Hero 1 Engineered Plastics & Tooling Solutions
Our design and manufacturing expertise delivers innovative engineered plastic products for the most demanding applications. As a trusted industry leader, we provide customers with the highest level of quality and functionality.
Hero 2 Secondary Pages
Nearly every major automotive OEM partners with us to design and manufacture their cargo management systems, load floors, and other interior trim components. Our early access to trends and customer preferences enables us to provide innovative solutions to meet the evolving needs of the market.
Hero 3 Tertiary and Quaternary
We specialize in custom processes for automotive interior trim components, including cargo management, load floors, and seatbacks. Our team crafts unique solutions to boost quality, cut costs, and speed up your time-to-market.
BY THE NUMBERS
Insights
CERTIFICATIONS
Wherever You’re Located, We’re Here to Help
18 strategic locations in North America to meet the needs of our diverse customer base.
Get to know us. Get in touch today.
Gemini Group has the resources to meet any part or production challenge. Let’s talk about what that means for you.
"*" indicates required fields
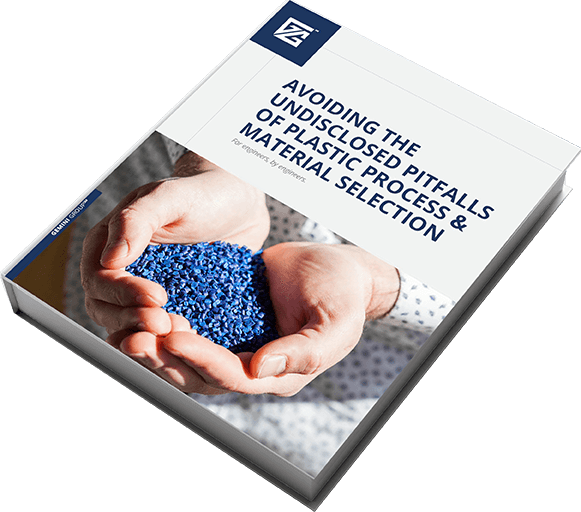
An Insider’s Guide to Plastic Process & Material Selection
It’s easy to under-design or over-engineer a plastic part. Whether you’re designing from scratch or converting from metal to plastic, there are a number of constraints you need to consider for each process and material option. Our engineers created this guide to help.
1 min
Two-Shot Injection Molding
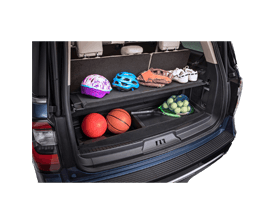
APPLICATIONS
We partner with OEMs and suppliers across the globe to develop innovative solutions for automotive interior trim applications and can quickly pivot to changing requirements. From cargo management systems to load floors to seatbacks, we can deliver.
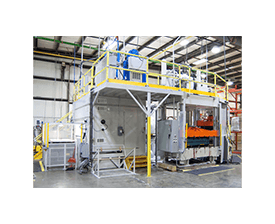
MANUFACTURING CAPABILITIES
With a variety of production processes available, we excel at driving cost out of your product and decreasing time to market. Our expert team thoroughly examines each project and recommends the process that will produce the best outcome.
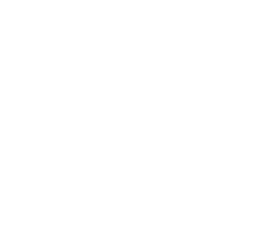
DESIGN & ENGINEERING
With decades of design and engineering experience, our team works alongside yours to identify ways to improve product performance and cost. We’re experts in value-added engineering and manufacturing and offer full design responsibility.
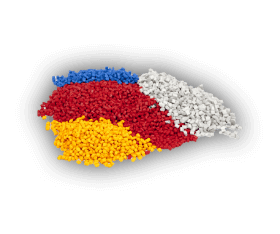
MATERIALS
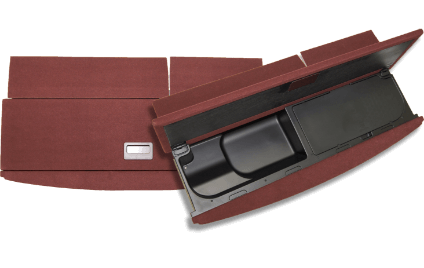
CARGO MANAGEMENT
Our expertise in designing and manufacturing cargo management systems begins with a deep understanding of consumer preferences and market trends.
