GPI, GT Plastics, Sierra, GPM
Plastic Extrusion and Co-Extrusion Process
Our plastic extrusion team are experts in single extrusion and co-extrusion manufacturing methods. We’re uniquely equipped to push the boundaries of what’s possible and drive cost out of our customers’ parts.
WHAT IS PROFILE EXTRUSION?
Profile extrusion is a highly versatile manufacturing process that allows us to create custom plastic profiles with precise cross-sectional shapes.
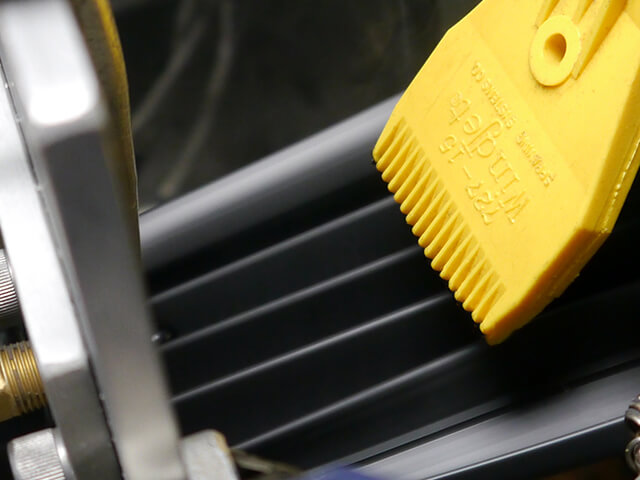
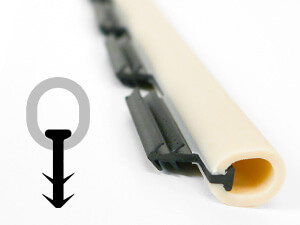
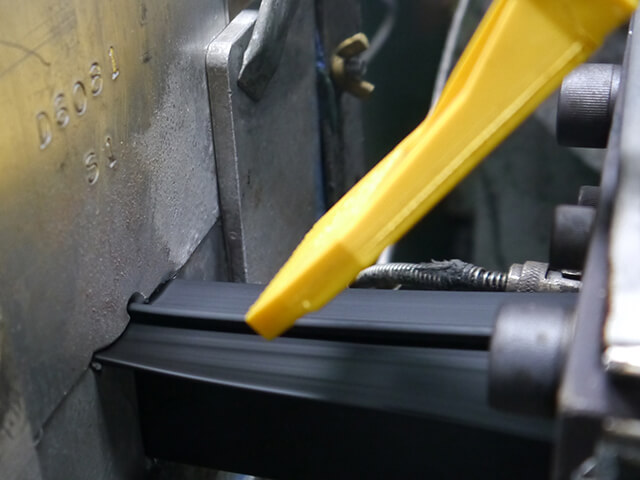
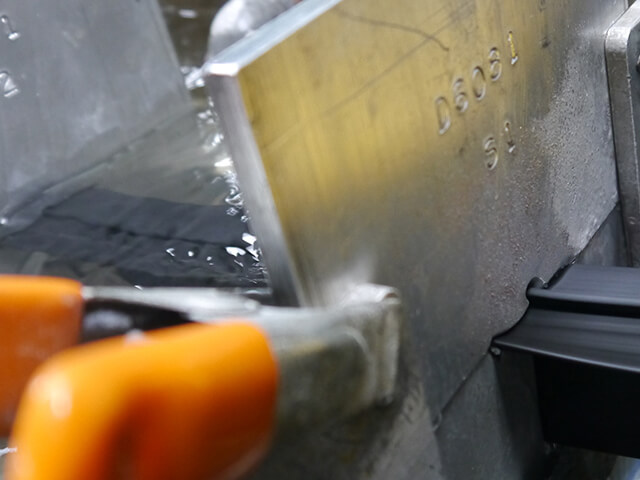
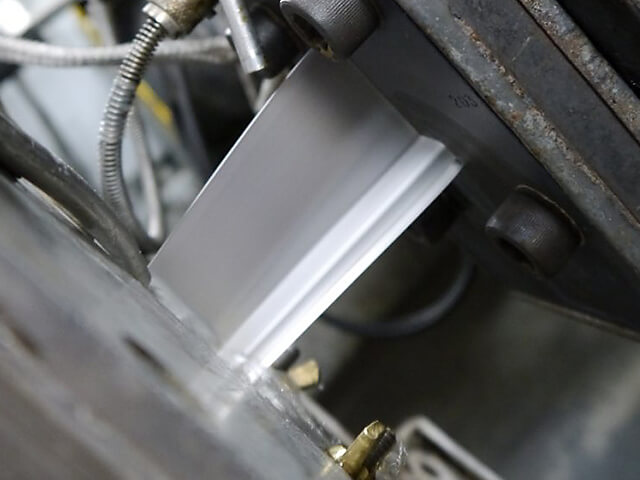
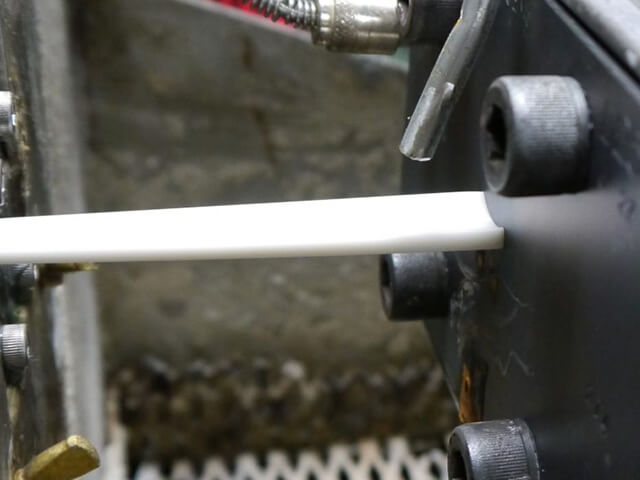
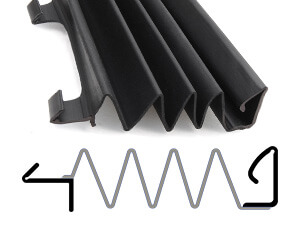
Profile Extrusion Process
The plastic profile extrusion process starts by melting plastic pellets and pushing it through a die with the desired cross-section, or “profile”. The formed plastic then passes through a vacuum to help it maintain it’s shape, if necessary. It is then pulled through a water bath until fully cooled. Now, the extrusion is ready to fabricate and either cut into multiple parts or wind as a single part.
A special technique called co-extrusion takes it to the next level by extruding two materials at once, often used to make parts that require both rigid and flexible components or two colors.
Benefits of Profile Extrusion
Complex/Custom Profiles
Our advanced extrusion technology enables us to produce intricate profiles tailored to meet our customers’ specific design requirements.
Hollow Profiles
We can create profiles with internal voids, allowing for weight reduction, improved insulation, and enhanced structural integrity.
Living Hinges
Our extrusion process facilitates the creation of flexible living hinges, which are crucial for applications requiring repeated opening and closing.
Single & Multi-durometer
We have the capability to extrude profiles with varying degrees of hardness, allowing for the integration of different functional properties within a single component.
Plastic CO-EXTRUSION: EXPANDING POSSIBILITIES
In addition to profile extrusion, we specialize in co-extrusion, a process that involves simultaneously extruding multiple materials to create composite profiles.
