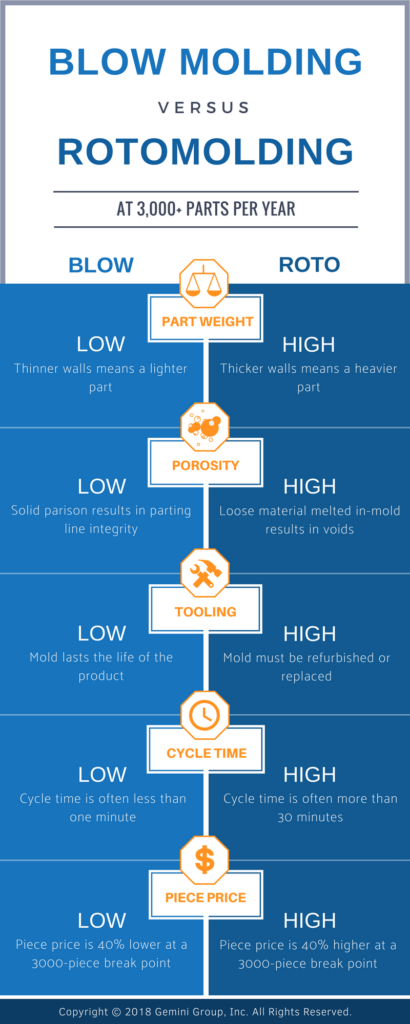
As you know, you can make large hollow plastic parts using rotational (roto) molding or blow molding. But, depending on several factors, including the type of parts made and the volume of parts produced, the differences between roto molding and blow molding can be significant. Here’s the bottom line:
If you’re producing fewer than 3,000 pieces of product per year, you might be better off using roto molding. But if your production volumes are higher, blow molding is the way to go because it can save 40 percent on per-piece cost.
COST DRIVERS | ROTO MOLDING | BLOW MOLDING |
---|---|---|
Tooling | $150,000 / yr | $200,000 / lifetime |
Production Rate | 2 parts / hr | 70 parts / hr |
Piece Price | $35 | $22 |
While per-piece cost is a very important metric in the comparison of roto molding to blow molding, other technical reasons make the case for blow molding as well, including cycle times, tooling, porosity, and part weight.
- Cycle time: As with most manufacturing processes, time is money. Naturally, shorter production times are more cost-effective. Roto molding cycle times are often more than 30 minutes while blow molding cycle times are often less than one minute.
- Tooling: With roto molding, tooling must be refurbished or replaced regularly. With blow molding, the mold lasts the life of the product.
- Porosity: With roto molding, plastic resin is tumbled around inside a hot mold in an attempt to fill in all the areas of the mold. Unfortunately, this still results in voids in the product. With blow molding, a solid parison (a tubular sheet of ready-to-be-formed plastic) avoids the voids, resulting in parting line integrity.
- Part weight: Roto molded parts, by their very manufacturing process, result in thicker walls. Which means parts are generally heavier than they otherwise could be. Blow-molded parts form with thinner walls. Which means parts are generally as light as they can be while meeting design requirements.
We deal with these design and manufacturing issues all the time and are glad to work with you to see if blow molding – the technical blow molding that has served our customers again and again – is the more sensible and cost-saving operation for your hollow part needs. Depending on volume of parts needed, blow molding may not be right for you compared to roto molding. But let’s have a conversation about your needs and see if there’s a good match.
To contact our technical blow molding experts, call 248-435-7271 or email plasticsales@geminigroup.net. We look forward to hearing from you!
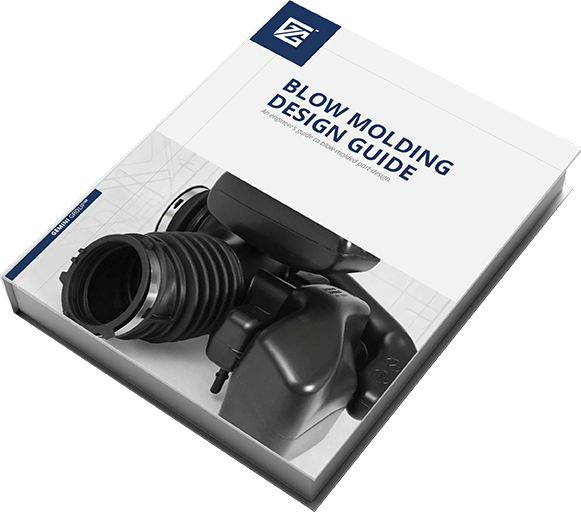
INTRO TO BLOW MOLDING DESIGN
If you’re new to blow molding and don’t know where to start, then our free Blow Mold Design Guide is for you! It will provide you with basic design guidelines for the injection, stretch, and extrusion blow molding methods so you can determine if this process is right for you.