Valley Enterprises, GGIT
Excellence in Automotive Interior Trim Processes
Our automotive interior trim processes are elevated to an art form. We specialize in a comprehensive range of techniques, each meticulously tailored to produce flawless interior components. No cookie-cutter solutions here – our diverse set of processes ensures a harmonious fit for your components while strategically optimizing costs and expediting time to market.
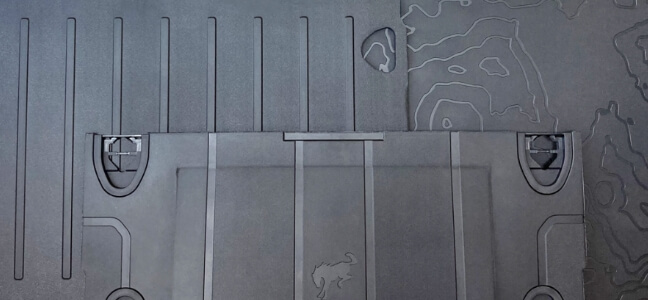
U-SKIN
Our innovative surface technology provides customizable, tough, and functional applications for automotive applications.
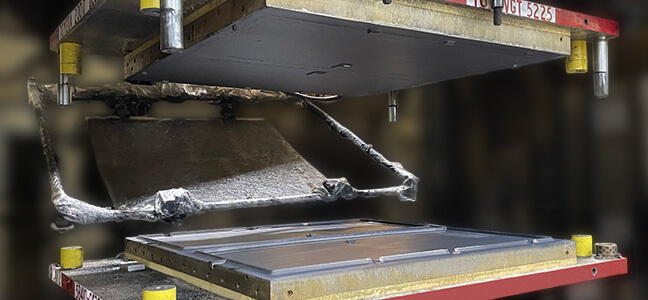
Composite Spray Molding (Baypreg)
Our advanced composite spray molding technology ensures lightweight, low profile, rigid load floor substrates.
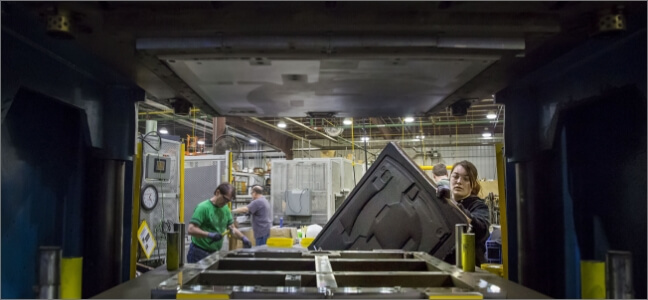
Compression Molding
Our mastery of compression molding opens doors to shaping high-strength substrates, such as, natural fiber, fiberglass composites, and carpet.
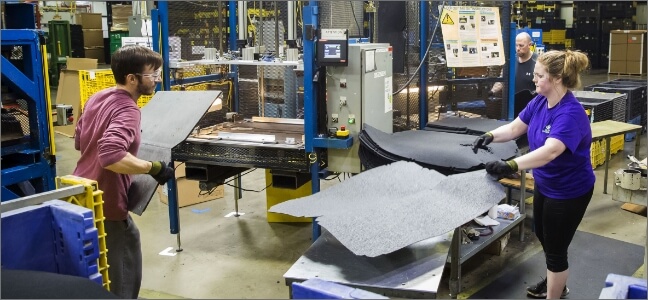
Other manufacturing methods
Our expertise in injection molding, twin sheet molding, and thermoforming enable us to provide you with the best process choice available.
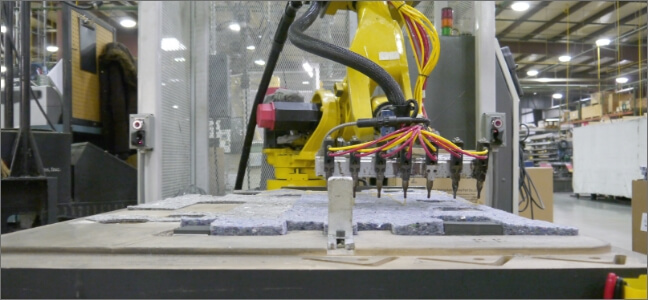
Secondary Operations
Our proficiency extends far beyond these processes. From automated edge wrapping to sonic welding, each process showcases our dedication to achieving excellence from every angle.
Wherever You’re Located, We’re Here to Help
18 strategic locations in North America to meet the needs of our diverse customer base.
Insights
Get to know us. Get in touch today.
We have the resources to meet any part or production challenge. Let’s talk about what that means for you.
"*" indicates required fields