Regency
Technical Blow Molded HVAC Ducts
We understand the tight packaging constraints involved in HVAC duct design and can help work around the geometrical restrictions imposed by other vehicle components. That’s why OEM’s and Tier 1 suppliers across the globe partner with us for the development and manufacturing of their custom blow-molded HVAC duct components and assemblies. We have the resources and expertise to assist with your design, engineering, tooling, and production needs.
Engineered For Performance and Efficiency
Designing HVAC duct components and assemblies can be complex and challenging, but it doesn’t have to be.
Whether your project calls for…
- IP Ducts
- Console Ducts
- Floor Ducts
- Seating Ducts
- SWD Ducts
- Headliner Ducts
Are you sourcing a custom HVAC duct or simply looking to update your benchmark?
If you need to achieve complex geometries or you spend north of $100,000 annually in blow molding, we should talk. Contact us today for an accurate and timely quote.
Blow Molded HVAC Duct Gallery: Components and Assemblies
Blow molding is the ideal manufacturing process for HVAC components and assemblies. It can achieve difficult part geometries with tight tolerances, produce high impact and structural integrity, and is more cost-effective than alternative molding methods such as rotomolding. Here’s a small sample of some common HVAC components manufactured through blow molding:
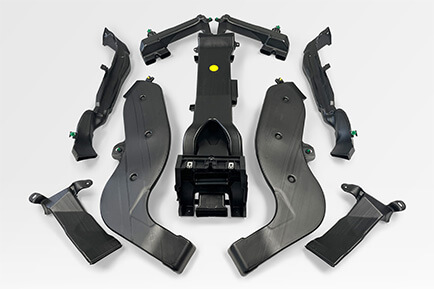
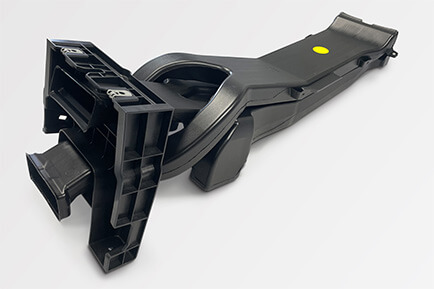
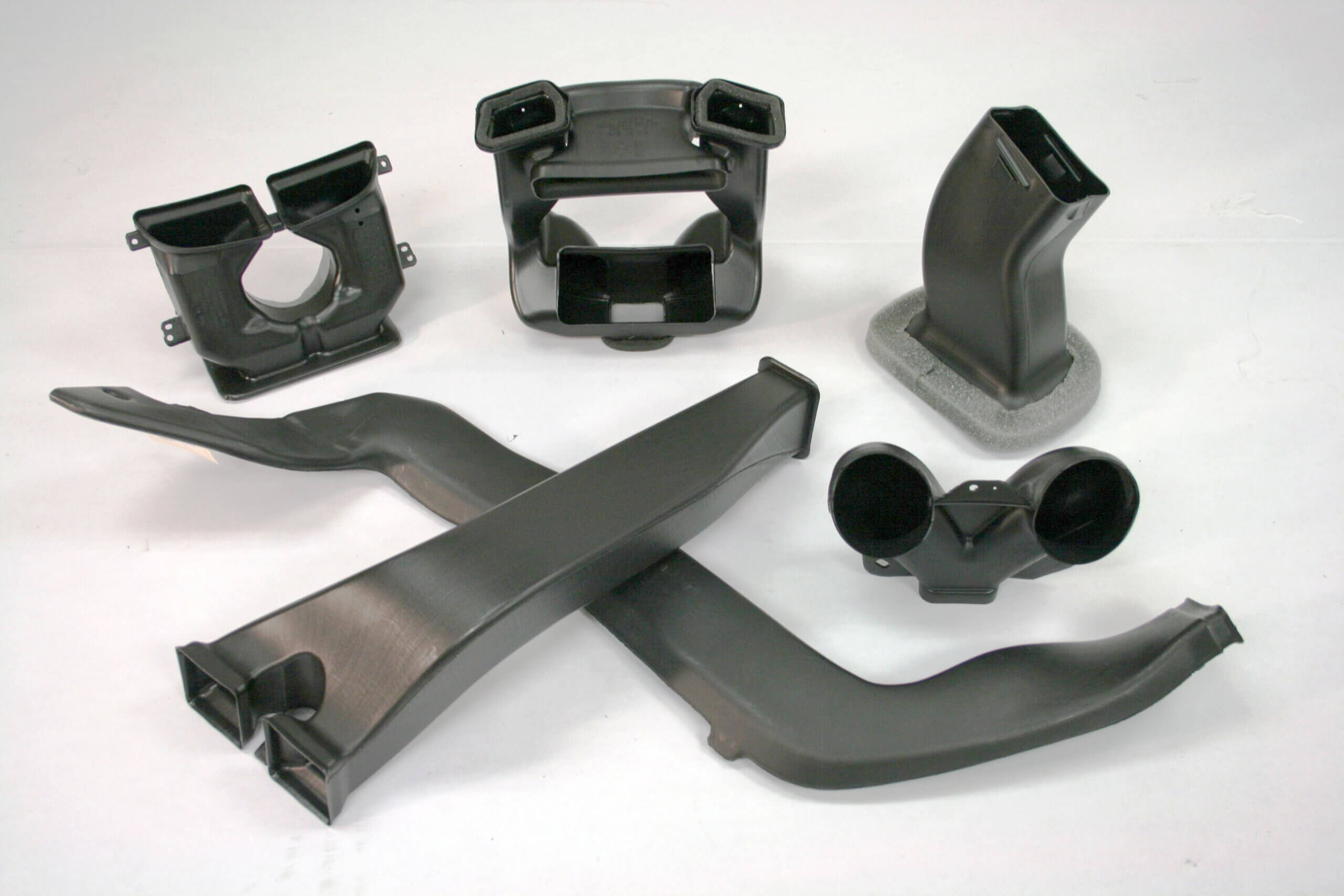
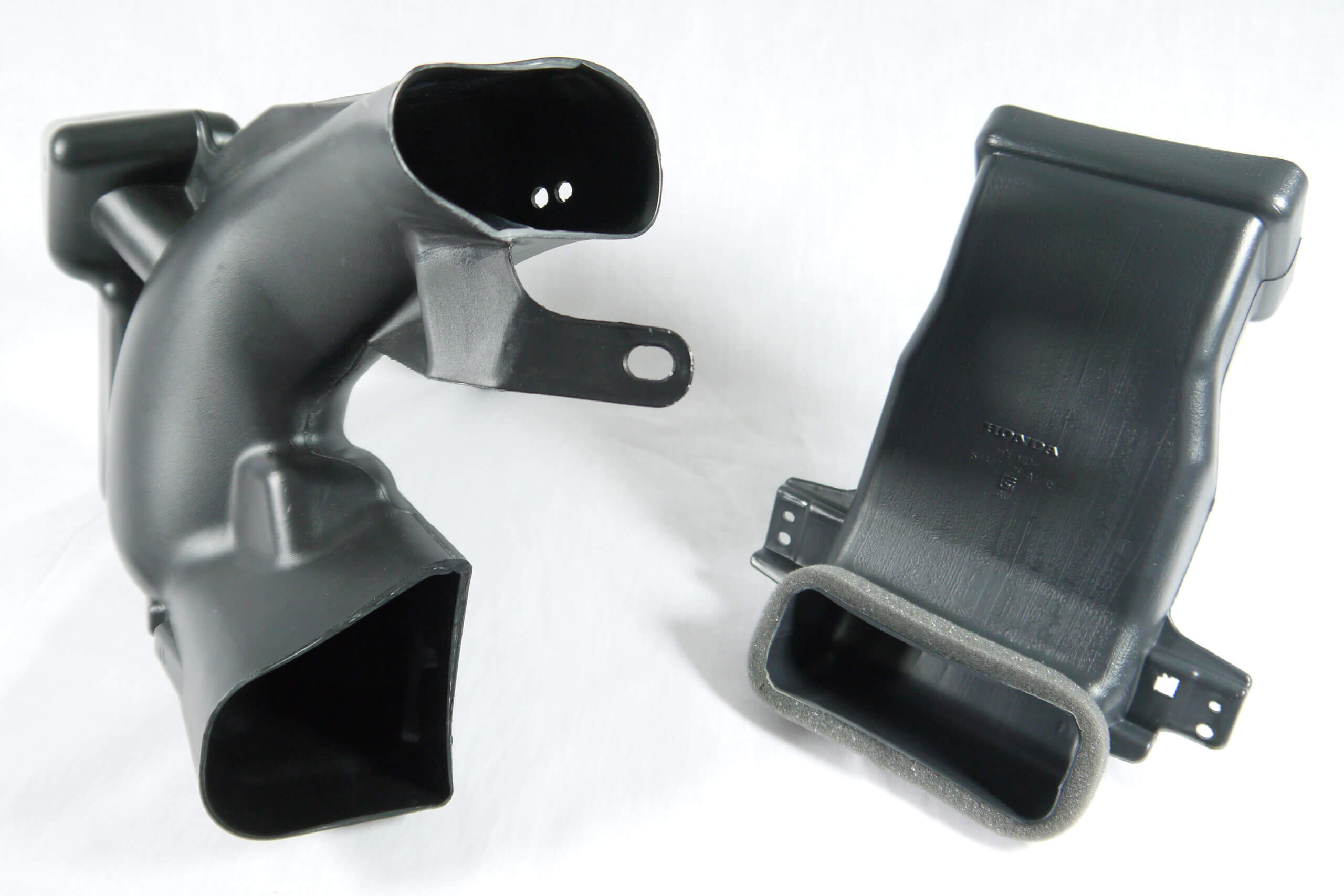
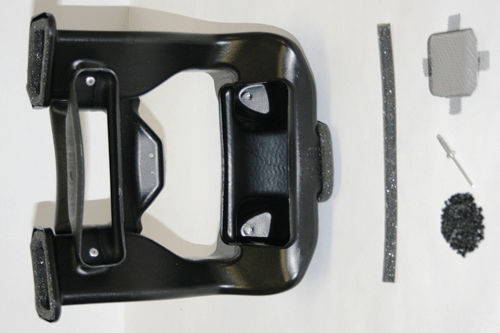
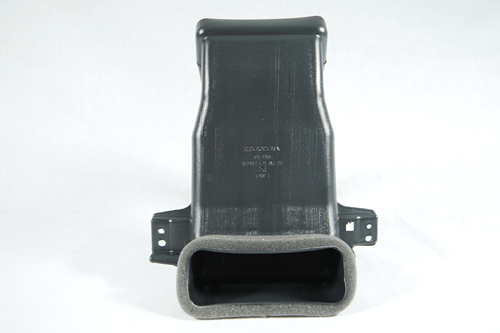
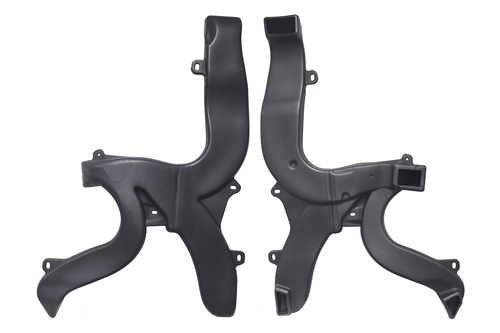
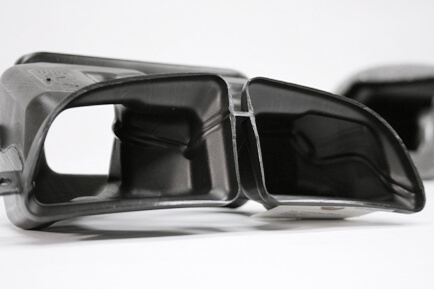
Optimizing Blow Molded HVAC Duct Design
To minimize wall thickness in the design phase, we use a blow molding process simulator throughout development to measure and optimize localized wall thickness. This bypasses the need for prototype tooling, cuts mold cost, reduces delivery time, and decreases product development time by up to 40%.
