Regency
IN-HOUSE TOOLING
Through the use of protype tooling that converts to production tooling, as well as insert tooling for quick iterations, we eliminate the need for redundant tooling changes. We also build nearly all fab tooling in-house, reducing lead times by an average of 2-4 weeks.
Convertible Prototype Tooling
One of the first steps we take when developing any new blow molded products is stage tooling. This involves assessing the feasibility of building prototype tooling that converts to production tooling.
Once the prototype tooling consistently produces parts to your specifications, we add finishing details such as vents and cooling lines to make it production-ready. The use of convertible tooling greatly improves lead times and reduces tooling costs.
Insert Tooling Technique
We use insert tooling for critical areas or areas of uncertainty that need testing and may need to be modified. The insert technique allows us to run a prototype part that you can test for compatibility and functionality. If changes need to be made, the insert is simply replaced with the updated design, saving you the cost of having to rebuild the entire mold from scratch.
Trim & Fabrication Tooling
Out of the gate, our customers gain the advantage of 2-4 week reduced lead-times on tooling as all trim and fabrication tooling is designed and built in-house; eliminating the need for outside tooling shops.
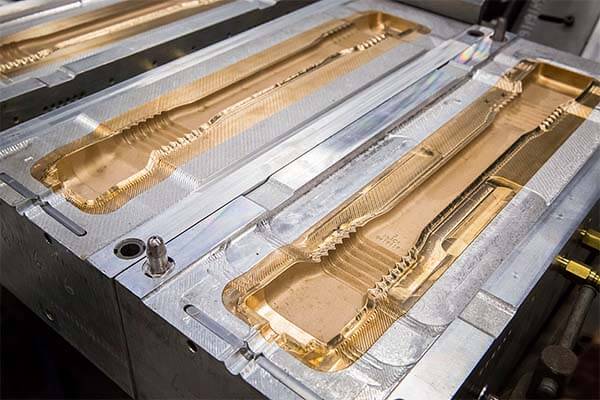
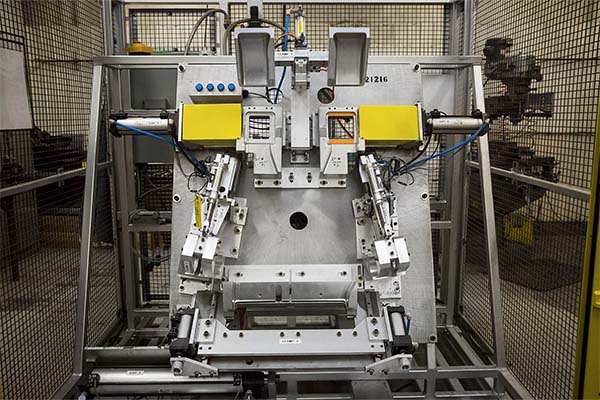
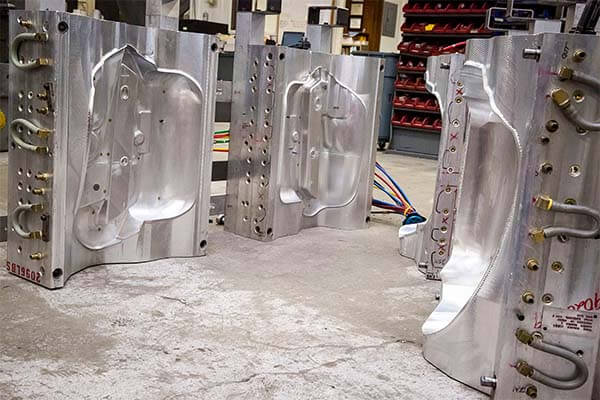
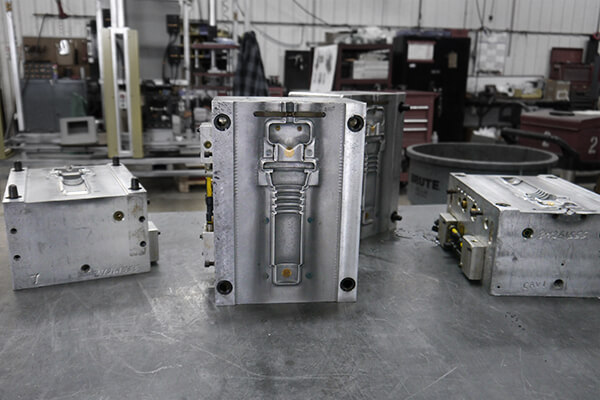
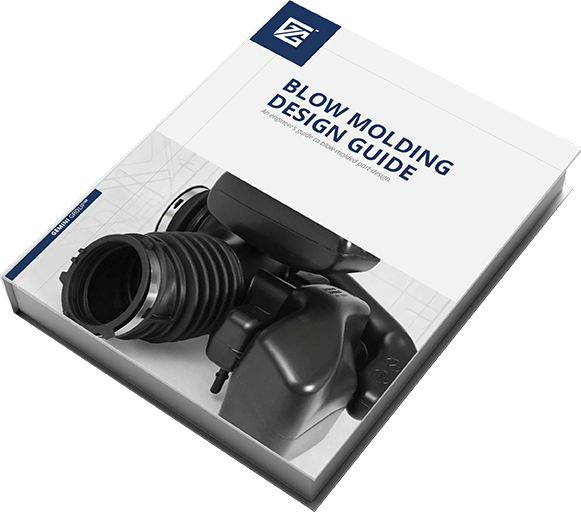
INTRO TO BLOW MOLDING DESIGN
If you’re new to blow molding and don’t know where to start, then our free Blow Mold Design Guide is for you! It will provide you with basic design guidelines for the injection, stretch, and extrusion blow molding methods so you can determine if this process is right for you.
Wherever You’re Located, We’re Here to Help
17 strategic locations in North America to meet the needs of our diverse customer base.
Insights
Get to know us. Get in touch today.
We have the resources to meet any part or production challenge. Let’s talk about what that means for you.
"*" indicates required fields