Regency
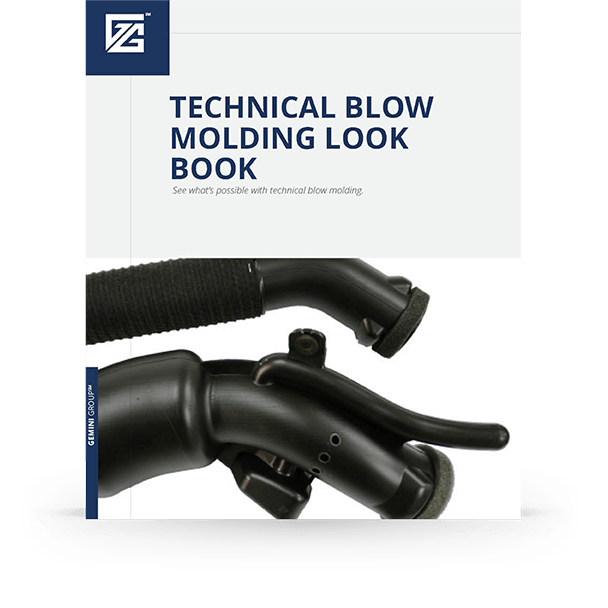
Over 3,000 Pieces? Think Blow Molding!
Rotomolding and blow molding both yield hollow plastic parts. So how do you decide which to choose? It all boils down to quantity and quality. Here’s where each process shines:
ROTOMOLDING
- Quantity: 1-3,000 parts per production run
- Dimensions: 4’x4’ or larger
- Wall features: Multi-layer walls, OD and ID control
- Common products: Plastic toys, kayaks, shipping containers
BLOW MOLDING
- Quantity: 3,000+ parts per production run
- Dimensions: 4’x4’ or smaller
- Wall features: Single-layer walls, OD control, no ID control
- Common products: DEF tanks, HVAC ducts, seat belt boots
If your part design meets the criteria for blow molding, we need to talk! You can save thousands by switching to blow molding. Call our technical sales staff at 248-435-7271 or shoot us an email at plasticsales@geminigroup.net with your project details.
See what blow molding can achieve!
Do you want to see what blow molding is capable of? Do you want to know what to look for when sourcing a supplier? Check out this look book of blow molded parts. Just fill out the form below and we’ll send you a link to the book today!
GET YOUR FREE COPY TODAY!
"*" indicates required fields
Rotomold VS Blow Mold
cost
Rotomolding, or rotational molding, involves heating plastic in an enclosed mold, rotating it to coat the walls of the mold evenly as the plastic cools and hardens into its final shape. A single rotomold machine can produce one to two parts per hour. The mold is typically cast aluminum, coming in at a lower price point than blow molding, but must be replaced after just a few thousand cycles.
Thus, rotomolding is better suited to low-volume production.
Blow molding involves vertically extruding a tube of plastic, then closing a mold around it and blowing the plastic into the walls of the mold until it hardens into its final shape. Think of it like blowing up a balloon inside of a water bottle. A single blow mold machine can produce 50 to 100 parts per hour. The mold is typically machined steel, coming in at a higher price point than roto molding, but is capable of running over a million cycles over the life of the mold.
Thus, blow molding is better than rotomolding for high-volume production.
quality
The greatest quality advantage of rotational molding is its ability to produce sturdy, multi-layered, walls with consistent wall thickness throughout. The greatest advantage of blow molding is its ability to produce parts with tight tolerances and difficult geometries repeatedly.
Thus, rotomolding is better when wall thickness is priority, whereas blow molding is better when part geometry is priority.
Learn more about the quality you should expect and the complexity you can achieve when you choose blow molding for your plastic part. Download your look book today!