Regency
EXTRUSION BLOW MOLDING PROCESS
We specialize in the most advanced method of blow molding – extrusion blow molding. This method allows us to create highly technical, highly functional parts while improving lead times and reducing costs compared to other molding methods.
“Technical” Blow Molding
We often get asked how “technical” blow molding is different than your everyday, run-of-the-mill, blow molding. The main difference lies in the complexity and precision of the produced parts.
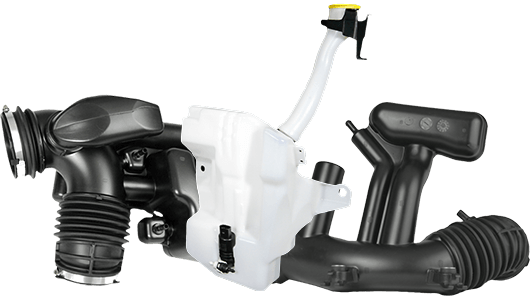
Technical Blow Molding
Technical blow molding refers to the extrusion blow molding process. It’s is used for producing highly engineered products with critical functional requirements such as fluid reservoirs and HVAC ducts. It involves the use of advanced machinery and sophisticated control systems that allow for complex geometries, higher tolerances, as well as the ability to incorporate inserts or achieve specific material properties.
VS
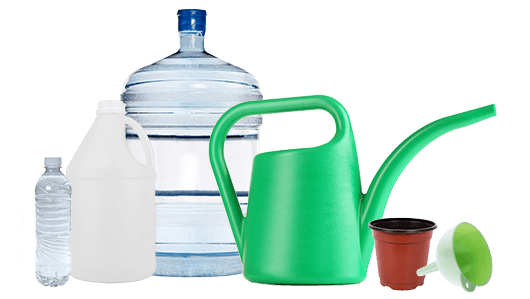
Standard Blow Molding
Standard blow molding refers to injection and stretch blow molding methods. It’s used for plastic products with standard material properties, basic geometries, and simple functionality such as water bottles and cosmetic containers. It’s pretty commonplace, generally less complex, and requires less precision.
Extrusion Blow Molding Process
The first step in the extrusion blow molding manufacturing process is the extrusion of a tube, also called a “parison”, of viscous plastic into a product mold. The mold closes around the parison and air is pumped in to inflate the parison against the mold walls. Once the plastic cools back to a solid state, the mold opens and the part is ejected. Finally, the excess material along the mold pinch line is removed by a process called deflashing and the part is ready to undergo any secondary operations that are needed to finish the part.
Step 1: Parison is extruded into the mold
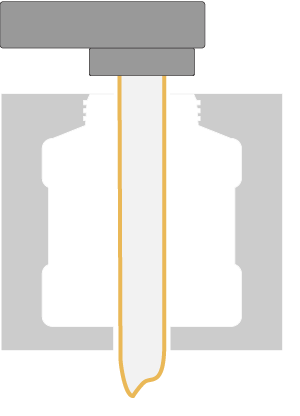
Step 2: Blow mold seals around parison
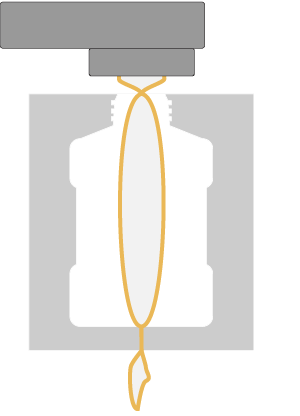
Step 3: parison is inflated with air
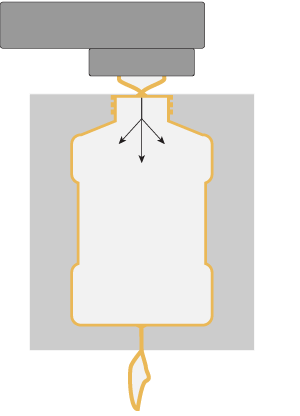
Step 4: parison cools and mold opens
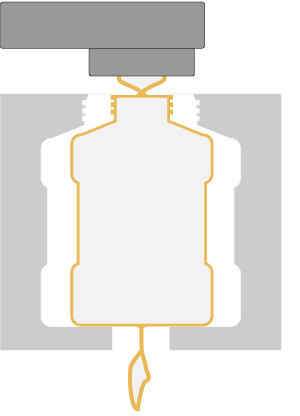
Compression molding and insert molding are often combined with the process of extrusion blow molding in order to maintain ID and OD tolerances and add features to the product:
PLASTIC COMPRESSION MOLDING
Typically, extrusion blow molding plastic is suited for tight control of the outer diameter (OD) of a part but does not allow for completely accurate tolerances of the interior diameter (ID). By combining the plastic compression molding process with the blow molding process, we can precisely control both the OD and ID of your part.