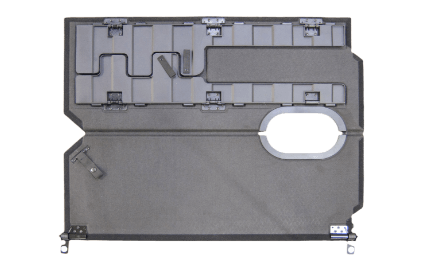
Automotive Load Floors
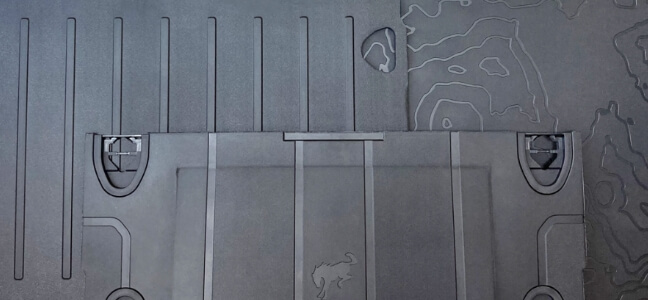
U-SKIN
Our innovative surface technology provides customizable, tough, and functional applications for automotive applications.
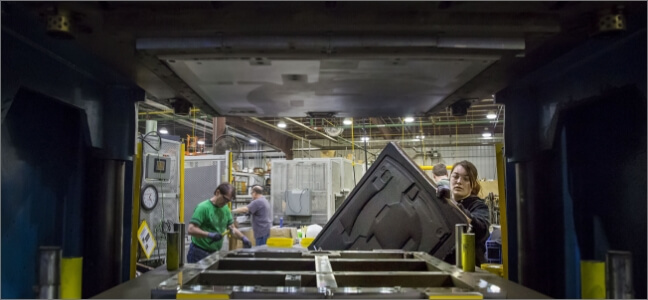
Composite Spray Molding (Baypreg)
Our advanced composite spray molding technology ensures exceptional load floors with superior strength and durability.
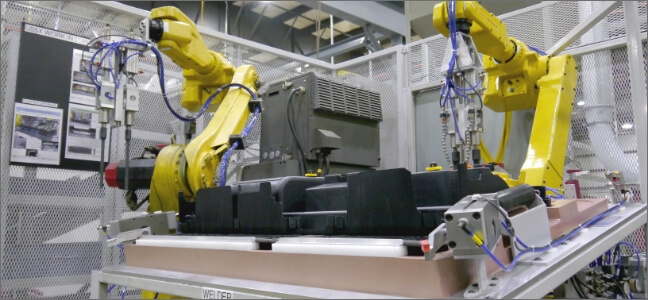
Compression Molding
Our mastery of compression molding opens doors to shaping high-strength substrates, such as, natural fiber, fiberglass composites, and carpet.
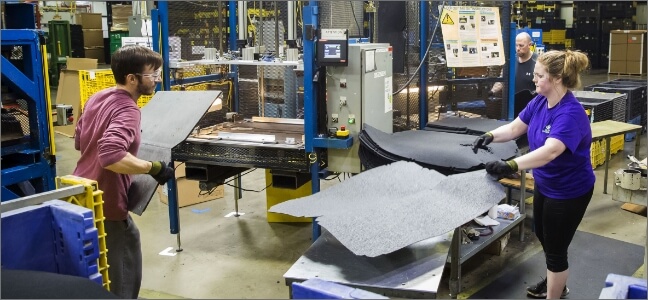
Other manufacturing methods
Our expertise in injection molding, twin sheet molding, and plastic thermoforming enable us to provide you with the best process choice available.
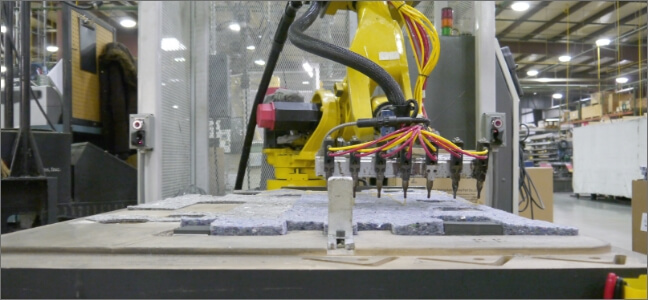
Secondary Operations
Our proficiency extends far beyond these processes. From robotic edge wrapping to sonic welding, each process showcases our dedication to achieving excellence from every angle.