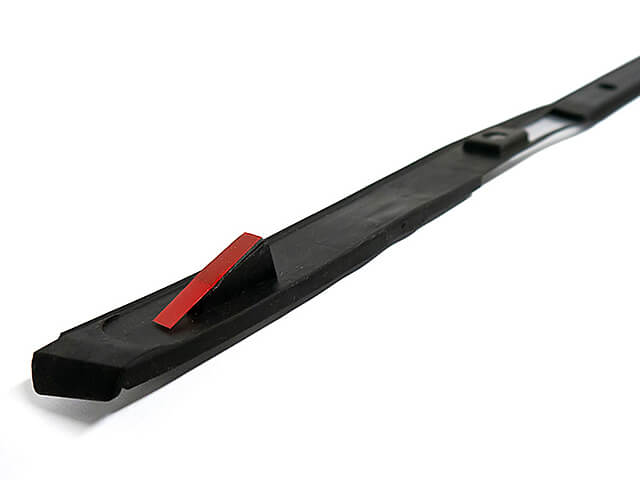
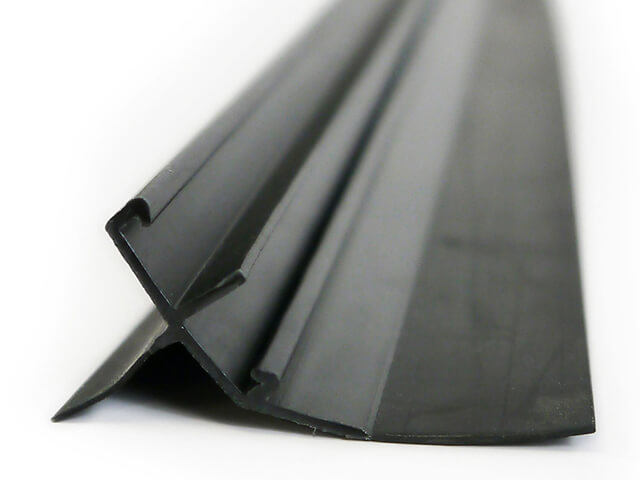
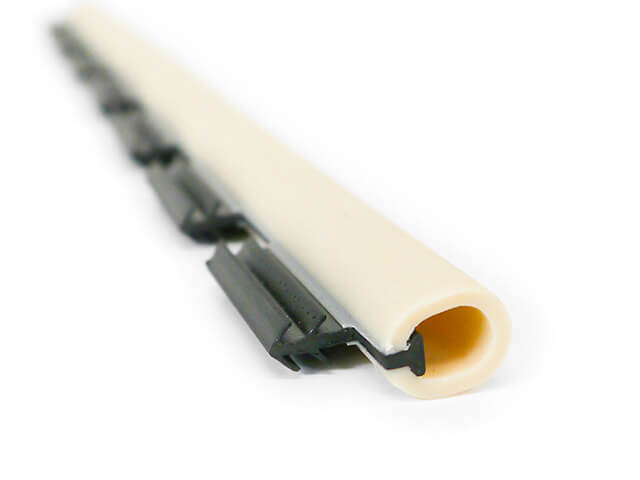
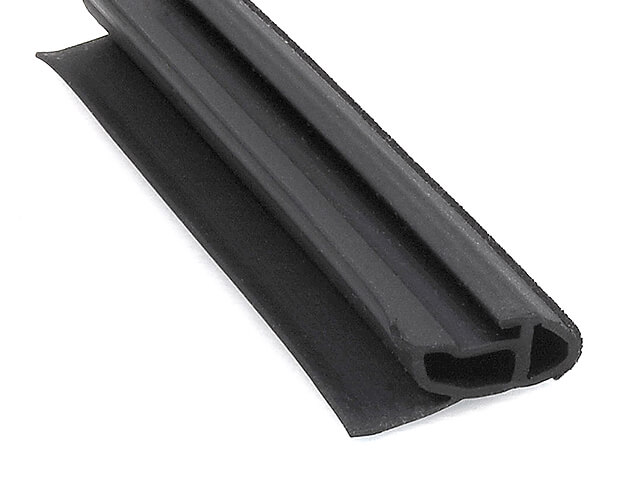
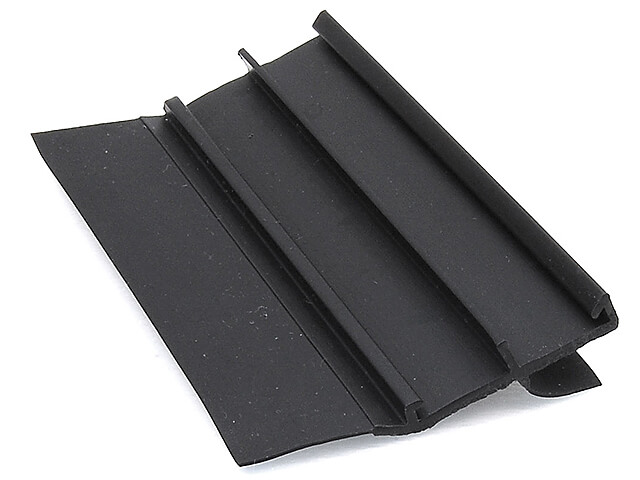
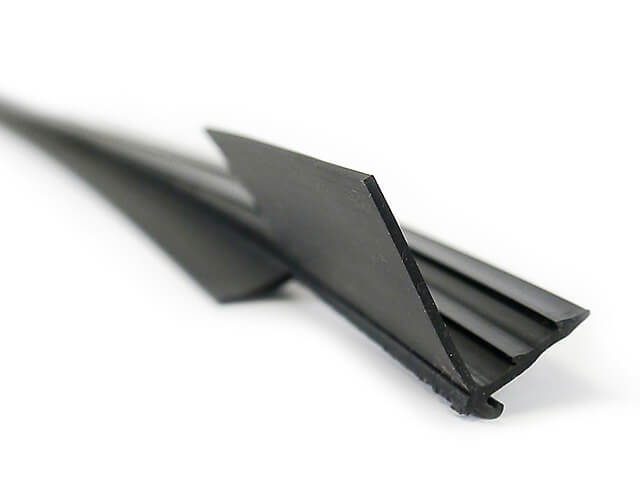
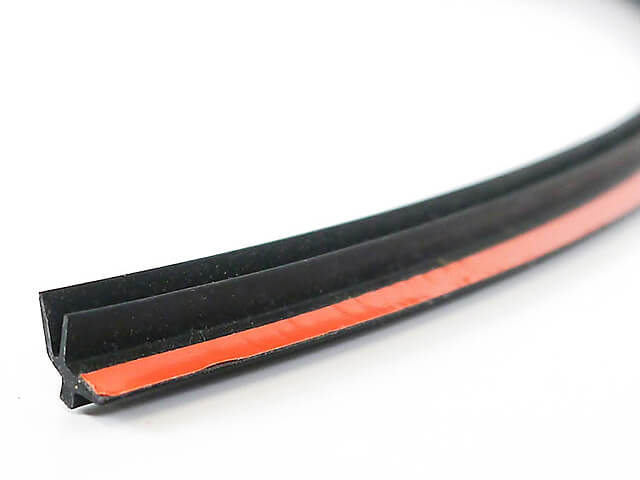
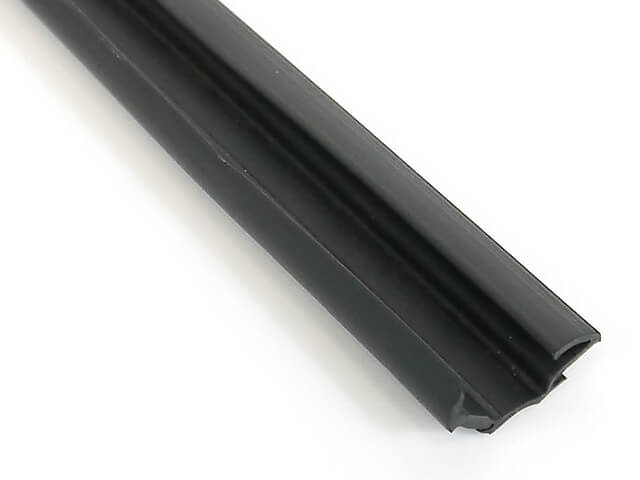
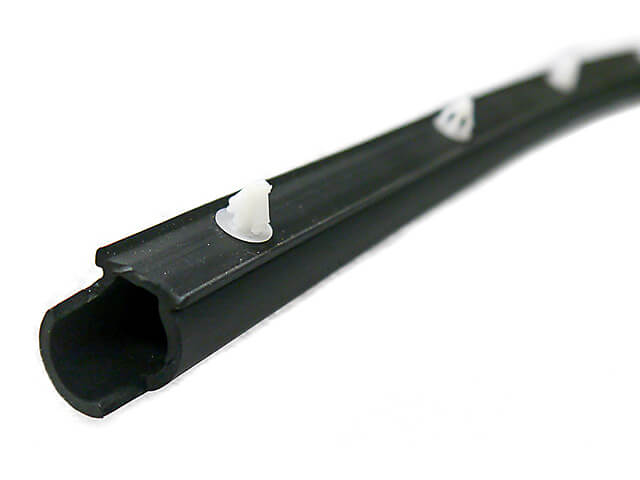
Plastic co-extrusion opens up a world of possibilities by combining different materials with distinct properties in a single profile. Each material used maintains its desired characteristic properties (such as stiffness, impermeability, or environmental-resistance), all of which would be impossible to attain with any single material.
This technique enables us to enhance functionality, improve aesthetics, and achieve unique performance characteristics.
BENEFITS OF THECO-EXTRUSION PROCESS
Material Flexibility
Co-extrusion allows us to combine materials with complementary properties, such as strength, flexibility, or chemical resistance, to push the limits of functionality.
Cost and Weight Reduction
By using different materials strategically, we can reduce the overall cost and weight of the final part without compromising functionality or durability.
