Regency
BLOW-MOLDED AIR INTAKE ASSEMBLIES
The biggest challenge in designing and manufacturing air intake assemblies is that no two systems are exactly the same. What works for one won’t work for another. But fear not! We have the experience and technology to turn that challenge into a victory for you and your program.
Blow-Molded Air Intake Components
The whole is greater than the sum of its parts until one of those parts fails. That’s why it’s so important to scrutinize each component not only on its own but also as to how it fits into the overall air intake system. That’s what you get when you work with us.
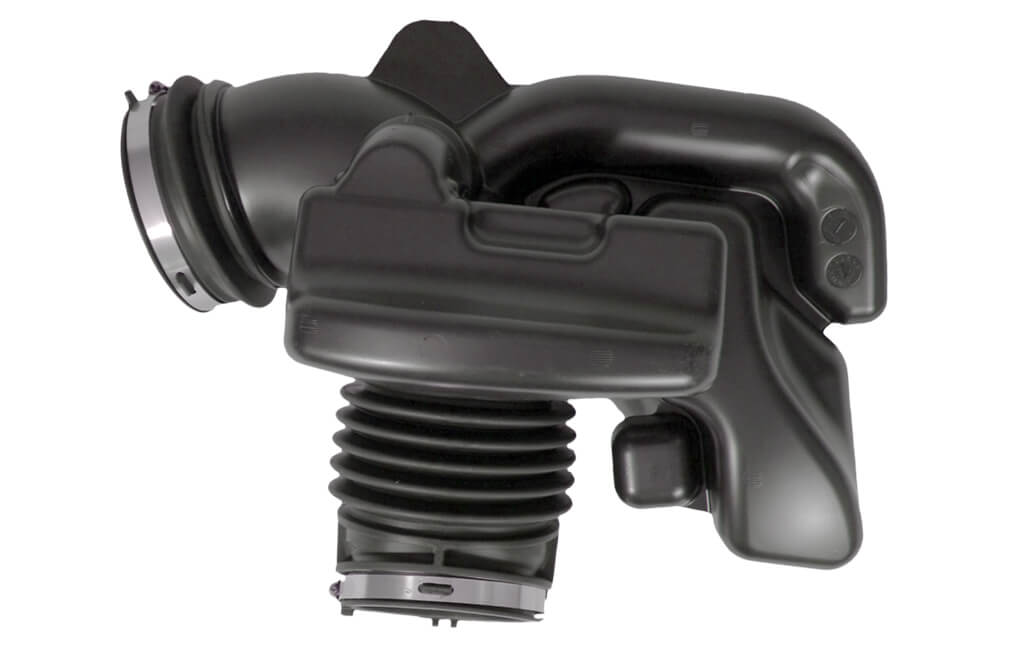
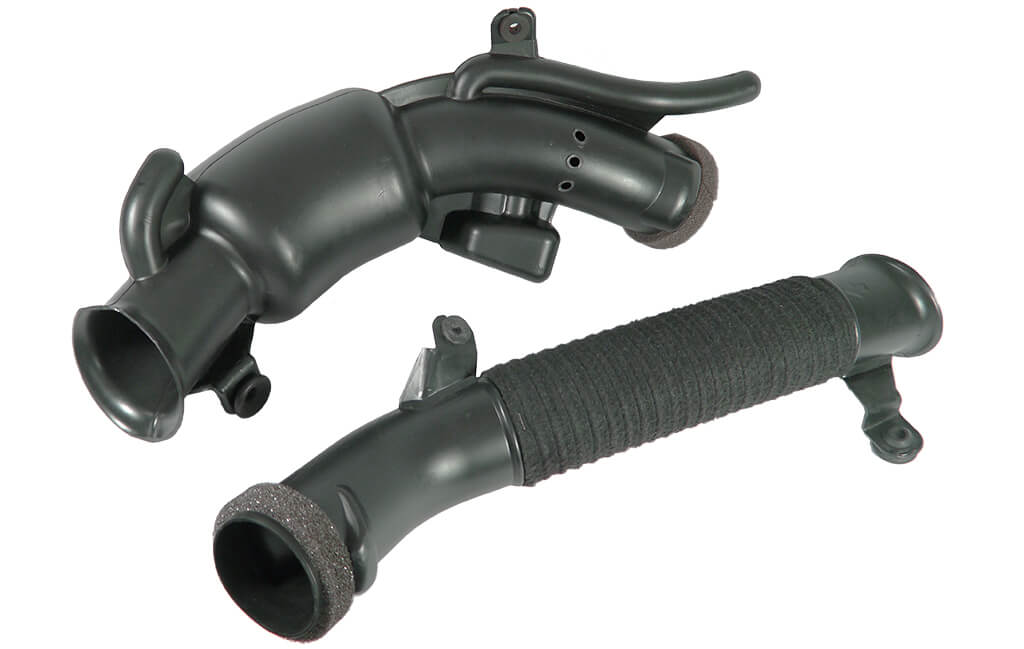
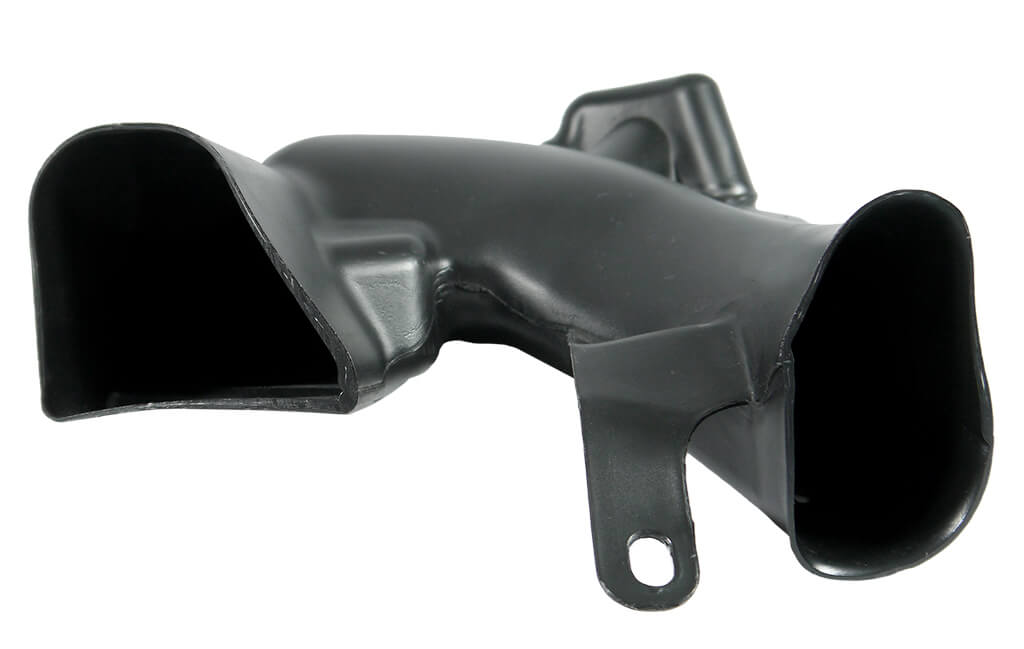
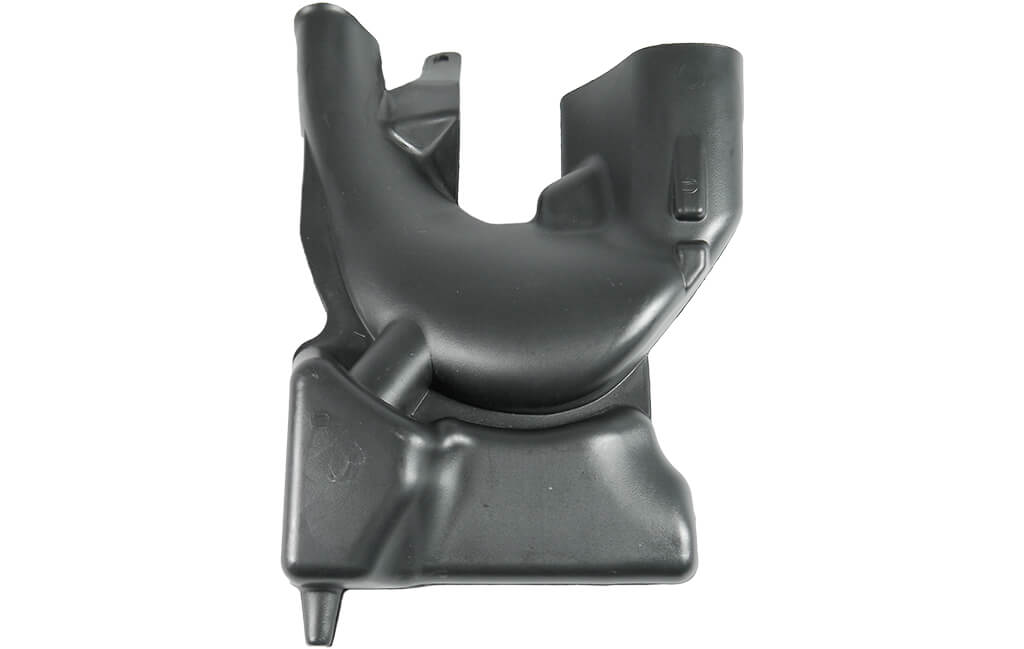
We have a proven track record in engineering and manufacturing a full range of blow-molded air intake components, including the following:
Clean Air Ducts & Assemblies
Resonators & Tuners
Dirty Air Ducts
Injection Molded Bellows, Cuffs, and Ports
By using our expertise and cutting-edge technology available to you, you can take your design to the next level.