To achieve optimal wall thickness on the production line, we control the thickness of the blow-mold parison as it’s extruded, thus regulating the wall thickness as it forms in a mold cavity. This process results in an average 25% reduction in part weight, 10% reduction in cycle time, and 6-8 week reduction in new part debug time.
Do you want to take your blow molded HVAC component or assembly to the next level?
Send us your design to get started!
case study
HVAC “K-Duct”
Distinguished by a signature green and yellow color scheme, our customer is the world’s largest producer of agricultural machinery. They’re also a leading original equipment manufacturer (OEM) for machinery, heavy equipment, diesel engines, and drivetrains for the construction, forestry, and lawn care industries.
Wherever You’re Located, We’re Here to Help
17 strategic locations in North America to meet the needs of our diverse customer base.
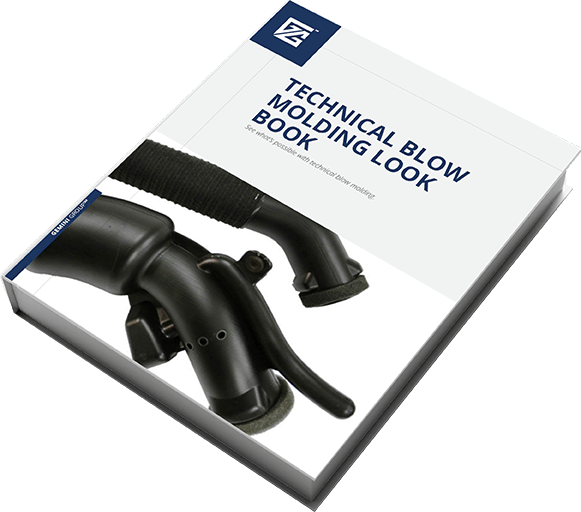
Technical Blow Molding Look Book
Rotomolding and blow molding both yield hollow plastic parts. So how do you decide which to choose?
Insights
Get to know us. Get in touch today.
We have the resources to meet any part or production challenge. Let’s talk about what that means for you.
"*" indicates required fields