Blow-Molded Air Intake Components
The whole is greater than the sum of its parts until one of those parts fails. That’s why it’s so important to scrutinize each component not only on its own but also as to how it fits into the overall air intake system. That’s what you get when you work with us.
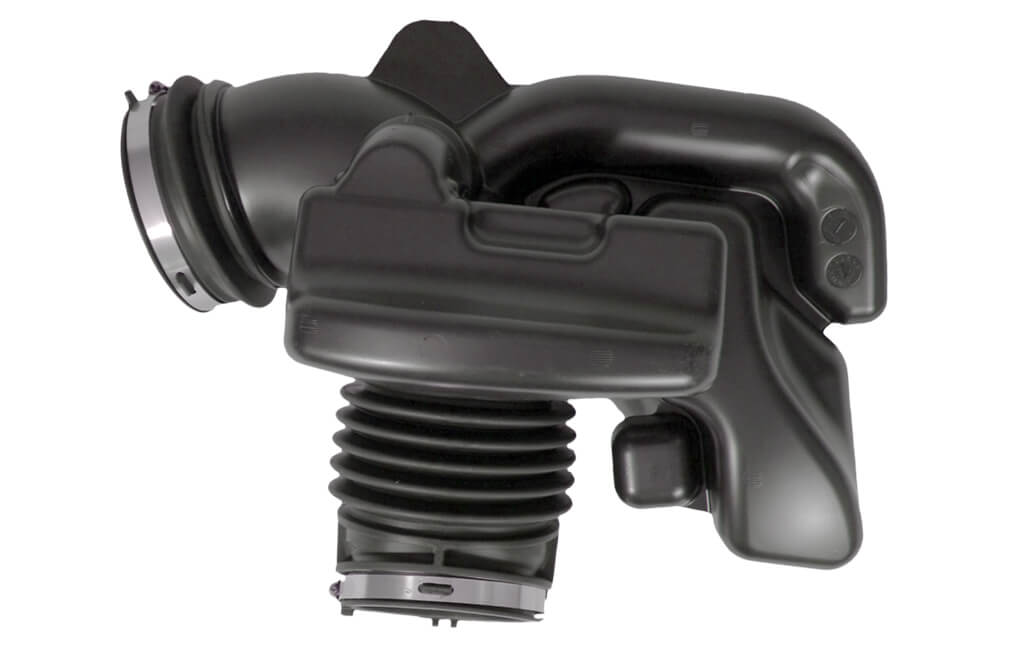
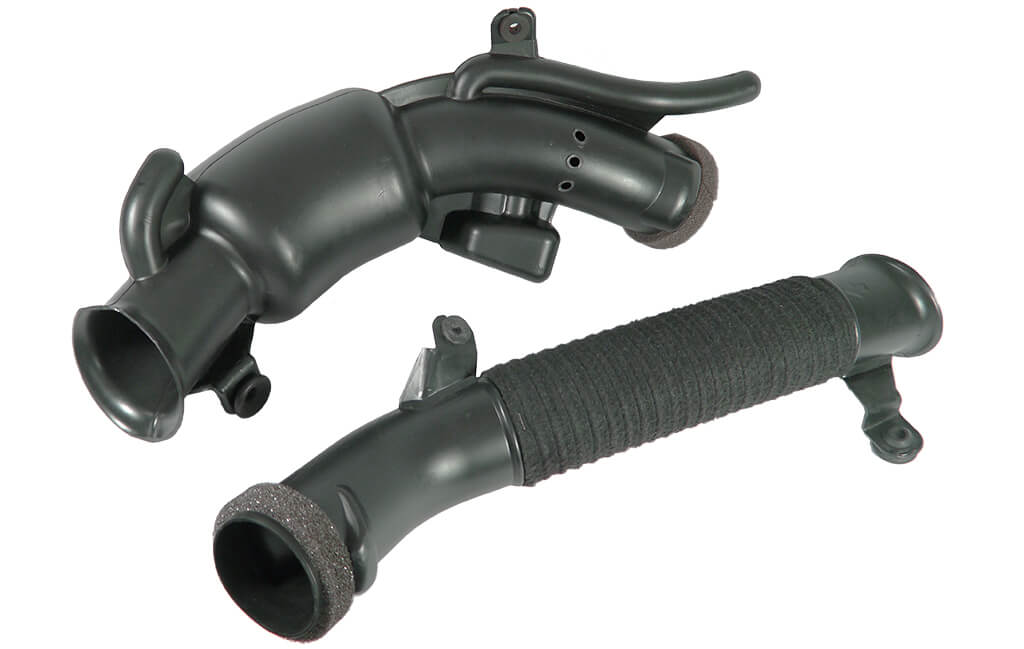
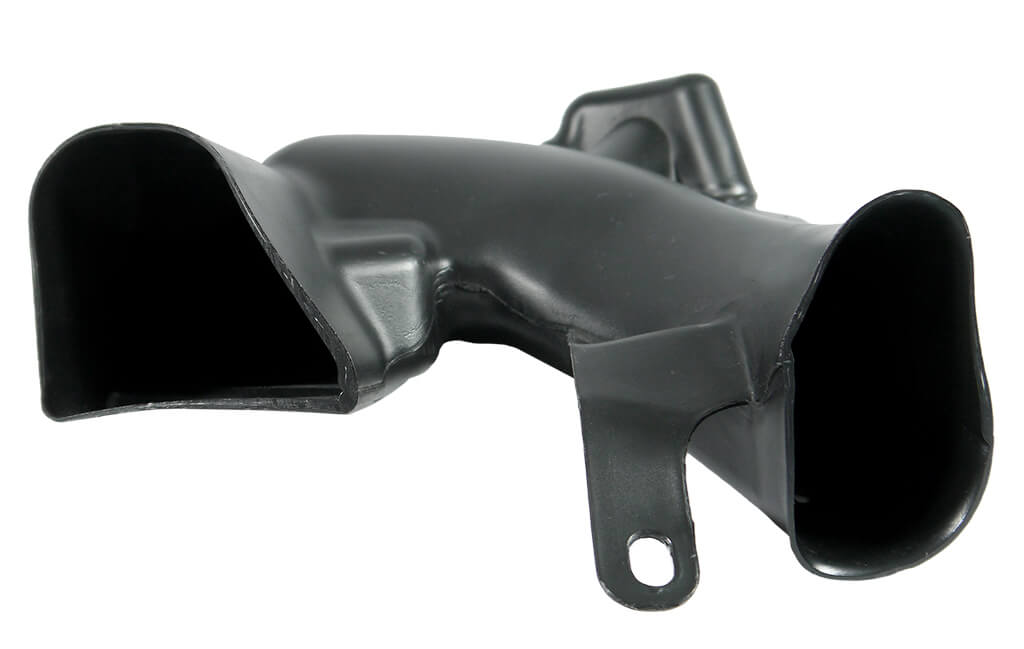
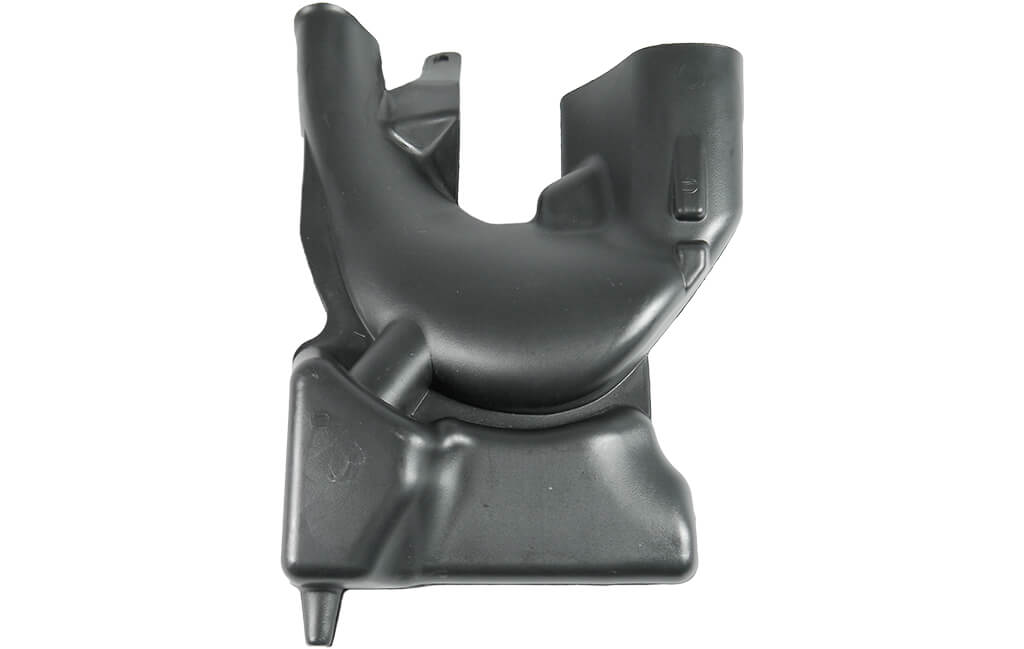
We have a proven track record in engineering and manufacturing a full range of blow-molded air intake components, including the following:
Clean Air Ducts & Assemblies
Resonators & Tuners
Dirty Air Ducts
Injection Molded Bellows, Cuffs, and Ports
By using our expertise and cutting-edge technology available to you, you can take your design to the next level.
From material selection to DFM/DFA, from prototyping to production, we’re here to help you succeed. So what are you waiting for? Give us call. Shoot us an email. Put us to work for you!
Optimizing Fluid Reservoir and Tank Design
Drawing from over three decades of experience and successful blow molded fluid reservoir programs, we can optimize your fluid reservoir and tank designs, providing cost-effective solutions without compromising on performance. We’ve have built efficiency and quality into every step of the engineering and manufacturing process.
