Seal design can be an intimidating endeavor — whether a protective door edge guard or a high-performance radiator seal. Though every application is different, there are a number of factors every design engineer should consider on their quest to achieve a functioning seal. This article covers those factors in brief so you can get started.
If you’re designing a seal using the DFMA approach, download our free Seal Design Guide for a deeper dive.
Material Selection
Selecting the right material is the first and most critical step in designing a custom seal. Physical, resistance, and mechanical properties must all be taken into consideration for performance requirements, while material cost and processing must be considered to stay within budget. Add to that any regulatory or appearance guidelines and the task becomes daunting.
Luckily, companies like ours have been designing seals for decades and can assist in material selection for your seal. Start by determining the material properties required for the application:
Physical Properties
- Hardness range
- Gas permeability
- Water absorption
- Color
- Surface grade
Resistance Properties
- Weather, ozone
- Acids and alkalis
- Abrasion
- Flame
- Temperature
Mechanical Properties
- Tensile strength
- Compression set
- Compression deflection
- Flexibility
If, after considering these, you are still unsure what material would be best for your application, the our seals team can assist you.
Sealing Environment
What is the temperature range and length of exposure in the immediate and surrounding seal environment? What chemicals will the seal be exposed to? Is the application static with little or no movement relative to the seal, or is it dynamic with rotating or shifting motions? Since all of these factors are interrelated, you must accommodate all of them in your seal design.
Closing Force and Direction of Load
What is the amount of closing force that will be applied to the seal, and in what direction? A seal designed for 50 pounds of force from a 90-degree load may not work in an application where only 20 pounds of force will be applied from a 60-degree load, and vice versa.
Friction
What type of friction will the seal be exposed to, and for how long? Consider the seal dimensions, material hardness, and use of internal or external lubricants to help control the frictional force of the seal.
Gap
What is the gap or the opening the seal is going to fit into and be expected to seal? This includes both the minimum and maximum amounts of gap that exist throughout the application, taking into account tolerances of the enclosure and sealing material.
Attachment
Will the seal be attached mechanically or with an adhesive? For mechanical attachment, consider where and how the attachment device will be inserted into the seal so that it doesn’t interfere with the compression of the seal. For adhesive attachment, consider the thickness of the adhesive itself, as it will affect the overall height of the profile. Also consider the material of the seal and substrate it will be attached to, as well as the sealing environment.
Corners
There are two methods to fabricate corners in a sealing system: molding and hot splicing. Molded or overmolded corners create the most durable corner, but can be more costly. Hot splicing, achieved by melting the ends of two seals and combining them, is less expensive but less durable.
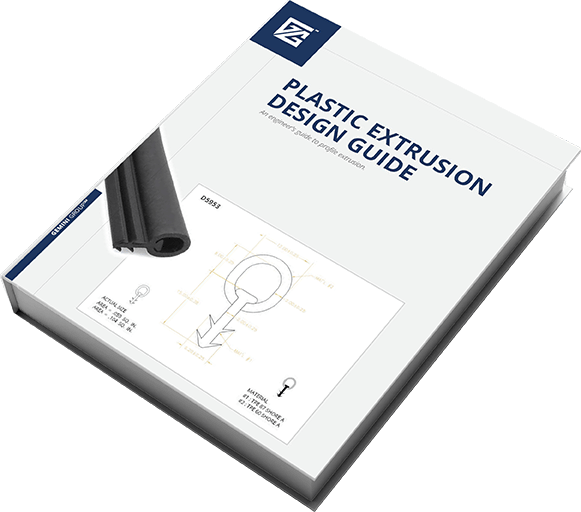
EXTRUDED SEAL DESIGN
We are proud to present to you the cumulation of over 50 years of experience in extrusion. We’ve helped thousands of engineers just like you with their extruded seal design – and this guide truly is the next best thing to working directly with our seals specialists.