Valley Enterprises, GGIT
Other Manufacturing Methods
With an array of plastic forming techniques, including thermoforming and twin sheet molding, we deliver products of unmatched quality. Our knowledge and experience in these processes transforms your vision into reality, ensuring innovation and precision in every product.
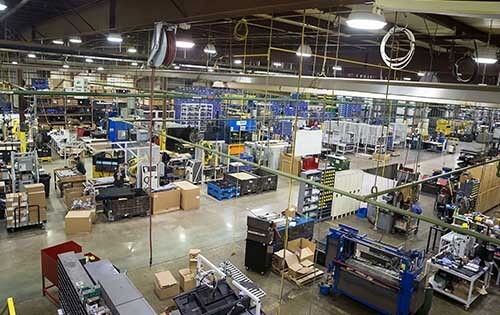

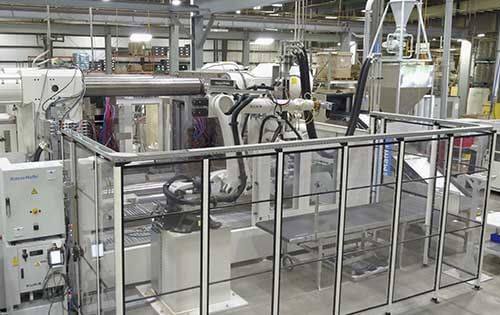
Injection Molding
Injection molding plays a crucial role in achieving the aesthetic appeal, functionality, and durability required for automotive interior parts. With injection molding machines up to 3000 ton, we have the capabilities to support all your interior trim needs.
- Design Flexibility – Optimizing part performance and functionality.
- Material Variety – We process a wide range of thermoplastic materials.
- High Efficiency – We’ve become extremely proficient enabling rapid production and large volumes.
Thermoforming: Shaping the Future
Using negative air pressure (vacuum) and heat, we create consumer packaging, headliner stiffeners, and more.
- Low Tooling Costs – The process’s gentle forming pressure enables cost-effective tooling made from affordable materials.
- Ideal for Large Parts – It’s a boon for large parts as the low tooling costs make it perfect for small to medium production runs.
Twin Sheet Molding: The Fusion of Mastery
Twin sheet molding is brought to life as we blend compression molding, blow molding, and vacuum forming into a seamless process.
- Multiple Materials – Each sheet can differ in thickness, color, or material, adding a world of possibilities.
- Enhanced Flexibility – Offers greater flexibility in parting line structure.
- Aesthetics – Smooth, high quality surface finishes reducing the need for secondary finishing operations.
Wherever You’re Located, We’re Here to Help
18 strategic locations in North America to meet the needs of our diverse customer base.
Insights
Get to know us. Get in touch today.
We have the resources to meet any part or production challenge. Let’s talk about what that means for you.
"*" indicates required fields