PLASTIC INSERT MOLDING
In the case of integrating plastic insert molding with the process of blow molding plastic, we can incorporate fasteners and/or other inserts directly within the mold. This eliminates steps in the production process such as riveting or welding which add time without adding value, and creates a stronger bond between the blow-molded and insert-molded components.
Is Blow Molding Right For Me?
Blow molding is the fastest and most cost-effective plastic molding process when production volume reaches 3,000+ parts per year. With an increasing focus on lightweighting and sustainability, it’s no wonder why engineers across the globe in nearly every industry have turned an eye towards blow molding for their high-production needs. Among its many benefits include:
Low Cost for High Volume Production
Blow molding is more cost-efficient than other processes such as rotomolding and thermoforming for mass-produced hollow parts.
High Strength-to-Weight Ratio
Parts can be reinforced with a lightweight foam core or internal ribs to increase structural strength and impact resistance.
Design Flexibility
Complex part geometries can be achieved to adapt to unusual spaces between already existing components.
Insulation and Acoustical Properties
Hollows can be vacuumed or filled with a material to achieve high insulation and noise reduction properties.
sourcing a supplier
We have over 30 years of technical blow molding experience. We know the importance of seeing each project through from inception to final production.
First and foremost, our intent with each new opportunity is to determine if there is a good fit for our blow molding process. If there is, we will assist you on material, process, pricing, logistics, quality, and DFM/DFA issues. On the other hand, if there isn’t a good fit we will do our best to connect you with someone who is better suited to fill the needs of your specific project.
Contact us to learn more or send us your drawings for a quote.
case study
Converting a Rotomolded DEF Tank to Blow Molding
Discover how blow molding helped a Tier 1 supplier of custom fluid management consolidated their supply chain, increase efficiency, and reduce costs while meeting all production and performance requirements.
Wherever You’re Located, We’re Here to Help
17 strategic locations in North America to meet the needs of our diverse customer base.
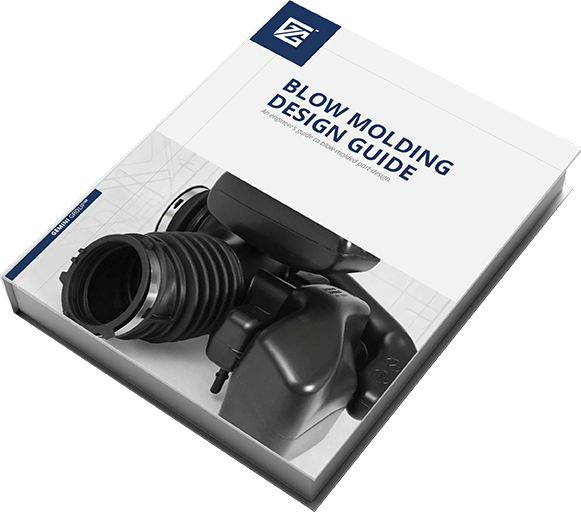
INTRO TO BLOW MOLDING DESIGN
If you’re new to blow molding and don’t know where to start, then our free Blow Mold Design Guide is for you! It will provide you with basic design guidelines for the injection, stretch, and extrusion blow molding methods so you can determine if this process is right for you.
Insights
Get to know us. Get in touch today.
We have the resources to meet any part or production challenge. Let’s talk about what that means for you.
"*" indicates required fields