Regency
BLOW MOLDING SIMULATION & DESIGN TESTING
Despite popular opinion, blow molding is a science, not an art. While many molders continue to rely on trial-and-error methods to refine part designs, we utilize cutting-edge simulation software to optimize wall thickness, part weight, and cycle times.
Eliminate the Guesswork
Every project begins by creating 3D models of each mold half based on your part design. From there, we can simulate the plastic parison extrusion and inflation, die swell, warpage, and other behaviors as it fills the mold and cools during the blow molding process. No more guesswork, no more headaches.
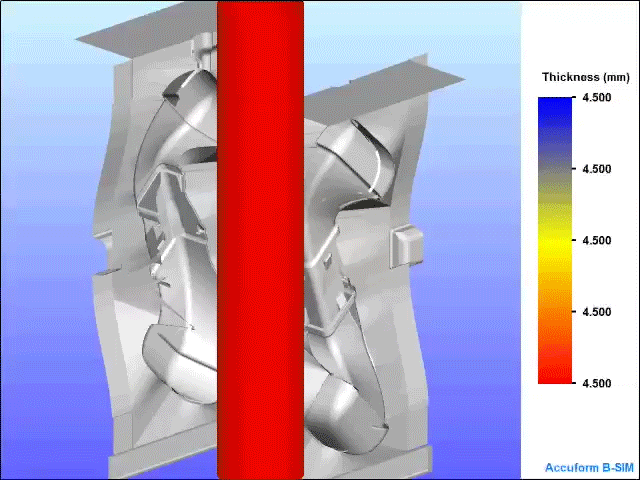
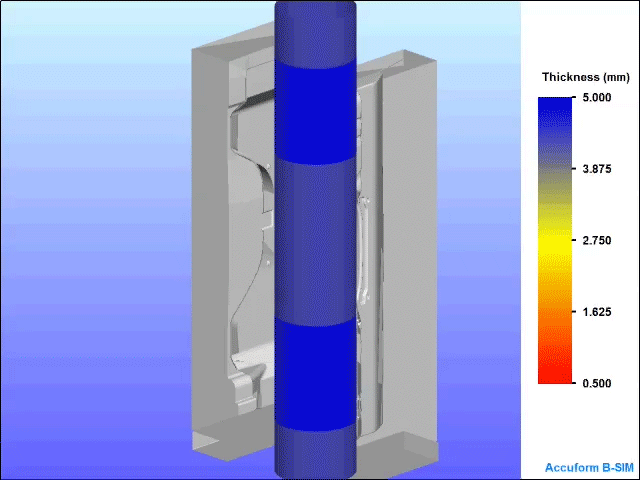
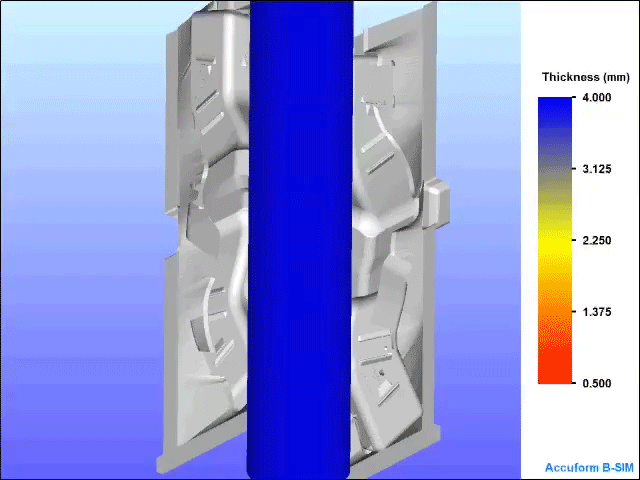
Optimize
Part
Design
Blow molding simulation allows us to identify problem areas and recommend design changes to optimize your part design.
- Optimize wall thickness
- Reduce cycle time
- Reduce part weight
Optimize
Tooling
Process
By transferring trial-and-error discovery to the computer at an earlier point in the design phase, we can optimize the tool-building process.
- Reduce development time by up to 40%
- Cut tooling in fewer steps
- Reduce tooling lead time and cost
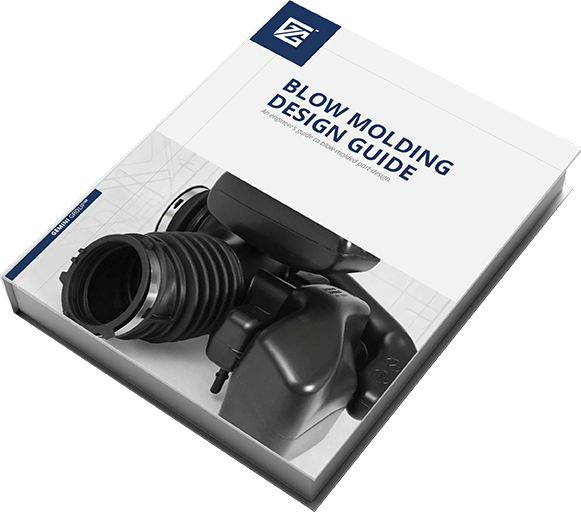
OPTIMIZE YOUR BLOW MOLDING DESIGN
Design is the key driver of the cost and quality of blow molded parts. It has the power to give your company a competitive advantage or it can bring your project to a screeching halt. Check out our Blow Molding Design Guide to learn how to optimize your design for the blow molding process.
case study
Converting a Rotomolded DEF Tank to Blow Molding
Discover how blow molding helped a Tier 1 supplier of custom fluid management consolidated their supply chain, increase efficiency, and reduce costs while meeting all production and performance requirements.
Wherever You’re Located, We’re Here to Help
17 strategic locations in North America to meet the needs of our diverse customer base.
Insights
Get to know us. Get in touch today.
We have the resources to meet any part or production challenge. Let’s talk about what that means for you.
"*" indicates required fields