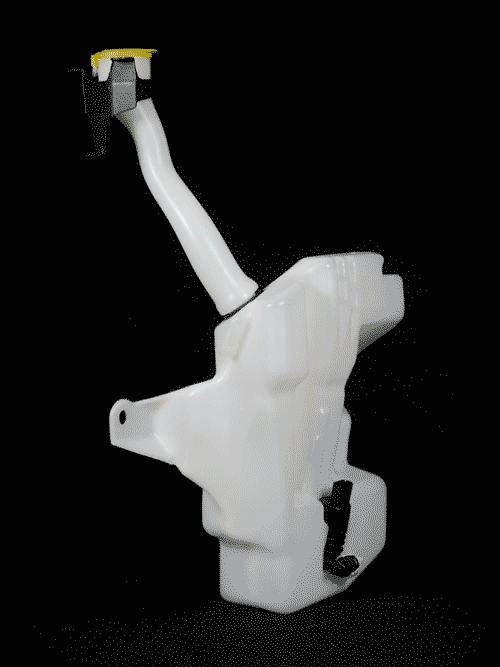

Our experience tells us that the best way to drive cost out is by optimizing part design so wall thickness can be minimized and secondary processes can be eliminated. This lowers the piece price by reducing weight, material costs, labor costs, and cycle times.
Here are the two most effective tactics we employ to achieve the optimal design:
1. Process Simulation
Using B-SIM, a cutting-edge blow molding simulation software, we identify potential issues and opportunities for improvement – during the design phase, well in advance of production. This helps minimize wall thickness while maintaining performance requirements and eliminates the need for prototyping and re-tooling.
2. Process Consolidation
Using insert molding, we can integrate molded ports, clips, and brackets into the part during the blow molding process, eliminating the need for secondary processes such as welding and manual assembly. Using core movements and side-actions, we can create features that would otherwise require machining such as drilling and cutting.
Partnering
for Success
If you are involved in or considering the development or production of any of the following, we should talk.
- Fluid Reservoir
- Windshield Washer Reservoir
- DEF Tank
- Radiator Surge Tank
- Coolant Surge Tank
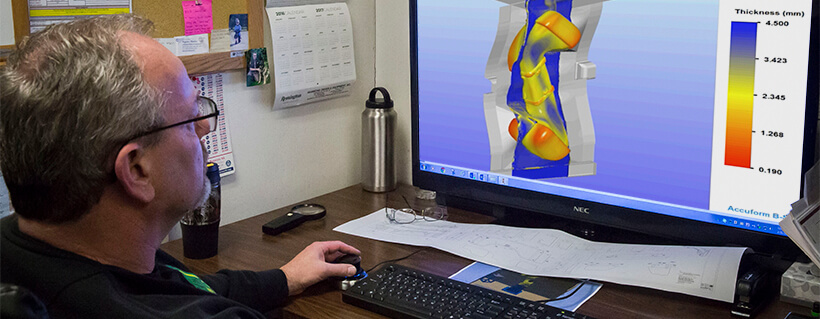
Our engineering expertise can optimize your part’s performance while reducing costs. By collaborating with us, you gain access to a team committed to excellence, efficiency, and high-quality results.
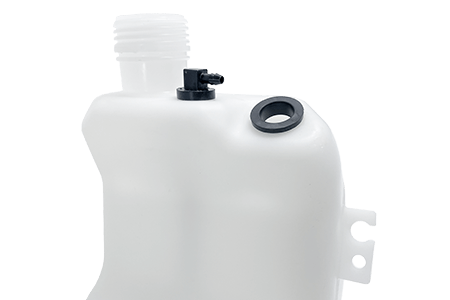
Unmatched Expertise in Fuel Tank and DEF Tank Manufacturing
Why choose us over other plastic tank manufacturers? It’s quite simple – we know what it takes to produce a successful fuel tank that won’t end in field-failure.
We perform blow molding simulation on every part design to ensure optimal wall thickness, produce rapid prototypes to test functionality and integration, process advanced materials that can withstand harsh environments, and test every single tank for leaks and rollover valve (ROV) functionality.
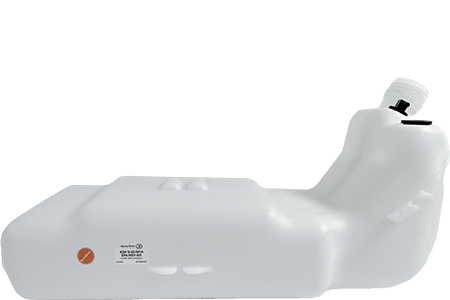
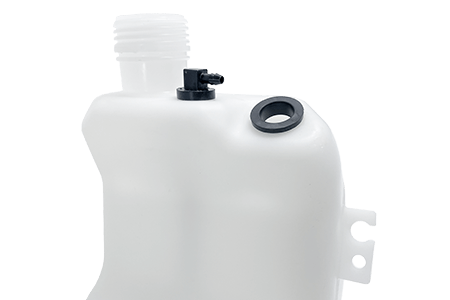
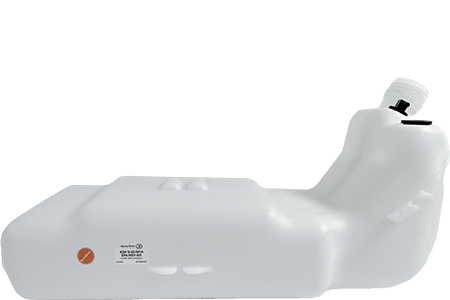
Reduce Field-Failure Liability
We perform strict rollover valve (ROV) and leak testing and apply serialized labels to each fuel tank with its unique test information, reducing our customers’ liability in the event of a field failure.
Reduce Development Costs
Through techniques such as blow molding simulation software and rapid prototyping with convertible tooling, we take the guesswork out of part design and reduce development costs.
Proficiency in Molding Durable Materials
We’re experts in molding highly durable and chemical-resistant materials that can withstand the corrosive nature of fuels while maintaining structural integrity.
Valve and Venting System Integration
We excel at seamlessly integrating valves and venting systems into our blow molded fuel tanks and DEF tanks, ensuring optimal performance, safety, and ease of use.
EPA and CARB Certified
We’re certified to produce fuel and DEF tanks that comply with stringent EPA and CARB environmental standards and emissions regulations.
In-House Secondary Operations
To further enhance functionality, we perform a variety of secondary operations in-house such as riveting, welding, and assembly, eliminating the need for third-party processing.
CO-EXTRUSION: EXPANDING POSSIBILITIES
In addition to profile extrusion, we specialize in co-extrusion, a process that involves simultaneously extruding multiple materials to create composite profiles.
The process starts by melting plastic pellets and pushing it through a die with the desired cross-section, or “profile”. The formed plastic then passes through a vacuum to help it maintain it’s shape, if necessary, is then pulled through a water bath until fully cooled. Now, the extrusion is ready to fabricate and either cut into multiple parts or wind as a single part.
A special technique called co-extrusion takes it to the next level by extruding two materials at once, often used to make parts that require both rigid and flexible components or two colors.
ONE OF MANY EXTRUDED SEAL APPLICATIONS: AUTOMOTIVE
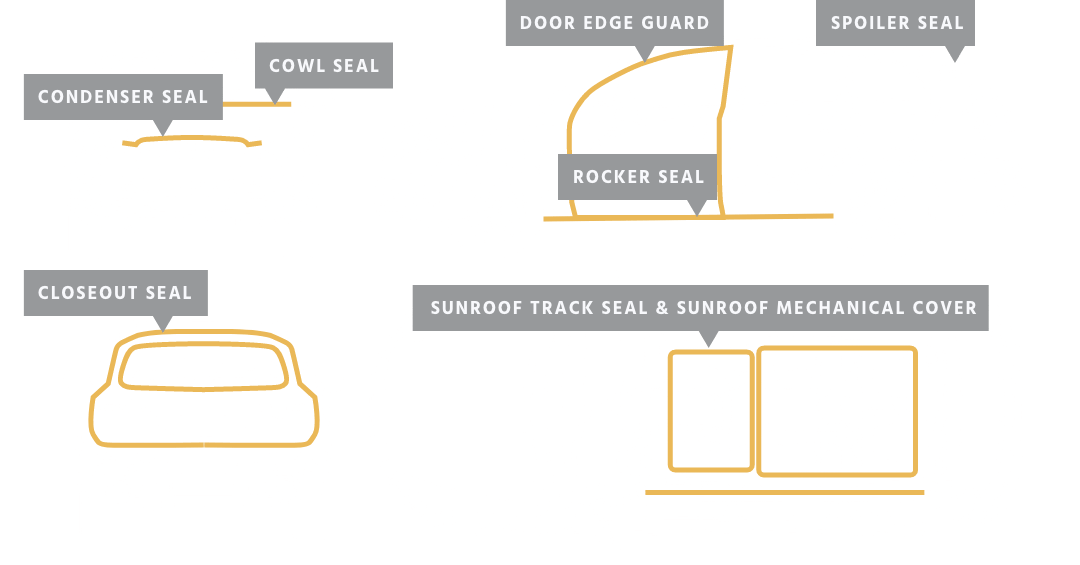
EXTRUDED SEAL SPECIALISTS YOU CAN RELY ON
Automotive and industrial customers across North America consistently rely on Gemini to help them choose the most cost-effective design and materials for their sealing applications. We have the experience and technology to help you, too.