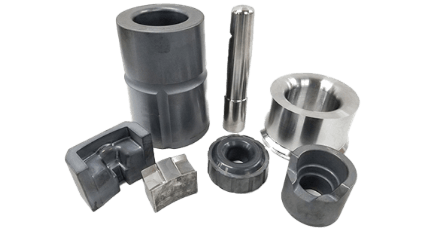
forge tooling Products
We are a preferred partner for the design and development of world-class hot, warm, and cold forge tooling systems, proudly made in the USA. Over forgers rely on us for full tooling systems crafted for optimal performance in forging hammers, presses, upsetters, ring rolling, trimming, sizing, and automation.
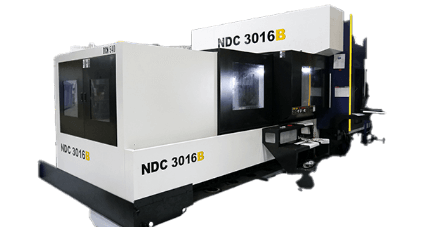
Equipment & Capabilities
We’re armed with over 100 CNC machine tools, including six high-speed mills and three 5-axis mills, and a dedicated staff of over 100 machinists, programmers, and engineers. From large format equipment to our exclusive in-house heat treat and black oxide, we’re equipped to meet the highest standards of quality, durability, and delivery.
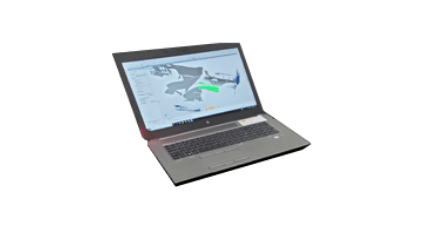
DESIGN & ENGINEERING
Our forge tooling specialists are true masters in their craft, routinely recommending material, design, and process modifications that extend tool and die life, enhance performance, and improve operational efficiency. With a combined 168 years of experience, you can count on our design and engineering team to deliver innovative solutions for your toughest forging challenges.
Are you sourcing a custom HVAC duct or simply looking to update your benchmark?
If you need to achieve complex geometries or you spend north of $100,000 annually in blow molding, we should talk. Contact us today for an accurate and timely quote.
case study
PATENTED SURFACE TECHNOLOGY SAVES 6 LBS AND $10 PER VEHICLE
When a major OEM was designing an iconic vehicle that gave consumers the freedom to experience the outdoors, they needed a cargo surface that was tough, lightweight and waterproof. The answer was U-SKIN™. We provided a load floor system that enabled the OEM to eliminate the need for a mat which would cover the already trimmed out carpeted load floor. The project eliminated 6lbs of mass in every vehicle fitted with this surface technology. In addition to the weight savings the OEM benefited from a reduction in part numbers and about a $10/vehicle savings.
If you have an annual production volume of 3,000 parts or more, we should talk.
If you have an annual production volume of 3,000 parts or more, we should talk. Whether you’re sourcing a new fuel or DEF tank supplier or simply updating your benchmark, you deserve an accurate and timely quote. We will deliver.
Content with Video
With more than 7,000 plastic extrusion profiles developed, we have the experience to achieve the right profile for your application.
Our designers and engineers are specialists in creating complex extrusion designs; we work with virtually all materials and offer advanced profile features such as hollows, living hinges, and dual and multi-durometer composites.
You save time and money because we design and build all tooling and perform all secondary operations in-house.
Frequently Asked Questions
General FAQs
Who do you work with?
We typically work with large customers such as OEMs and Tier 1 suppliers. The majority of our accounts require at least 10,000 parts annually and have an annual buy north of $100,000. If this sounds like you, we should connect. You can drop us a note online, give us a call at (248) 435-7271, or email us at plasticsales@geminigroup.net.
How do I contact you? Where are you located?
Our Profile Extrusion Division consists of three business units: GPI, Sierra Plastics, and GPM. GPI is located in Ubly, Michigan; Sierra Plastics in El Paso, Texas; and GPM in Saltillo, Mexico. Please visit our Locations page for location details and contact information.
What are your capabilities?
