The quality of an extruded plastic profile is directly related to the level of control over the flow and cooling of the extrusion materials as they are processed. The single most influential factor of control, and thus quality, is profile wall thickness.
Uniform Wall Thickness
Semi-molten plastic will always follow the path of least resistance as it is pushed through the extrusion die. The larger the hole, the quicker it flows. This behavior makes it very difficult to regulate the flow of material through unbalanced walls. Controlling the flow in these scenarios is possible but requires specialized tooling that can be cost-prohibitive.
Left uncontrolled, an uneven flow of plastic creates distortions as the material moves more quickly through the thicker wall sections. Further, thicker sections take longer to cool than thinner sections and result in bowing and twisting of the finished part.
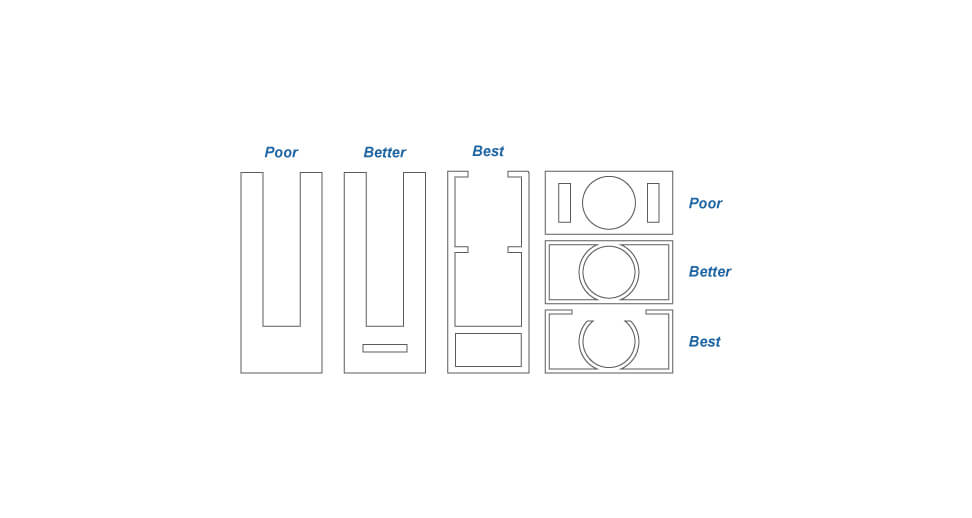
In short, the wall thickness of your profile should be as uniform as possible for the best results. It’s a simple but key concept that must be applied to your profile design if you want a quality part.
Wall Thickness in Corners
The elements that are most often overlooked in profile design are corner radii. A 90 degree corner may appear to have uniform thickness, but it’s actually thicker at the joint unless a radius is worked in to the inner and outer walls.
As insignificant as it may seem, corner radii have a significant impact on the flow of plastic through the profile die. As such, inside and outside radii should be offset to maintain a uniform wall.