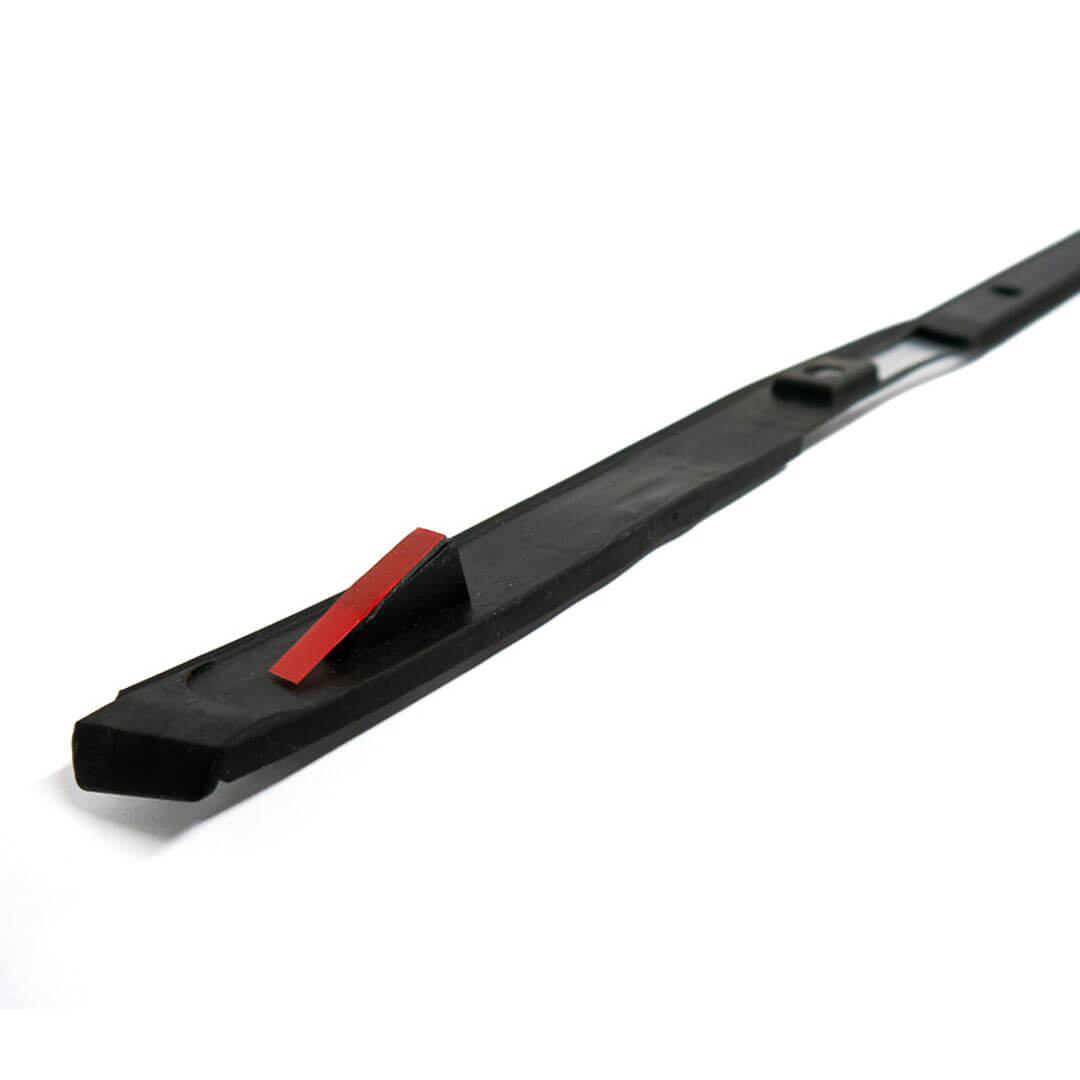
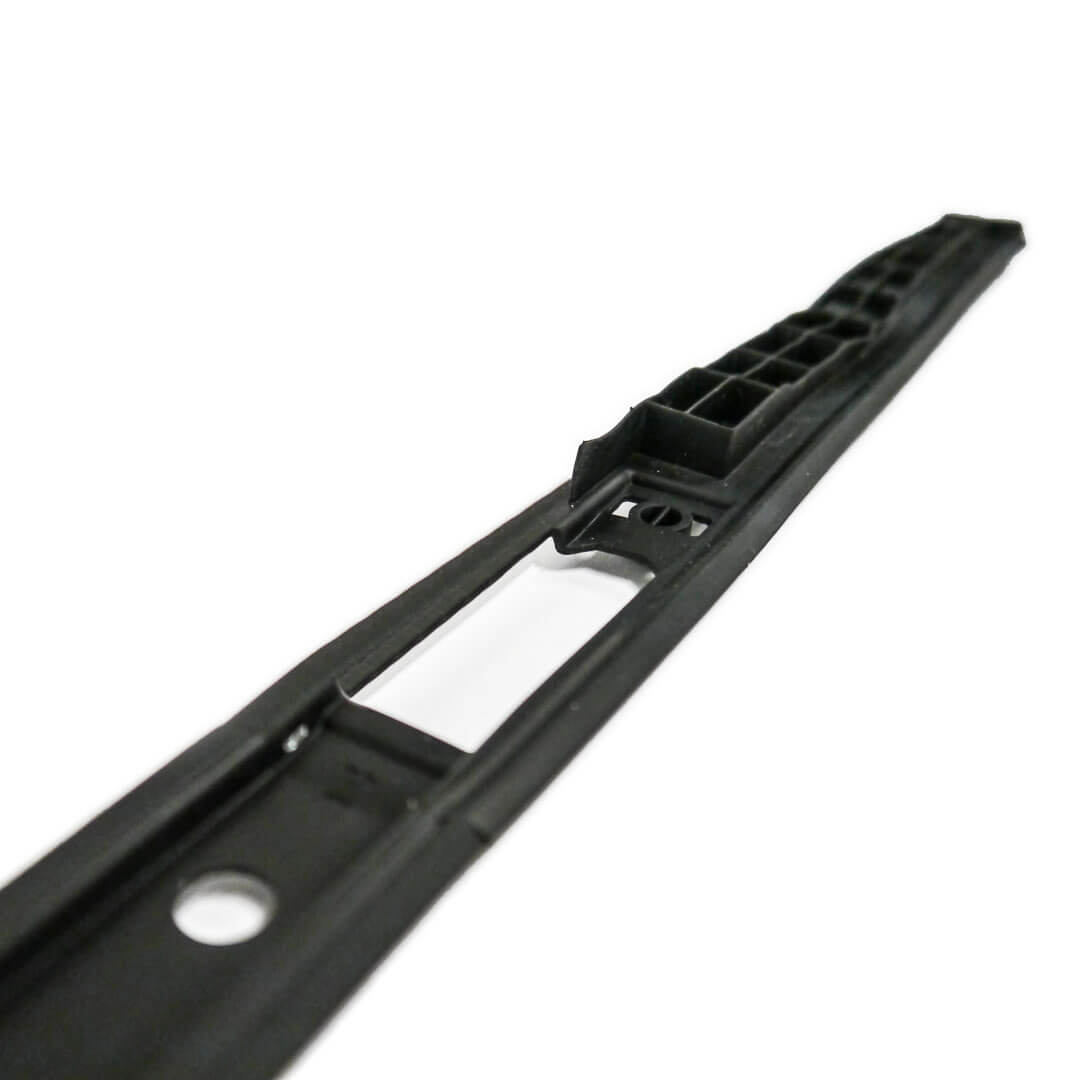
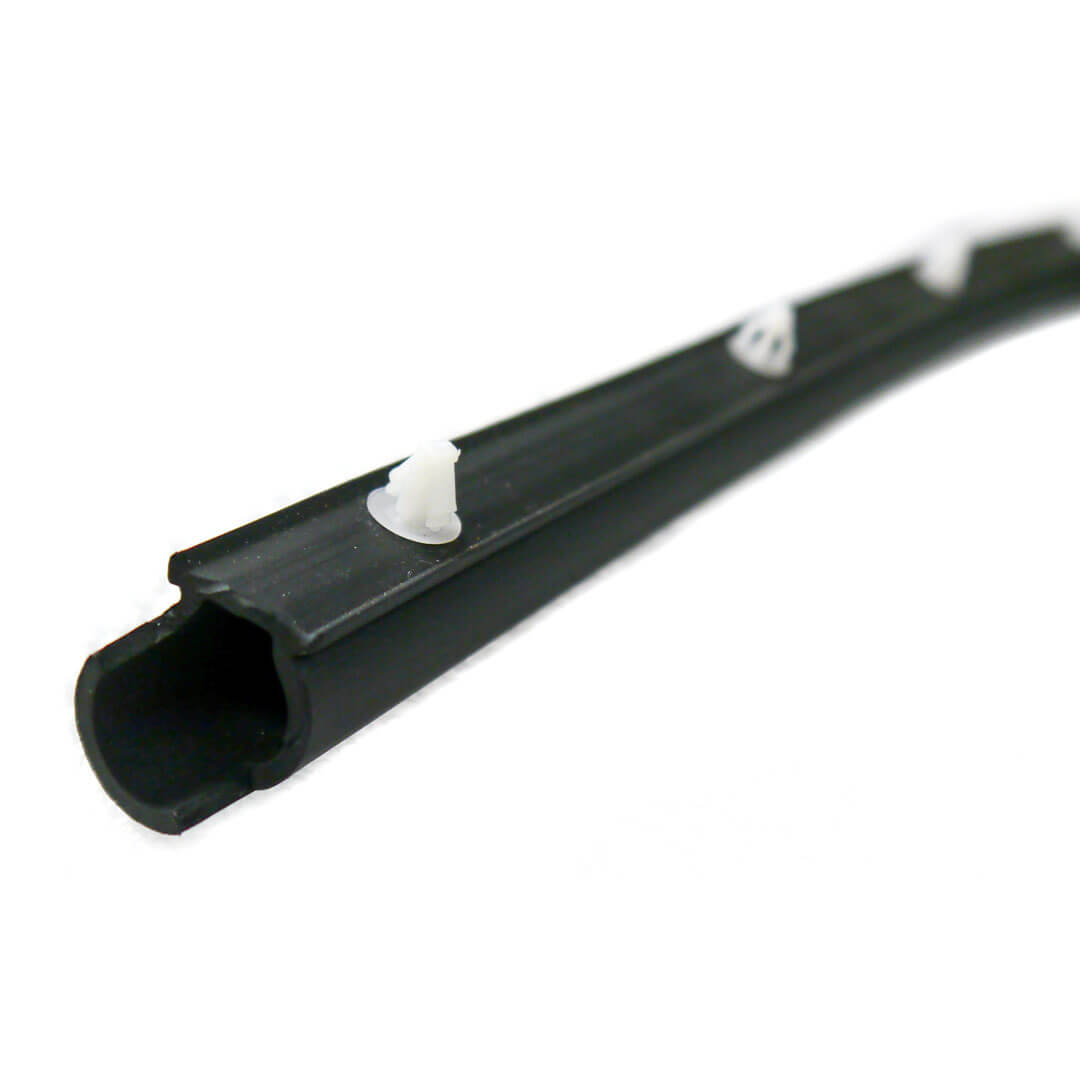
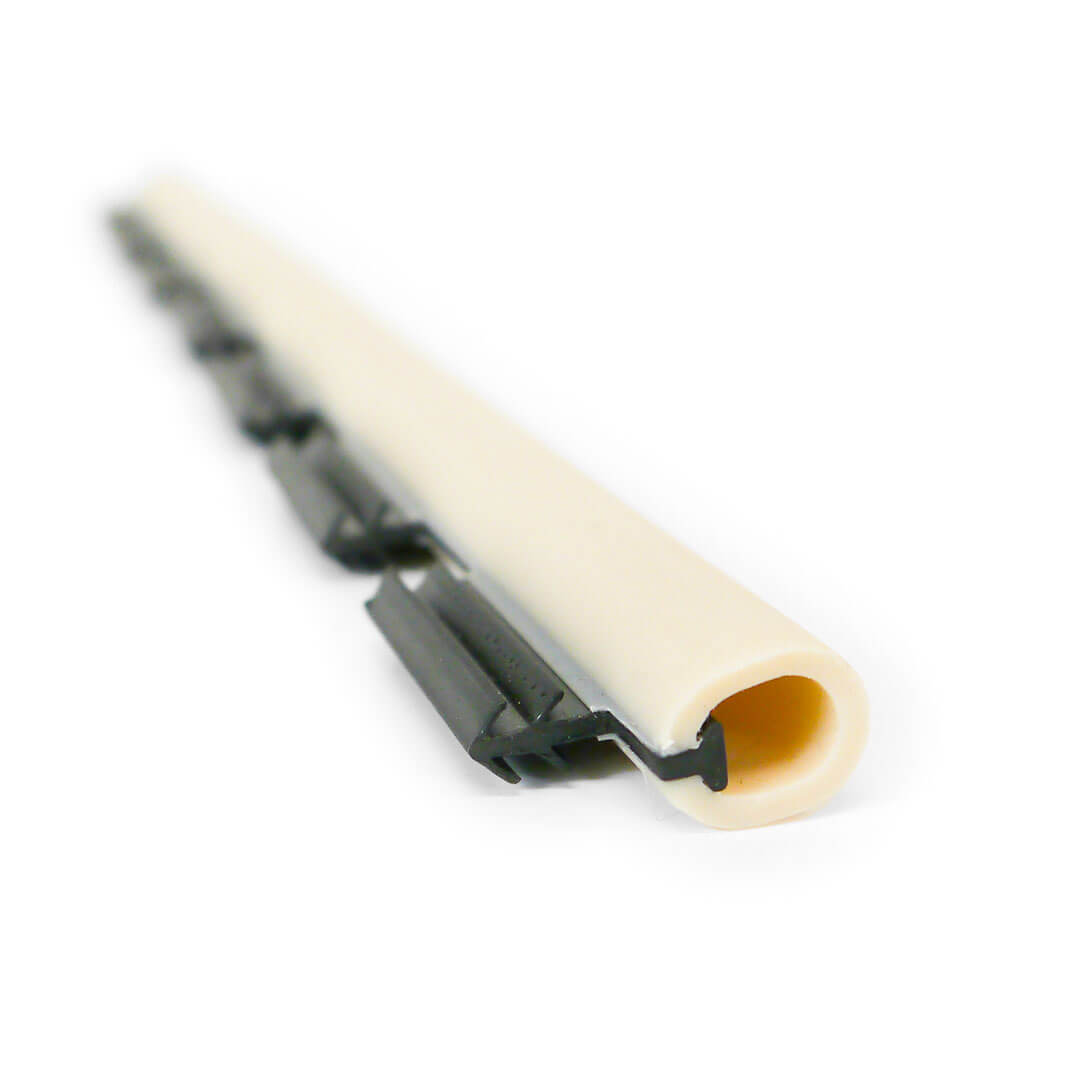
Engineering Support
We’re not just a manufacturer, we’re a partner in engineering. We take a DFMA approach to everything we do. This allows us to simplify, re-engineer, and drive cost out of your extruded seal, all while maintaining or improving its form, fit, and function.
Stringent Standards
With dozens of automotive OEM and Tier 1 customers across the globe, we’re more than capable of meeting and surpassing tough quality standards, delivery demands, and budget constraints for high-volume orders. You can rest easy knowing we’ll get the job done right.