From material selection to DFM/DFA, from prototyping to production, we’re here to help you succeed. So what are you waiting for? Give us call. Shoot us an email. Put us to work for you!
Controlling Costs
We have some pretty high expectations for air intake systems. We expect them to be sleek, to meet demanding functional requirements, to be light weight and strong, to come in at or under budget, and for all components to fit perfectly together while seamlessly conforming into the empty space in its surrounding environment…
…which sounds like a job description in engineering.
Truly, if you want a successful program launch on time and within budget, it’s critical to choose a supplier that knows what you’re up against. One that can help you navigate the nuances of each component. One that can offer suggestions to enhance your design for manufacturing and assembly. One that can help minimize costly tooling changes. One like us.
We aren’t a build-to-print blow molder. We understand the complexity of an air intake assembly and can provide strategies to drive cost out. We’ve invested heavily in the technology and equipment our customers need to meet their cost and quality targets:
- The insert molding process can be used to incorporate fasteners and/or other inserts directly into the mold without the costs associated with secondary operations.
- Extensive in-process testing and leak testing prevents virtually all defective parts from ever leaving our facility.
- Underestimating high-volume logistical needs
- Lack of certifications and processes for quality control
- Blow-molding simulation software helps identify potential problem areas before any tooling is built.
- In-house tooling design and build allows better cost control, reduced lead times, and quick turnarounds on engineering and design changes.
case study
Air Intake Assembly
The customer is a Tier I supplier to automotive OEMs, specializing in air induction systems. While the customer is an expert in air filtration and air boxes, they rely on Tier II suppliers for other system components such as clean and dirty air ducts.
Wherever You’re Located, We’re Here to Help
17 strategic locations in North America to meet the needs of our diverse customer base.
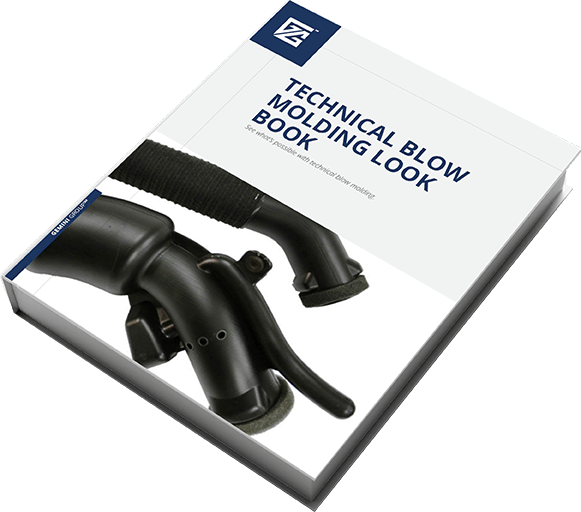
Technical Blow Molding Look Book
Rotomolding and blow molding both yield hollow plastic parts. So how do you decide which to choose?
Insights
Get to know us. Get in touch today.
We have the resources to meet any part or production challenge. Let’s talk about what that means for you.
"*" indicates required fields