Regency
BLOW MOLDED FLUID RESERVOIRS
We understand the complexity of designing fluid reservoirs to seamlessly fit within existing systems. Let us help mitigate the risk of last minute design changes and deliver a quality part in time and on cost.
INTRICATE DESIGNS WITHOUT THE HEADACHE
Fluid reservoirs and tanks require complex geometries in order to fit between existing system components under hood. Oftentimes last minute engineering changes in the surrounding environment require a design change to the reservoir or tank.
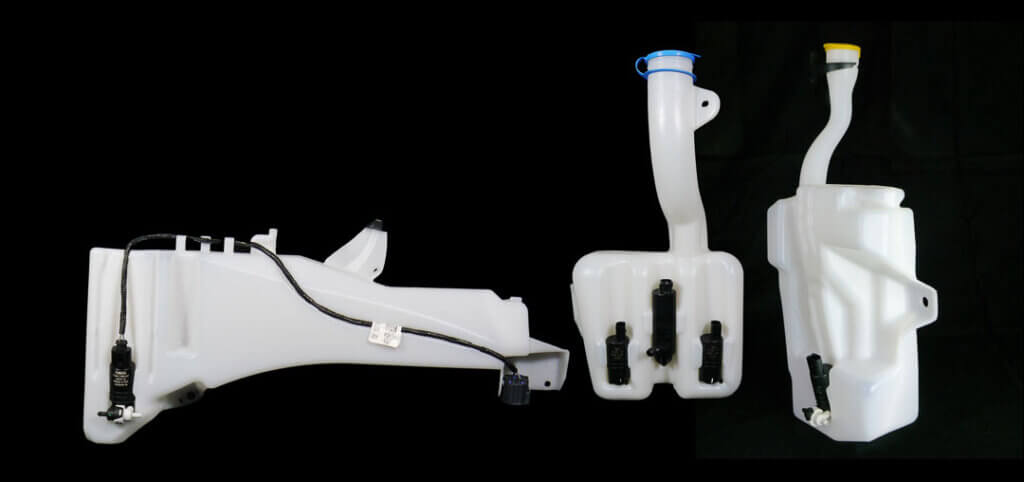
Working with a supplier who understands these nuances will help you mitigate risk and ensure the timely delivery of high-quality parts. That’s why OEM’s and Tier 1 automotive suppliers choose on us to assist with the development and refinement of their part designs.
Are you sourcing a custom fluid reservoir or simply looking to update your benchmark?
If your blow molded part has complex geometries or you spend north of $100,000 annually in blow molding, we should talk. Contact us today for an accurate and timely quote.
Optimizing Fluid Reservoir and Tank Design
Drawing from over three decades of experience and successful blow molded fluid reservoir programs, we can optimize your fluid reservoir and tank designs, providing cost-effective solutions without compromising on performance. We’ve have built efficiency and quality into every step of the engineering and manufacturing process.
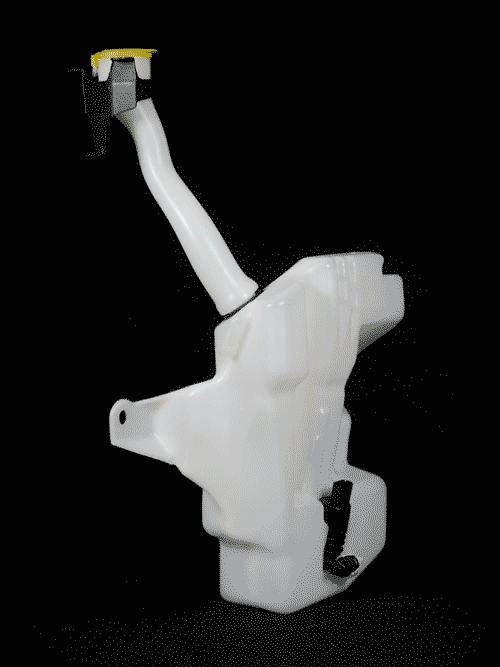

Our experience tells us that the best way to drive cost out is by optimizing part design so wall thickness can be minimized and secondary processes can be eliminated. This lowers the piece price by reducing weight, material costs, labor costs, and cycle times.