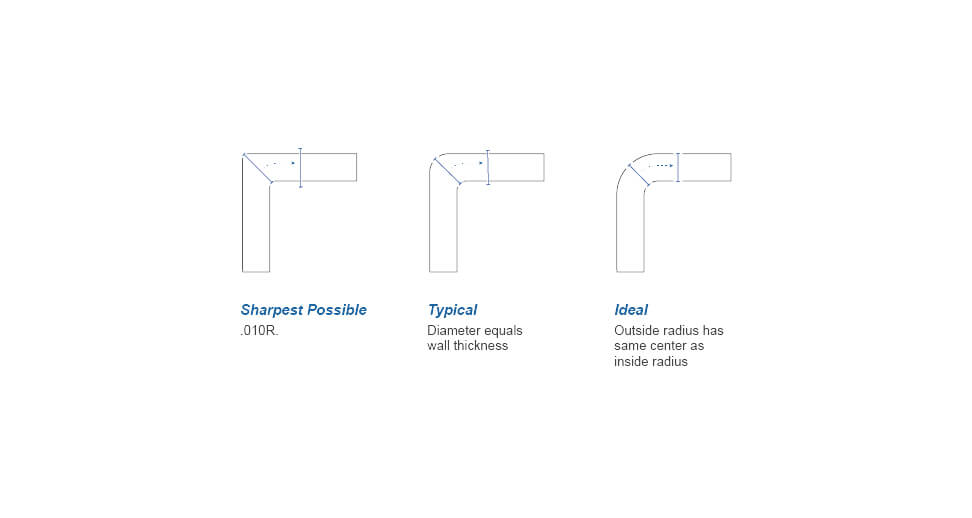
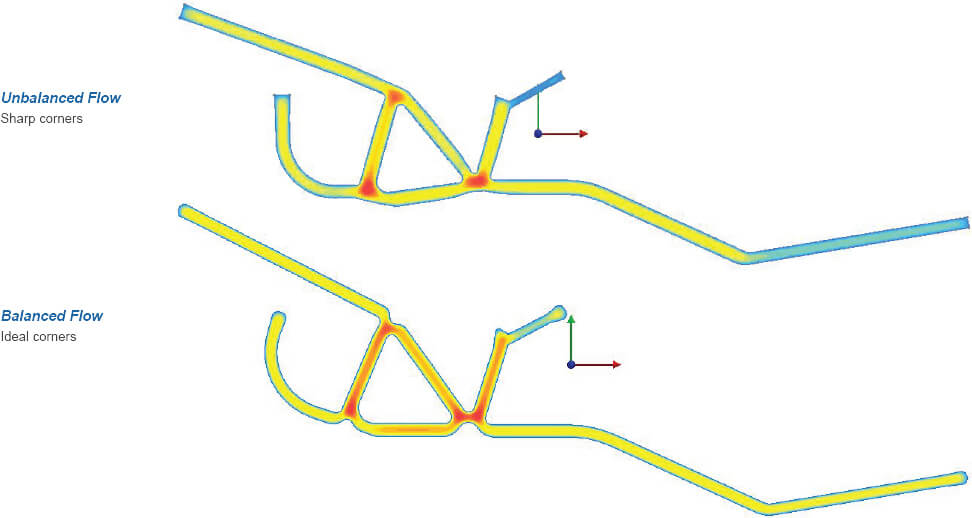
Wall Thickness Tolerances
Even with completely uniform walls throughout the profile design, there will inevitably be some variation in the wall thickness in the finished part. This is due to the shrink rate of plastics as they cool. More rigid material such as PVC will have a lower shrink rate and will experience less variation than flexible materials such as TPE, but all plastics shrink to some degree as they cool.
The key to a successful part is to keep the variation within a tolerable range. Luckily, most extrusions will meet performance requirements under a standard range of tolerances that most extruders can hold. Here’s the standard for wall thickness:
Wall Thickness | Tolerance |
---|---|
.00 – 2.0 mm | +/- 0.25 mm |
2.01 – 3.18 mm | +/- 0.30 mm |
3.19 – 5.0 mm | +/- 0.38 mm |
* These are general guidelines. Actual tolerances may vary based on material and part design.
Complex parts and critical features may require tighter tolerances than the standard, in which case modifications can be made to the material, design, and process conditions to maximize tolerance control.
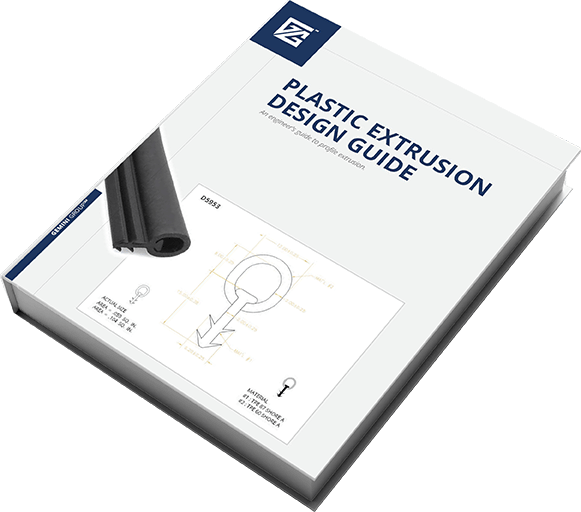
PLASTIC EXTRUSION DESIGN GUIDE
Is your extrusion design optimized to meet the constraints of the extrusion process? This free guide offers a solid foundation in the requirements for successful extrusion design. Created by engineers for engineers, and based on decades of extrusion development and manufacturing experience.