In-House Tooling
If your seal design can’t be matched to one of our existing 7,000+ extrusion profiles, we’ll design and build the tooling in house. This includes prototype and production dies, trim and fabrication tools, fixtures and gauges, and anything else we need to meet the requirements of your custom extruded seal.
Co-Extrusion
Complex sealing challenges don’t require complex solutions. The co-extrusion process gives us the ability to extrude two or more materials at once on a single extrusion line. Need a soft-grip seal with a rigid base or carrier, and a nearly unbreakable molecular bond between the two? Easy. Co-Ex.
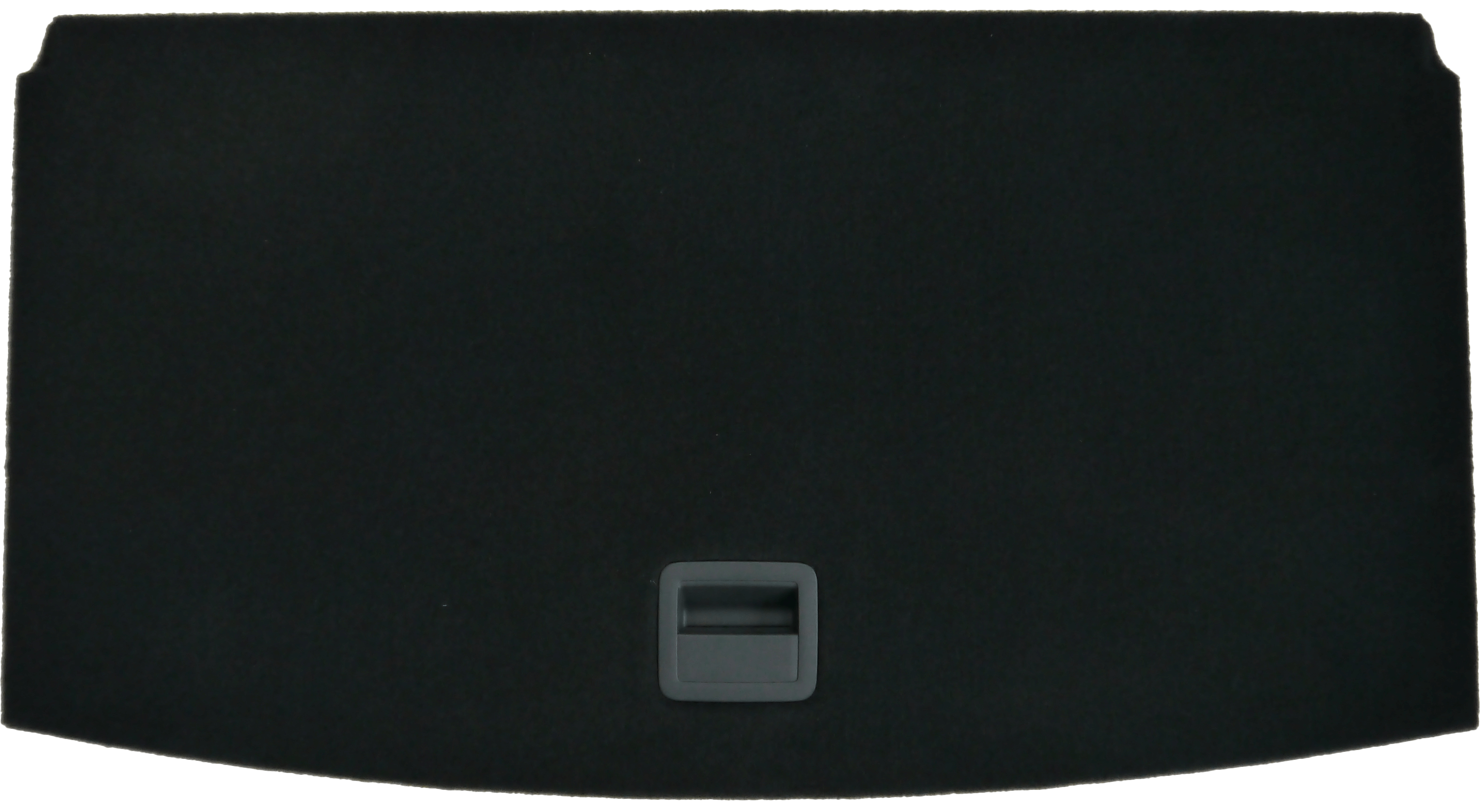
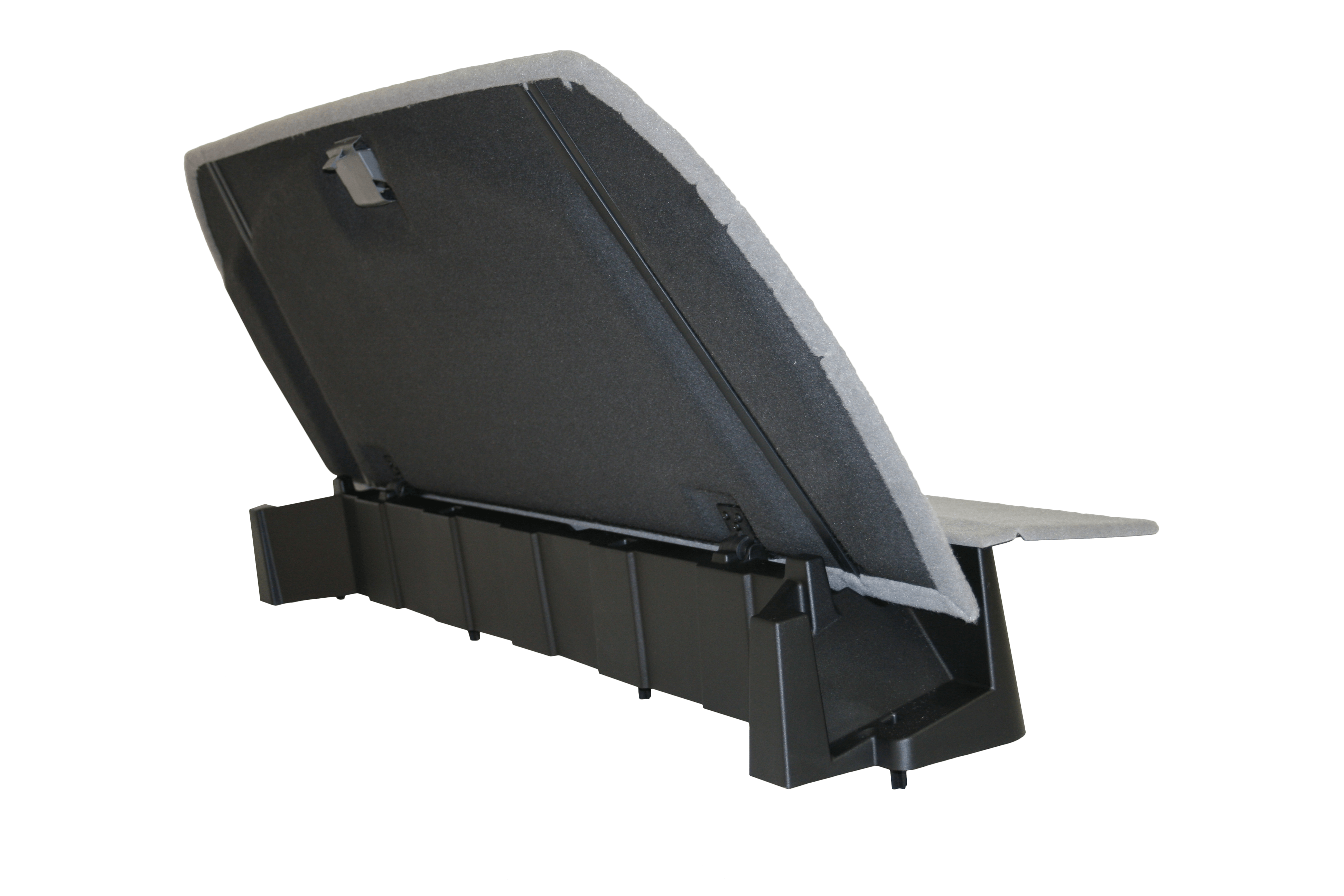
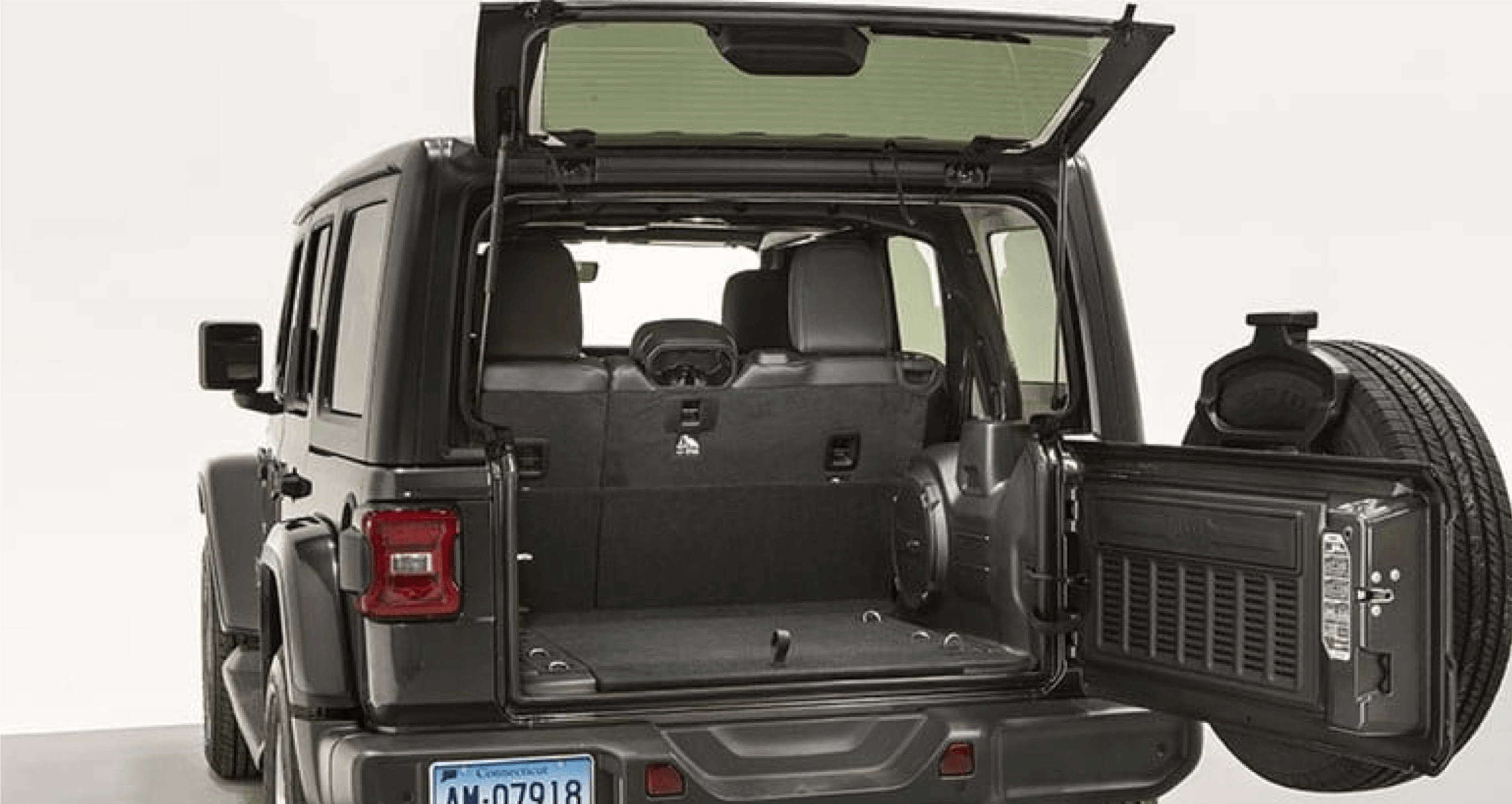
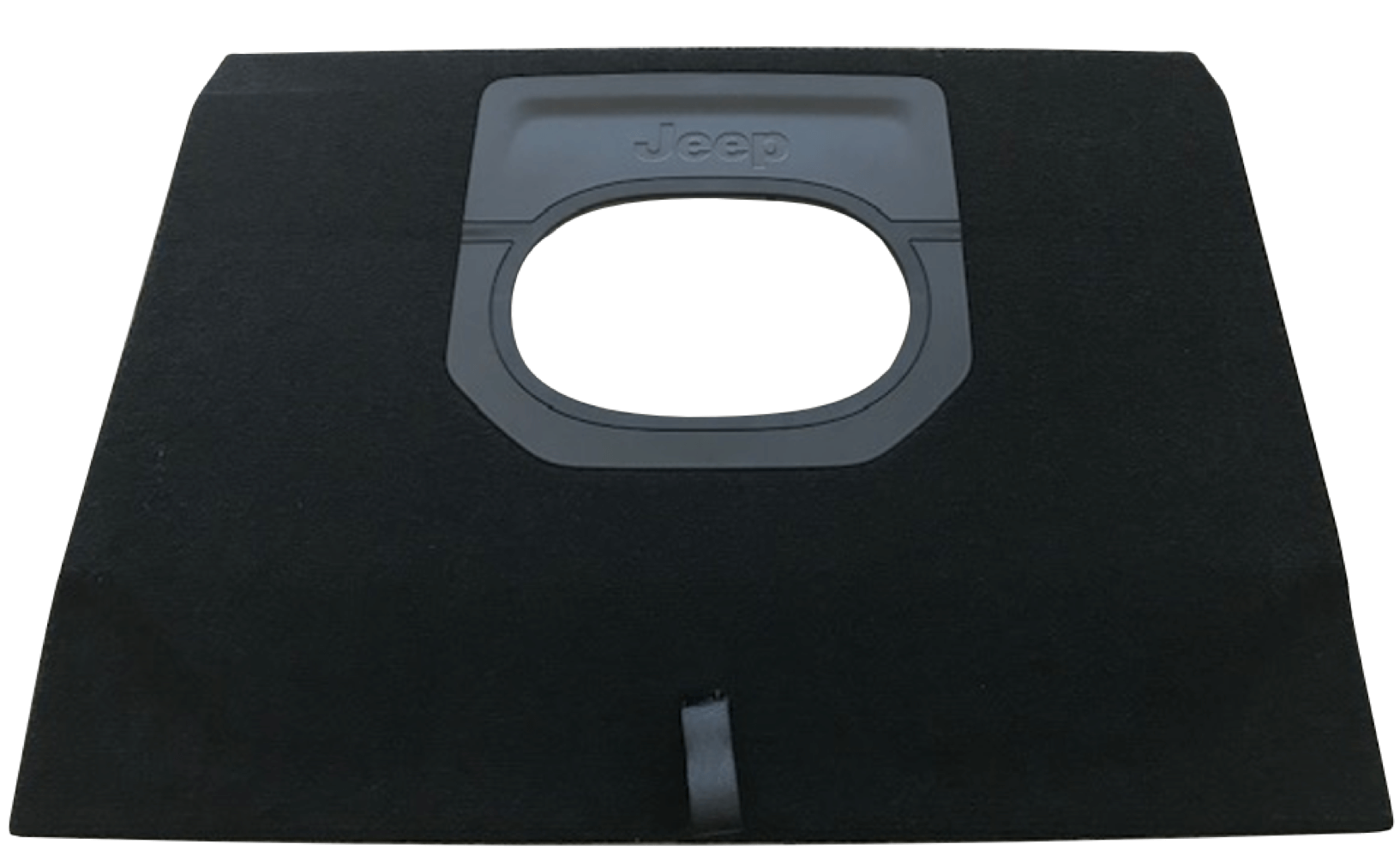
Experience the Future of Cargo Management
Partner with us to explore a new era of cargo management capabilities. Our utilization of cutting-edge technologies like FEA and in-house rapid prototyping guarantees designs that are both innovative and reliable. Develop solutions that blend intelligent design, integrated components, and luxurious finishes – all under our promise of excellence.