Here are the two most effective tactics we employ to achieve the optimal design:
1. Process Simulation
Using B-SIM, a cutting-edge blow molding simulation software, we identify potential issues and opportunities for improvement – during the design phase, well in advance of production. This helps minimize wall thickness while maintaining performance requirements and eliminates the need for prototyping and re-tooling.
2. Process Consolidation
Using insert molding, we can integrate molded ports, clips, and brackets into the part during the blow molding process, eliminating the need for secondary processes such as welding and manual assembly. Using core movements and side-actions, we can create features that would otherwise require machining such as drilling and cutting.
Additionally, by designing and constructing blow molding tooling in-house, we streamline the manufacturing timeline, offering better quality control and swift responses to engineering changes.
Partnering
for Success
If you are involved in or considering the development or production of any of the following, we should talk.
- Fluid Reservoir
- Windshield Washer Reservoir
- DEF Tank
- Radiator Surge Tank
- Coolant Surge Tank
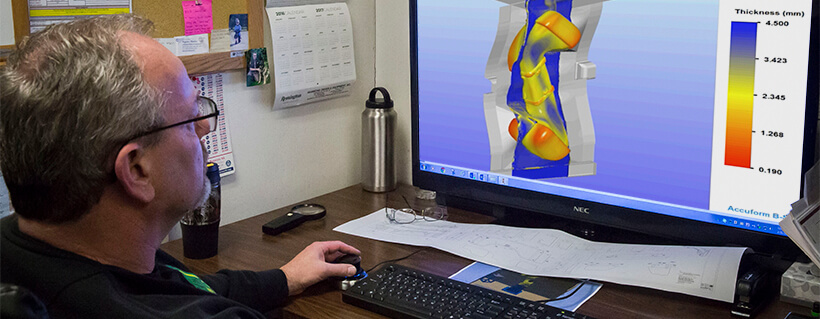
Our engineering expertise can optimize your part’s performance while reducing costs. By collaborating with us, you gain access to a team committed to excellence, efficiency, and high-quality results.
case study
Overcoming Engineering Challenges for a High-Performance Washer Fluid Tank
Discover how our expertise in washer bottle design, molding, and tooling helped a Tier 1 Automotive supplier overcome tight packaging constraints, geometrical restrictions, and engineering changes to successfully develop a leak-proof washer fluid tank.
Wherever You’re Located, We’re Here to Help
17 strategic locations in North America to meet the needs of our diverse customer base.
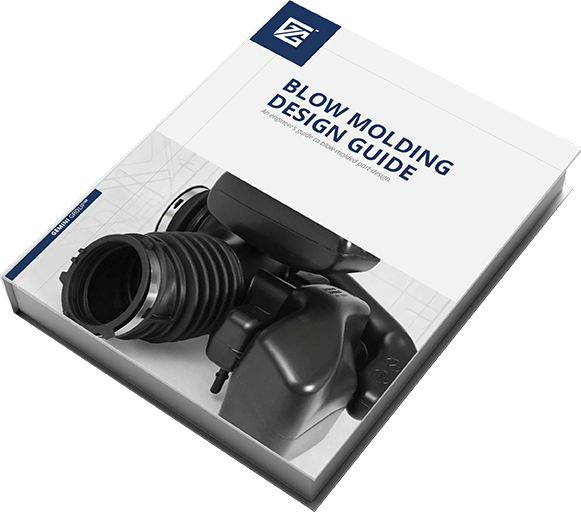
BLOW MOLDING DESIGN GUIDE
Are you new to blow molding and don’t know where to start with your part design? Then our Blow Molding Design Guide is for you! Created by engineers, for engineers, this guide is the ultimate starting point to kick off a successful product design for the blow molding process.
Insights
Get to know us. Get in touch today.
We have the resources to meet any part or production challenge. Let’s talk about what that means for you.
"*" indicates required fields