Design Versatility
Co-extrusion provides the flexibility to incorporate different colors, textures, or surface finishes within a single profile, enhancing the visual appeal and branding opportunities.
IN-LINE PROCESSING
We offer a range of in-line processing and secondary operations to further enhance the functionality and aesthetics of our extruded profiles.
Punching and Laser Cutting
In-line punching and cutting enables us to incorporate holes, slots, and custom shapes into the extruion with a high level of uniformity and repeatability.
Printing
In-line printing enables us to apply graphics, logos, or product information directly onto the profiles, enhancing branding and visual appeal.
Cutting and Rolling
We can either cut the extruded profiles to specific lengths for easier assembly or roll them into coils for easier handling and transportation.
Slipcoats, Flock, Adhesives, and Tape
To provide additional surface characteristics, we can apply slipcoats or flock for improved lubricity, and adhesives or tapes for bonding.
This streamlined approach eliminates the need for additional processing, thus enhancing repeatability, improving quality, and reducing costs for our customers.
Why Choose Us?
With over 7,000 profiles under our belt and millions of extrusions shipped annually, we have the experience to turn your concept into reality.
Experience the difference of working with a trusted industry leader. We are committed to delivering excellence, providing innovative solutions, and exceeding your expectations.
EXPERTISE
To put it simply, we’ve honed our skills and techniques to perfection. Our knowledgeable team is dedicated to delivering top-notch results.
INNOVATION
We thrive on innovation and constantly push the boundaries of what is possible, ensuring that our customers have the best available options for design and cost.
PARTNERSHIP
We believe in building long-term partnerships with our customers. A strong relationship built on trust enables both parties to push each other towards greater success.
Wherever You’re Located, We’re Here to Help
18 strategic locations in North America to meet the needs of our diverse customer base.
Insights
Get to know us. Get in touch today.
We have the resources to meet any part or production challenge. Let’s talk about what that means for you.
"*" indicates required fields