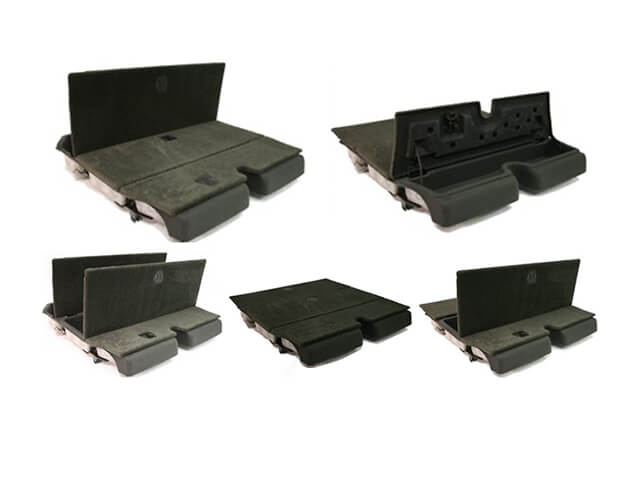
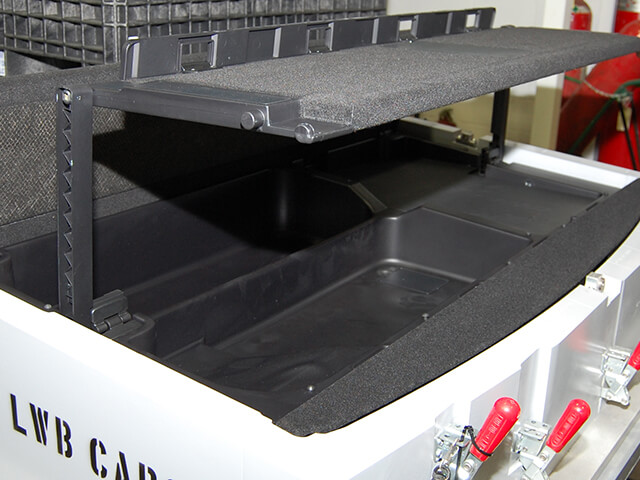
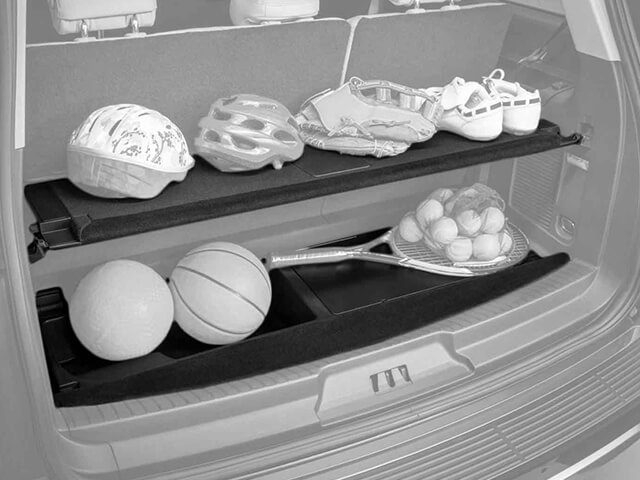
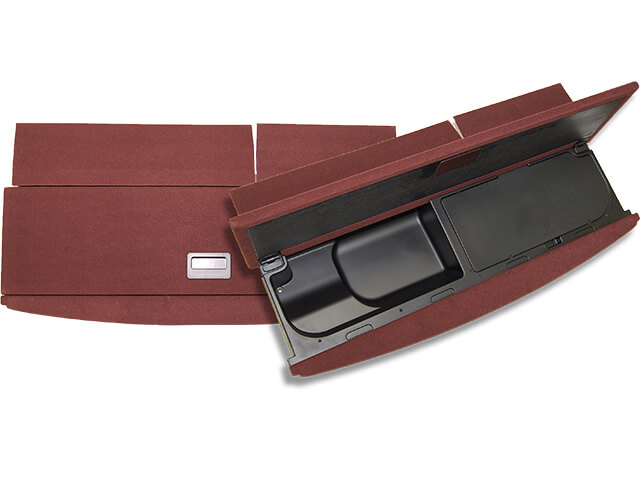
“Technical” Blow Molding
We often get asked how “technical” blow molding is different than your everyday, run-of-the-mill, blow molding. The main difference lies in the complexity and precision of the produced parts.
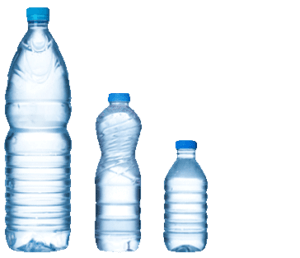
Standard Blow Molding
Standard blow molding refers to injection and stretch blow molding methods. It’s used for plastic products with standard material properties, basic geometries, and simple functionality such as water bottles and cosmetic containers. It’s pretty commonplace, generally less complex, and requires less precision.
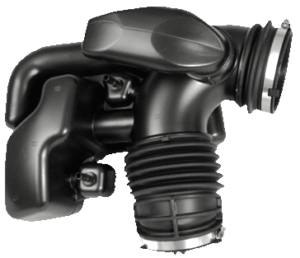
Technical Blow Molding
Technical blow molding refers to the extrusion blow molding process. It’s is used for producing highly engineered products with critical functional requirements such as fluid reservoirs and HVAC ducts. It involves the use of advanced machinery and sophisticated control systems that allow for complex geometries, higher tolerances, as well as the ability to incorporate inserts or achieve specific material properties.
Extrusion Blow Molding Process
The first step in the extrusion blow molding manufacturing process is the extrusion of a tube, also called a “parison”, of viscous plastic into a product mold. The mold closes around the parison and air is pumped in to inflate the parison against the mold walls. Once the plastic cools back to a solid state, the mold opens and the part is ejected. Finally, the excess material along the mold pinch line is removed by a process called deflashing and the part is ready to undergo any secondary operations that are needed to finish the part.
Step 1: Parison is extruded into the mold
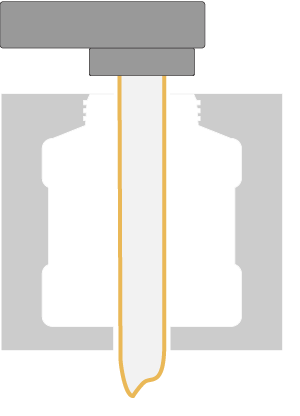
Step 2: Blow mold seals around parison
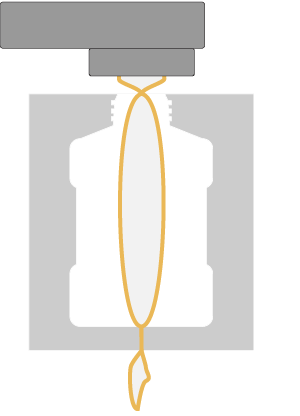
Step 3: parison is inflated with air
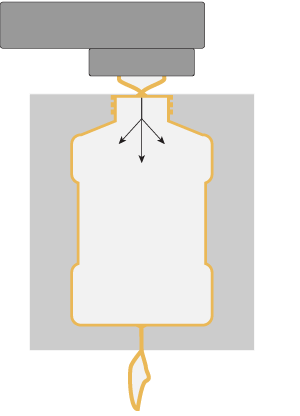
Step 4: parison cools and mold opens
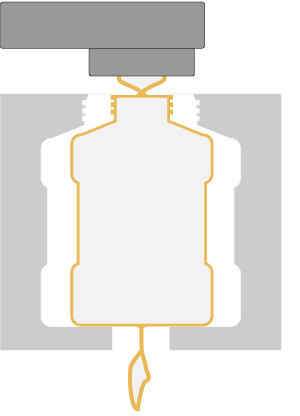
Compression molding and insert molding are often combined with the process of extrusion blow molding in order to maintain ID and OD tolerances and add features to the product:
PLASTIC COMPRESSION MOLDING
Typically, extrusion blow molding plastic is suited for tight control of the outer diameter (OD) of a part but does not allow for completely accurate tolerances of the interior diameter (ID). By combining the plastic compression molding process with the blow molding process, we can precisely control both the OD and ID of your part.
PLASTIC INSERT MOLDING
In the case of integrating plastic insert molding with the process of blow molding plastic, we can incorporate fasteners and/or other inserts directly within the mold. This eliminates steps in the production process such as riveting or welding which add time without adding value, and creates a stronger bond between the blow-molded and insert-molded components.
IN-PROCESS TESTING METHODS
To make sure that your blow molded part meets all of your specifications such as material properties, tensile strength, load, thickness, and more, we perform thorough testing both on the production floor and in our dedicated testing lab. We tailor our testing procedures to match the design and requirements of your specific part.
We employ the following techniques to guarantee the quality of your parts:
- Rollover Valve (ROV) Testing
- Mass Flow Testing
- Submersion Testing
- Other Leak Testing Methods
- Push/Pull Testing
- Tensile Testing
- Material Thickness Analysis
- Destruction Testing
- Color/Gloss Testing with Spectrometers
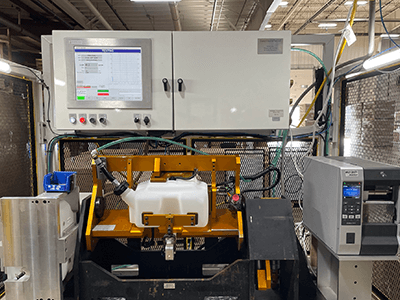
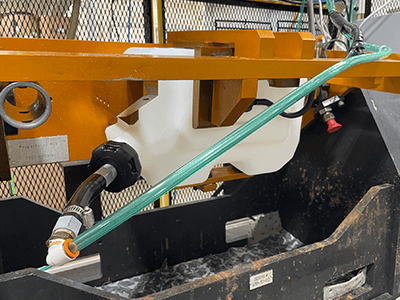
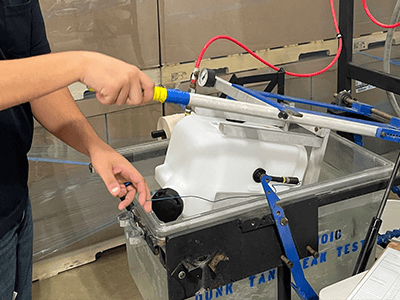
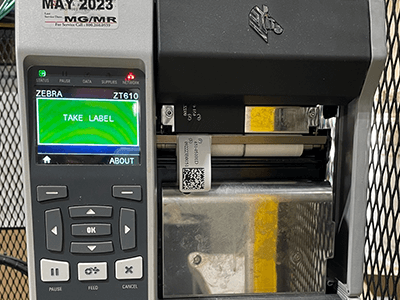
With our comprehensive in-process testing methods, we ensure that every aspect of your blow molded product is thoroughly evaluated and meets the highest quality standards. By minimizing the chances of field-failure through rigorous testing, we enhance the reliability and performance of your parts. Trust our expertise and dedication to exceed your expectations.
Two-Shot Molding Process
There are two phases of the two-shot molding process.
The first is similar to traditional injection molding: A shot of resin is injected into a mold and cooled to form a solid part.
