GPI, GT Plastics, Sierra, GPM
PLASTIC EXTRUSIONS FOR SEATING APPLICATIONS
Two out of every three automotive seats produced in North America utilize our plastic profile extrusions. With over 7,000 profiles under our belt, we take the headache out of designing from scratch.
PRODUCTS
We offer a wide range of plastic extrusions specifically designed for seating applications. Though you may have never seen them, chances are you’re literally leaning on them every day; our seating extrusions are in nearly 70% of vehicles on the road today!
Trim Retainers
Our trim retainers primarily serve as clip-and-lock systems to securely fasten seat covers onto the seat frame and define the trim line. These versatile extrusions can be punched, lasered and printed in-line, as well bonded to non-woven fleece.
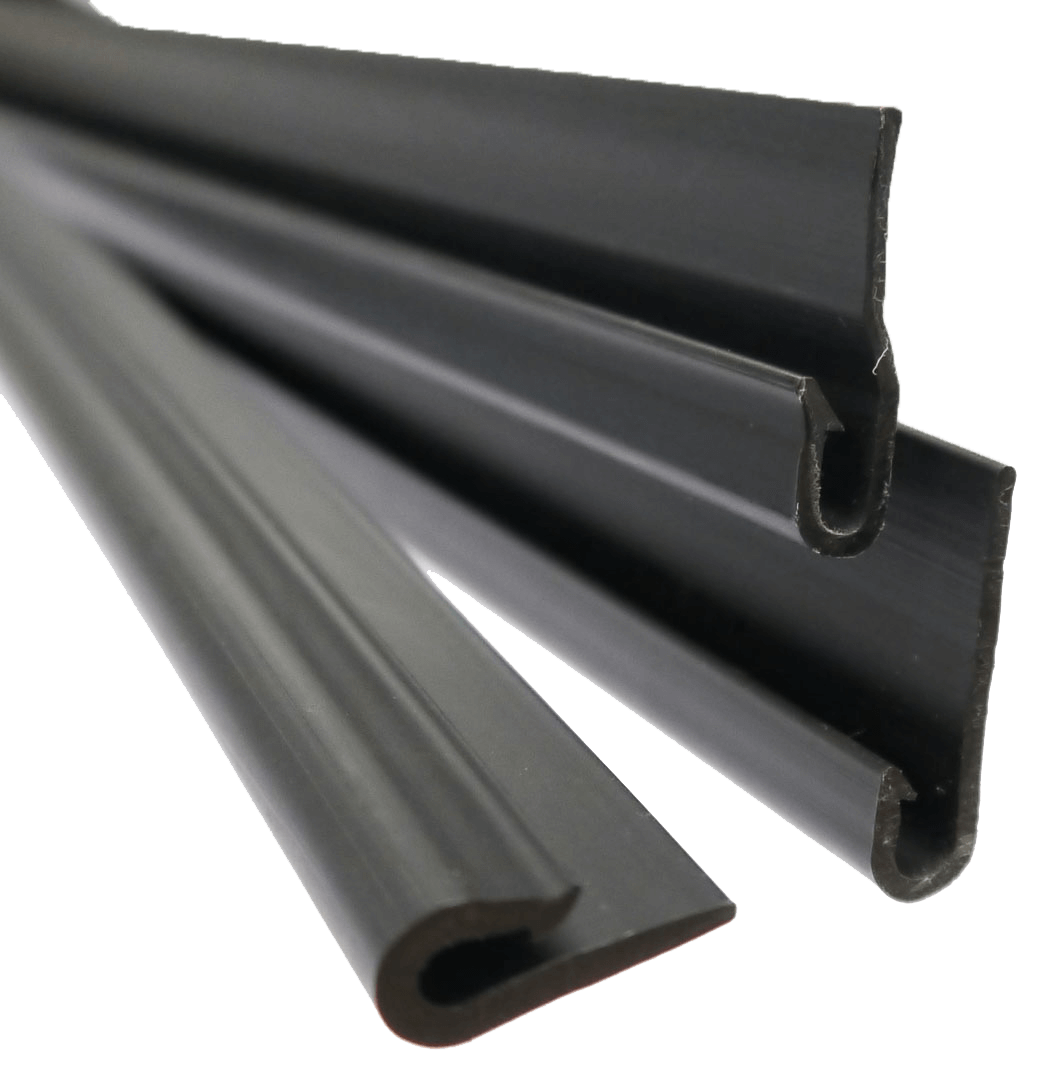
J-Retainers
The J-retainer stands as the timeless seating retainer. With its fish hook shape, this profile easily locks into position and can clip directly onto metal wire. It’s an ideal profile for bonding with non-woven fleece.