65 extrusion & co-extrusion lines
- Hollow profiles, living hinges
- Dual and multi-durometer
- Two or more colors
Secondary operations
- Insert and overmolding (corners and sections)
- Thermal bending
- Welding (ultrasonic, hot plate)
- Lamination
- Assembly
- CNC routering
In-line processing and fabrication
- Wire and metal carrier reinforcement
- Tape (PSA, foam-backed)
- Slipcoat application, including silicone
- Flock application
- Graining
- Inkjet printing
Advanced testing laboratory
- Tensile/elongation testing
- Flowability
- Hardness (rockwell)
- Cold impact
- Component-level validation
- CMM
- Dimensionals
In-house tooling design and build
- Extrusion and co-extrusion dies
- Trim/fabrication tooling
- Assembly fixtures
- Quality gauges
Rapid prototyping
- FEA
- Process simulation
- 3D printing
- Dedicated prototyping lines
What certifications do you have?
Our extrusion business units include GPI, Sierra Plastics, and GPM. GPI and Sierra Plastics are ISO 14001:2004, ISO/TS 16949:2009, and WBENC certified. GPM is ISO/TS 16949:2009. You can view the certifications here.
What materials do you work with?
We work with a variety of multi-durometer plastic-rubber blends, including:
- TPV
- TPR
- T TPO
- TPE
- TPU
- 50+ engineered resins!
How do I design an extrusion profile?
We’d be remiss to provide an answer without understanding the scope of your challenge. That’s why we’ve developed an Extrusion Design Guide. It provides the basic facts you’ll need to start the plastic extrusion design process
How much does extruded plastic cost?
Every extrusion solution is unique and deserves a custom quote. Though many of our jobs are custom, we can help you determine if an existing profile will work for your project. Request a Quote to learn more.
My project requires an NDA. How do I submit that?
You can attach your NDA to our RFQ form or send it directly to plasticsales@geminigroup.net.
Seal FAQs
What material is best for sealing?
There is no “one size fits all” material that works for every seal application. That’s why we’ve developed The Engineers’ Guide to Selecting an Extruded Seal Material. It provides stats and specs for dozens of extrusion materials and will guide you through the most critical considerations so you can make the best choice possible for your unique application.
How can I prevent seals from buzzing, squeaking, and rattling (BSR)?
Buzzes, squeaks, and rattles (BSRs) are 100% preventable, yet they remains a major source of warranty claims. This is typically the result of improper material friction characteristics, chemical reactions, and/or environmental factors. To prevent seal chatter, take a look at the surrounding system.
- To what, and how, will the seal be attached?
- What is its proximity to other components?
- Will it be exposed to extreme temperatures, chemicals, or ozone?
Once you have an understanding of the application’s environment, you can predict potential BSRs and determine the best method of prevention. Some of the most common solutions include the application of a slip-coat, blending a slip-agent directly into the seal material, and applying flock tape or spray to exposed surfaces.
How can I prevent a rubber seals from staining or bleeding?
Staining and bleeding have long plagued rubber seal applications. Fortunately, you can prevent it.
Staining happens when additives in the rubber have some solubility with a mating surface; such is the case with the infamous rubber-footed table stain in the linoleum-floored kitchen. You can prevent this by creating a barrier between the mating materials.
Bleeding is the seepage of rubber additives, namely oils. There are some rubber compounds that are resistant to bleed, but the only way to prevent it entirely is to use an alternative material such as TPV.
What is the white powdery substance that builds up on the surface of a rubber part?
This phenomenon is referred to as “blooming,” and occurs when compounding agents in the rubber migrate, or bloom, to the surface. This is due to the agents’ limited compatibility with the rubber elastomer. It affects the tensile strength, adhesion properties, and appearance of your part.
What are the alternatives to rubber seals?
Depending on your seal application, you may have numerous alternatives to rubber. The most common is TPV, a rubber-like material that can be processed and recycled like plastic, but without the stain, smell, and blooming you see with rubber. It’s like a simplified rubber, allowing for more flexible part design, quicker manufacturing, reduced part/system costs, and weight reduction. Some other alternatives to rubber include TPO, TPU, TPZ, and PVC among others. To help you navigate the sea of options, we’ve developed the The Engineers’ Guide to Selecting an Extruded Seal Material.
what our customers say about working with Gemini Group
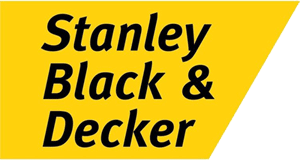
“Gemini Group knows blow molding. You do not have to be a blow molding expert to get the part you need for your application. They took care of the mold design, gauging, post-process machining, assembly, and leak testing. With their automotive supplier background, they will put a comprehensive quality control plan in place for your parts as well.”
Eric Plamper / Sr. Engineer: Fuel, Engine & Exhaust Systems / Stanley Black & Decker