In the second phase, the just-molded part is transferred to a second mold via a rotating platen or a robotic arm, and receives the second shot of resin – in, through or around certain parts of the first molded part, depending on the design. The two plastic resins then form a molecular bond and the multi-resin molded part is cooled and ejected.
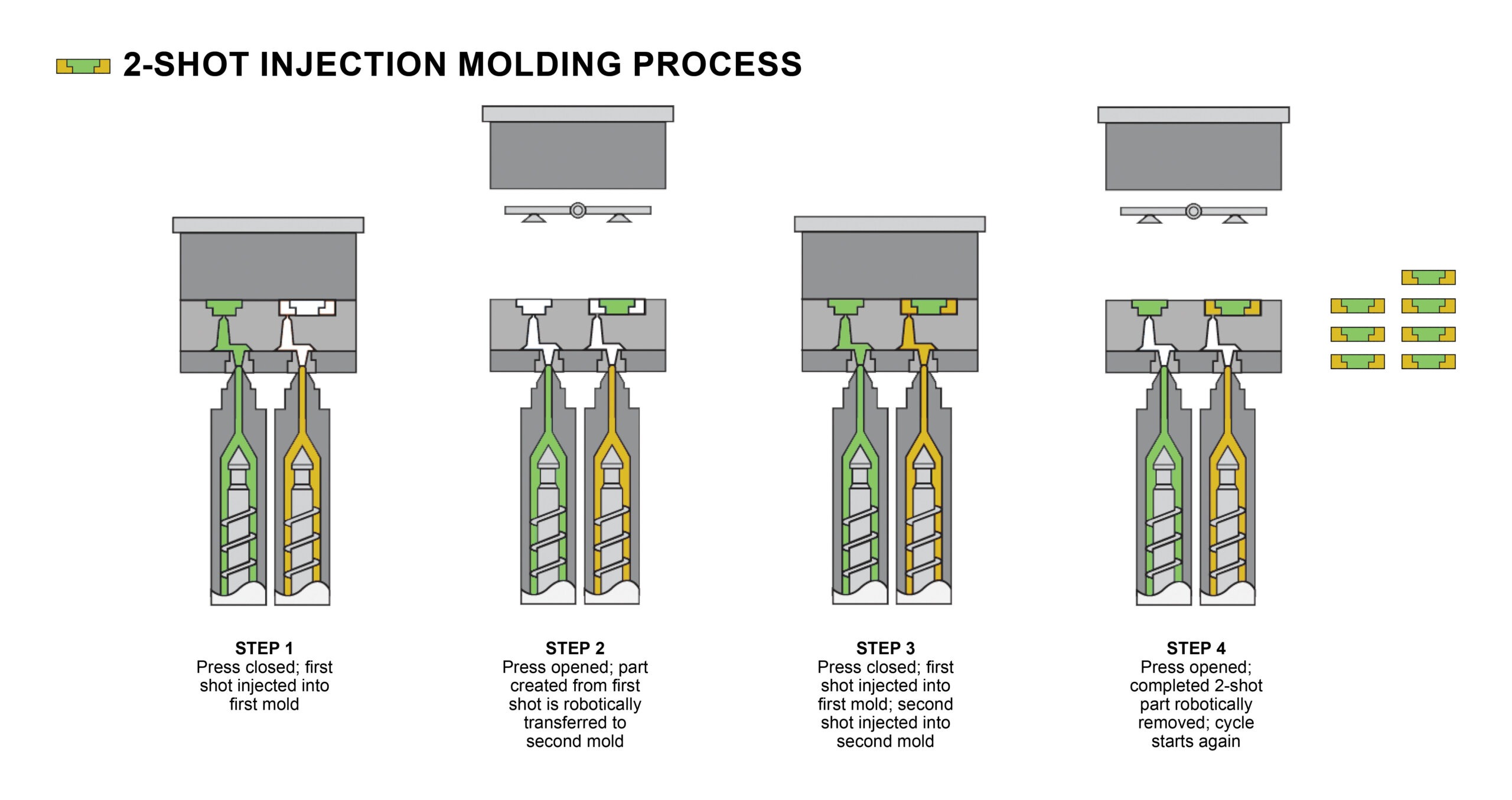
The process isn’t difficult to understand, but it’s highly difficult to master. It requires high levels of technical expertise and attention to detail, and even the smallest mistakes can cost big money, especially in high-volume production scenarios.
That’s why it’s critical to find a highly capable supplier. Look for excellent supplier quality scorecards, defined processes to mitigate against flash, flow lines, and short-shots, and contingency plans to expand capacity as your business and your two-shot molding needs grow.
Once you find a supplier, involve them early on in the design phase of your part. They can identify potential problem areas and engineer value into your product.
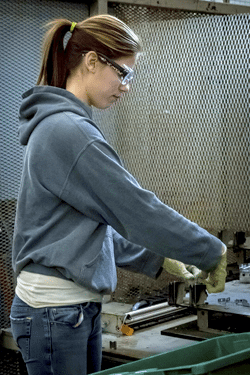
- Insert/Over Molding
- Heat Staking
- Riveting
- Sub-Assembl
- Hot Stamping
- Foam and Acoustic Pad Assembly
- Part Identification Marking
- Parts Kitting
LARGE FORMAT EQUIPMENT
(3) Toshiba and Union Large Format Boring Mills
(1) Dual Column Bridge Mill
(1) Millutensil Spotting Press
Up to 158” x 118” x 180″ table size
50 Ton Capacity
Our large format milling machines and spotting press allow us to produce massive bolsters, cassettes, and other large format tooling.
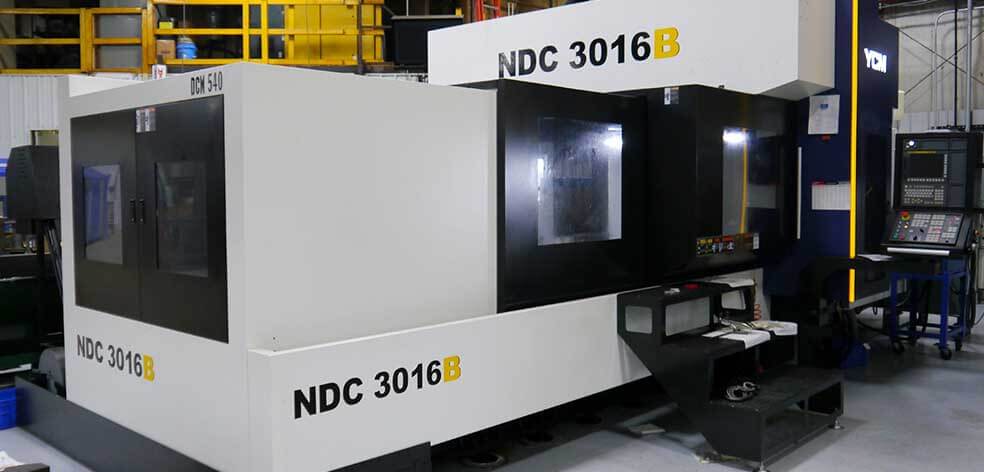
PRECISION CNC TURNING
(40) Okuma and Mazak CNC Lathes
Up to 6-jaw chucking capabilities
Live milling capabilities
Off-center radial and face cut features
Up to 24” diameter, 60” long
These lathes are making chips on all shifts with full part inspection, minimizing programming time and maximizing production efficiency.
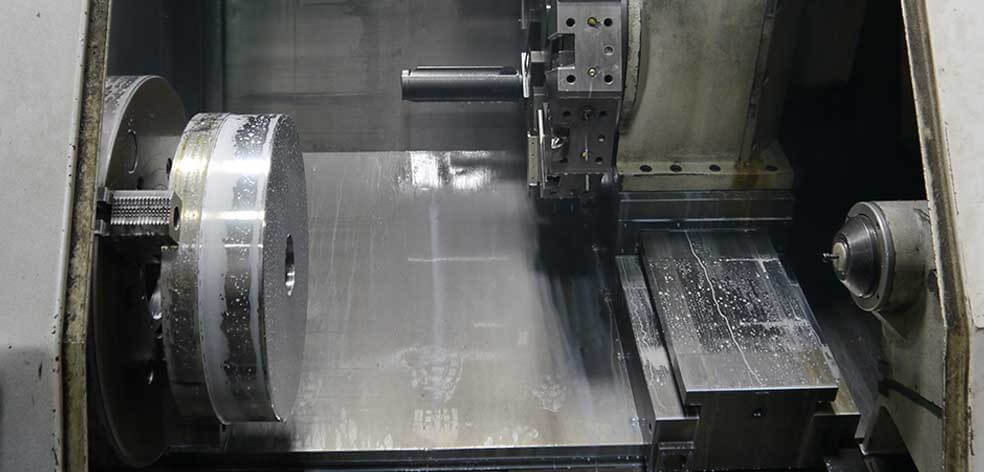
PRECISION CNC MILLING
(43) Okuma, Makino, and Mazak CNC Milling Machines
5-Axis and high-speed milling capability
Up to 55” x 47” x 55” horizontal table size
Up to 24” x 55” x 78” vertical table size
We combine deep machining know-how and unique work-holding fixtures to run our highly efficient and precise milling operation.
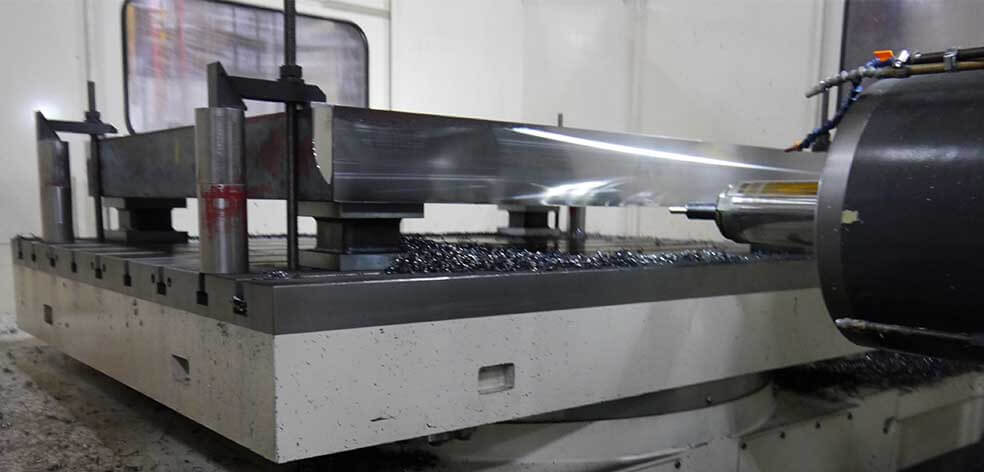
GRINDING AND HONING
(10) Okuma ID/OD Grinding and Sunnen Honing Machines
16” diameter, up to 40” long
(5) Okamoto Surface Grinders
20” x 40” table size
Our grind department is temperature and humidity controlled, allowing us to hold the tight tolerances your toughest project requires.
