Regency
BLOW MOLDED FUEL AND DEF TANKS
When it comes to sourcing high-quality blow molded fuel tanks and diesel exhaust fluid (DEF) tanks, our expertise leak testing and rollover valve (ROV) testing paired with our CARB and EPA certifications sets us apart.
Unmatched Expertise in Fuel Tank and DEF Tank Manufacturing
Why choose us over other plastic tank manufacturers? It’s quite simple – we know what it takes to produce a successful fuel tank that won’t end in field-failure.
We perform blow molding simulation on every part design to ensure optimal wall thickness, produce rapid prototypes to test functionality and integration, process advanced materials that can withstand harsh environments, and test every single tank for leaks and rollover valve (ROV) functionality.
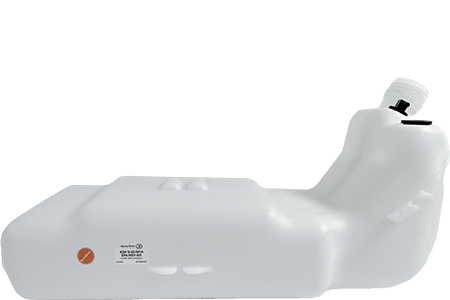
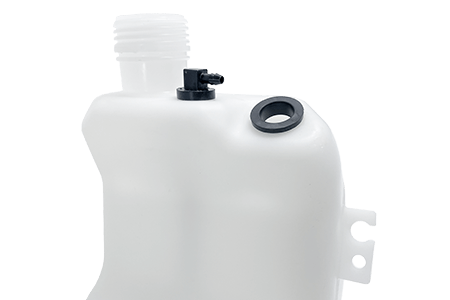
Reduce Field-Failure Liability
We perform strict rollover valve (ROV) and leak testing and apply serialized labels to each fuel tank with its unique test information, reducing our customers’ liability in the event of a field failure.
Reduce Development Costs
Through techniques such as blow molding simulation software and rapid prototyping with convertible tooling, we take the guesswork out of part design and reduce development costs.
Proficiency in Molding Durable Materials
We’re experts in molding highly durable and chemical-resistant materials that can withstand the corrosive nature of fuels while maintaining structural integrity.
Valve and Venting System Integration
We excel at seamlessly integrating valves and venting systems into our blow molded fuel tanks and DEF tanks, ensuring optimal performance, safety, and ease of use.
EPA and CARB Certified
We’re certified to produce fuel and DEF tanks that comply with stringent EPA and CARB environmental standards and emissions regulations.
In-House Secondary Operations
To further enhance functionality, we perform a variety of secondary operations in-house such as riveting, welding, and assembly, eliminating the need for third-party processing.
If you have an annual production volume of 3,000 parts or more, we should talk.
Whether you’re sourcing a new fuel or DEF tank supplier or simply updating your benchmark, you deserve an accurate and timely quote. We will deliver.
Superior Alternative to Steel
Plastic fuel tanks offer key advantages over traditional steel tanks due to their lightweight construction, resistance to corrosion and puncturing, and design flexibility. Many industries have embraced plastic fuel tanks due to the numerous benefits they provide.
- Improved Fuel Economy:
Plastic tanks are significantly lighter than metal, leading to improved fuel economy and vehicle performance. - More Design Flexibility:
Blow molding offers superior design flexibility, producing tanks that can conform to the available space in the vehicle, and can incorporate additional features like baffles, which help minimize fuel sloshing.
- Improved Durability:
Plastic tanks are less susceptible to denting or puncturing compared to steel tanks, enhancing their durability in case of impact. - Higher Corrosion Resistance:
Plastic fuel tanks exhibit superior corrosion resistance, eliminating the need for costly anti-corrosion coatings.
Superior Alternative to Rotomolding
Traditionally, rotomolding has been the choice manufacturing method for fuel and DEF tanks due to consistent IDs and ODs. But blow molding advancements now combine it with compression molding for better control of tolerances. Today, blow molding surpasses rotomolding for fuel and DEF tanks.
- Lighter Part Weight: Blow molded fuel tanks require less material than rotomolded ones without compromising strength and durability, resulting in increased fuel efficiency and improved overall performance.
- Improved Structural Integrity: Blow molding uses one solid parison resulting in parting line integrity while rotomolding uses melted material, creating voidsand defects in the tank wall, especially at the parting line and near inserts.
- Shorter Cycle Times and Lower Cost: Blow molding facilitates shorter cycle times and lower costs, particularly when the production volume exceeds 3,000 pieces.
- Reusability of De-Flash Material: By eliminating excess material through de-flashing, we not only reduce waste but also have the opportunity to recycle and reuse it in subsequent blow molding processes.
case study
Converting a Rotomolded DEF Tank to Blow Molding
Discover how blow molding helped a Tier 1 supplier of custom fluid management consolidated their supply chain, increase efficiency, and reduce costs while meeting all production and performance requirements.
Wherever You’re Located, We’re Here to Help
17 strategic locations in North America to meet the needs of our diverse customer base.
Insights
Get to know us. Get in touch today.
We have the resources to meet any part or production challenge. Let’s talk about what that means for you.
"*" indicates required fields