Regency
TECHNICAL BLOW MOLDED PRODUCTS AND APPLICATIONS
We’re a trusted global supplier of blow molded plastic products to OEM and Tier-1 suppliers, achieving complex part geometries that most blow molding companies shy away from.
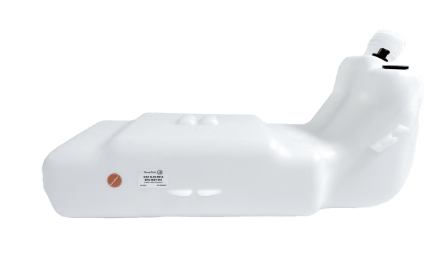
Fuel & DEF Tanks
Blow molding is an excellent alternative to traditional roto-molding for DEF tanks, allowing for mass production with a shorter cycle time, lighter part weight, and lower costs.
Our blow molded fuel and DEF tanks offer several benefits, including:
- EPA & CARB Certified
- Resistance to corrosion
- Lightweight construction
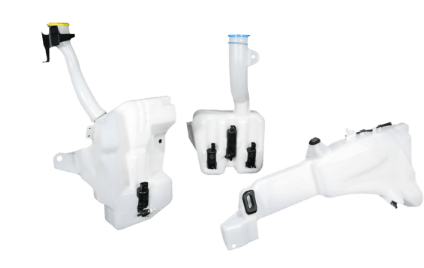
Fluid Reservoirs
We have the engineering expertise to help you design the complex geometries needed for fitting fluid reservoirs and tanks in existing system components.
Our plastic reservoirs are known for their:
- Intricate designs
- Fixed capacity
- Leak-proof interfaces
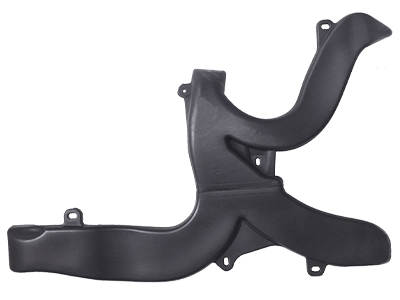
HVAC Ducts
With excellent resistance to temperature variations and airflow optimization, our HVAC ducts ensure optimal performance in various applications.
Key features of our HVAC components include:
- High airflow capacity
- Excellent insulation properties
- Reduced noise transmission
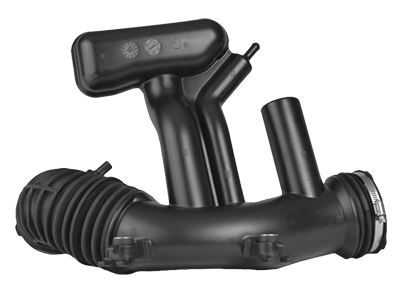
Air Intake Assemblies
Our technical blow molding processes allow air intake ducts, resonators, tuners, and injection molded plastic cuffs to be integrated into a one-piece assembly – something other blow molding suppliers often shy away from.
Our blow molded air intake assemblies offer:
- Enhanced engine performance
- Durability in harsh environments
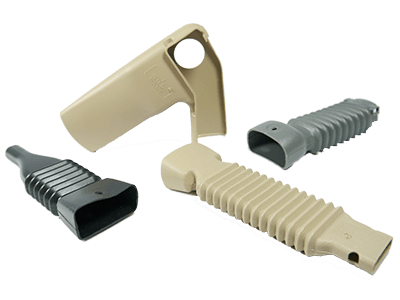
Seatbelt Boots & Sleeves
Whether you need a color matched PVC or a soft touch TPO seatbelt boot, we have the expertise to turn your concept into reality.
Key features of our blow molded seatbelt components include:
- Class A, grained surfaces
- Custom color-matching
- Resistance to wear and tear
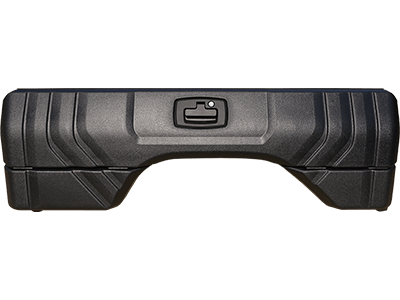
Other
The versatility of our technical blow molding process enables us to create a wide range of functional and durable plastic components. If it’s hollow, chances are we can make it.
Some of the less common blow molded components we make include:
- Cargo bins
- Seating
- Tool cases
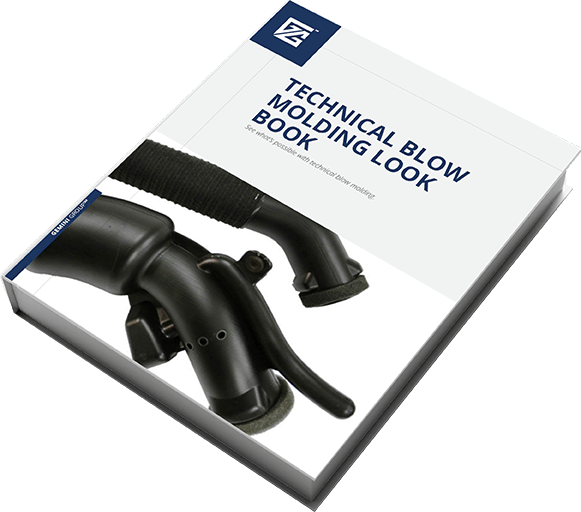
Technical Blow Molding Look Book
Rotomolding and blow molding both yield hollow plastic parts. So how do you decide which to choose?
Wherever You’re Located, We’re Here to Help
18 strategic locations in North America to meet the needs of our diverse customer base.
Get to know us. Get in touch today.
We have the resources to meet any part or production challenge. Let’s talk about what that means for you.
"*" indicates required fields