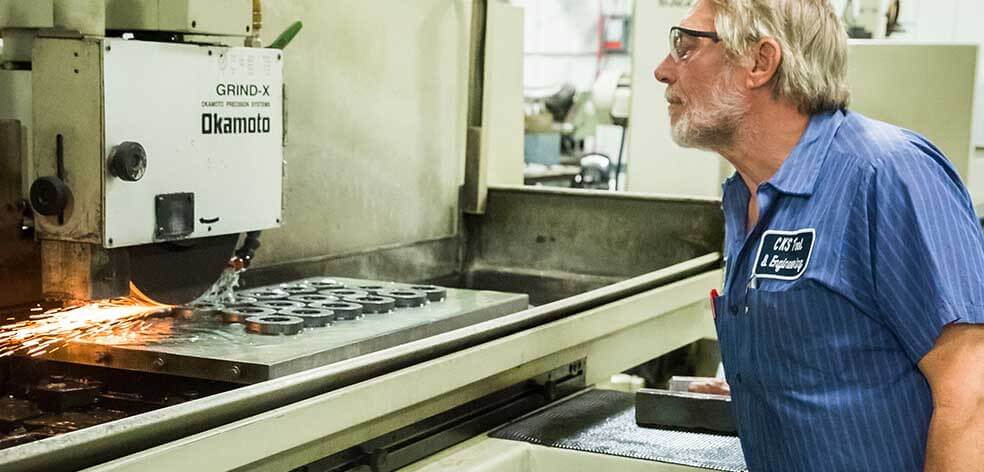
HEAT TREAT / BLACK OXIDE / CRYOGENICS
2,000 lb Carburizing Furnace
2 Bar Vacuum Furnace
Black Oxide Coating
Salt Pot
Fluidize Bed
Cryogenics
Compare our cryogenically treated and coated tools head-to-head against your existing tooling to see how much additional tool life you can achieve!
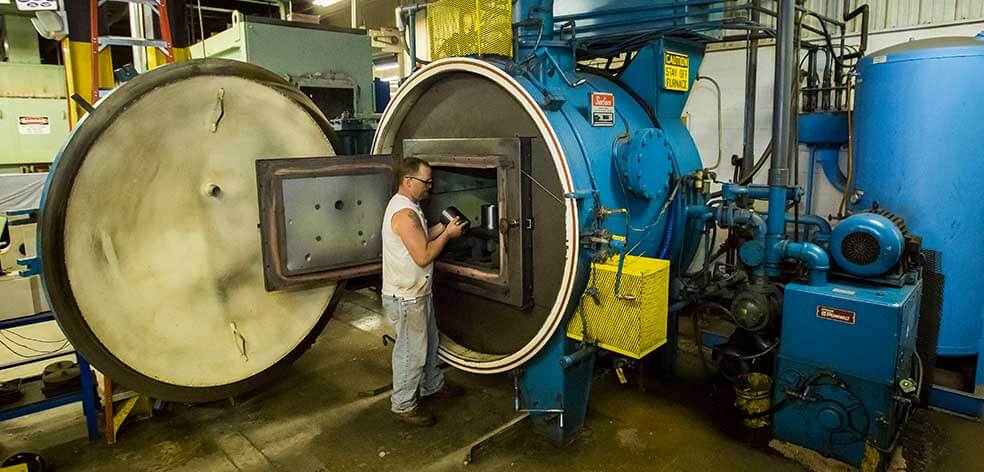
Our comprehensive treatment and coating capabilities allow close monitoring of operations that are often outsourced by other suppliers, saving you time and cost versus maintaining a separate vendor.
WIRE AND SINKER EDM
(5) Fanuc Wire EDM Machines
20” x 30” table size
(1) EDM Hole Burner
(2) Makino CNC Sinker EDM
98” x 55” x 32” table size
Our climate-controlled wire EDM department allows for small or odd-shaped angles and intricate contours.
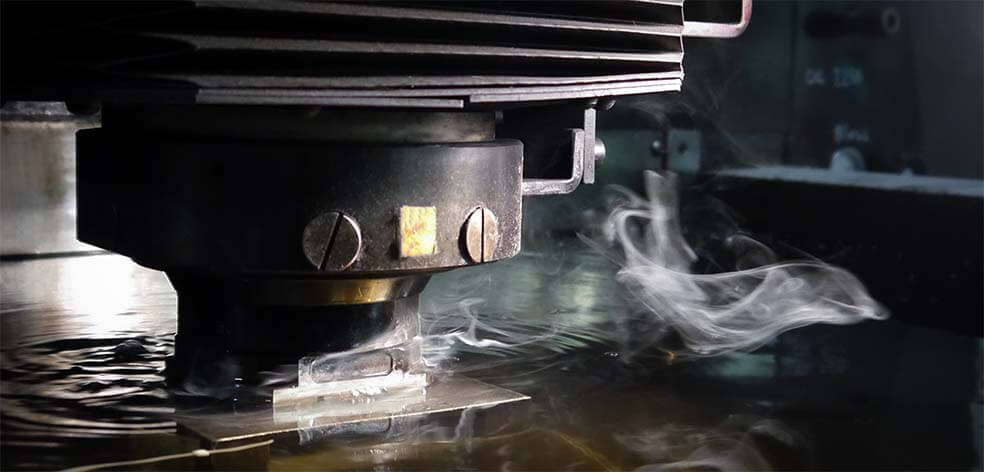
Our EDM capabilities are especially valuable for cutting pre-hardened steel, as it eliminates the need for heat treatment to soften and re-harden the material. EDM can also be used on exotic metals such as titanium, hastelloy, kovar, and inconel.
QUALITY & ENGINEERING
Inspection
Part Marking
CAD/CAM
DEFORM Simulation
Our quality and engineering staff are armed with state-of-the-art equipment and receive ongoing training on critical inspection processes and capabilities.
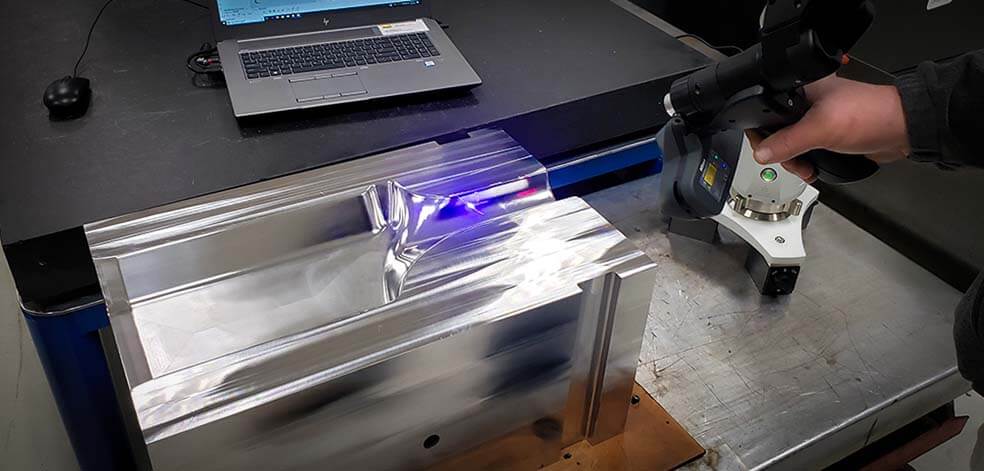
Our facilities are armed with a full complement of quality and engineering equipment.
Inspection
Our inspection equipment includes two 3D laser scanners by Nikon and four CMMs by Zeiss, Wenzel, and Brown & Sharp, and is located in dedicated climate-controlled labs with some units strategically located so operators can conduct critical in-process inspections.
Part Marking
We employ laser etching, pin marking, and other techniques to customize your part with permanent text, graphics, barcodes, or logos.
CAD/CAM
Our CAD/CAM department is equipped with the latest technology from Mastercam, Work NC, Solidworks, ProE, Delcam, and NXUnigraphics.
Simulation
We perform full forge tooling design and simulation with DEFORM engineering software, enabling us to predict material flow, thermal behavior, and deformation with precision.
LOGISTICS
We maintain local logistics warehousing to accommodate incoming raw stock, as well as finished goods ready to ship.
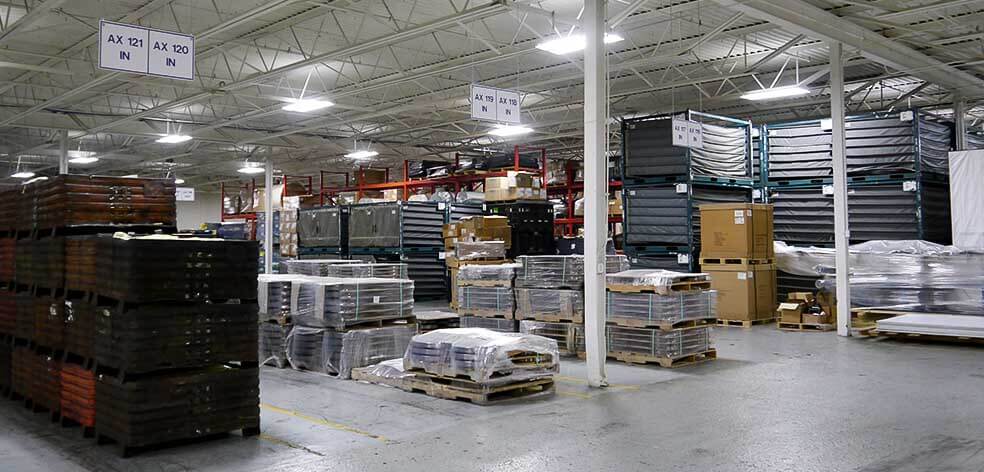