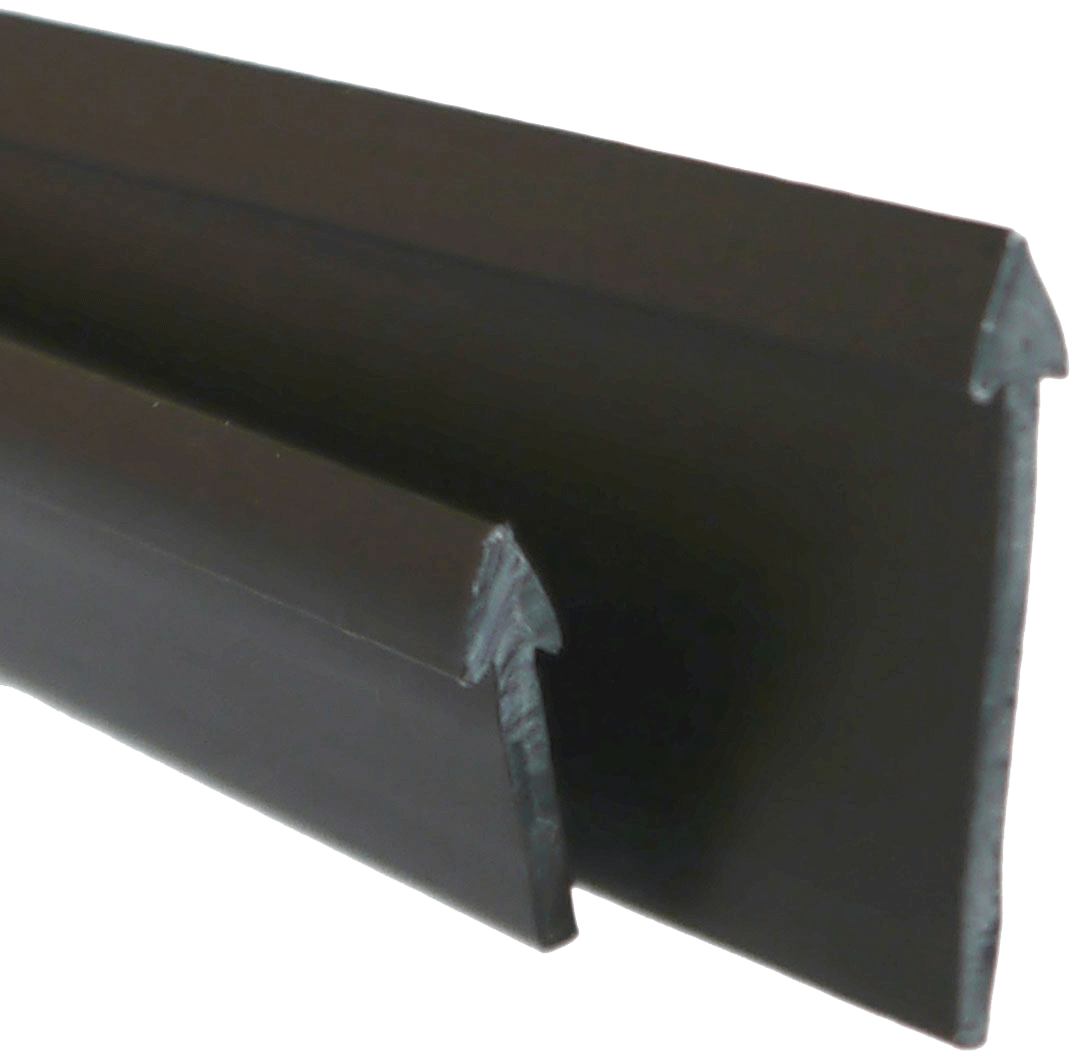
Arrow Retainers
Our arrow retainers come in a variety of variations and can be tailored to match your unique seat trim channel requirements. They offer flexibility without compromising on strength and performance.
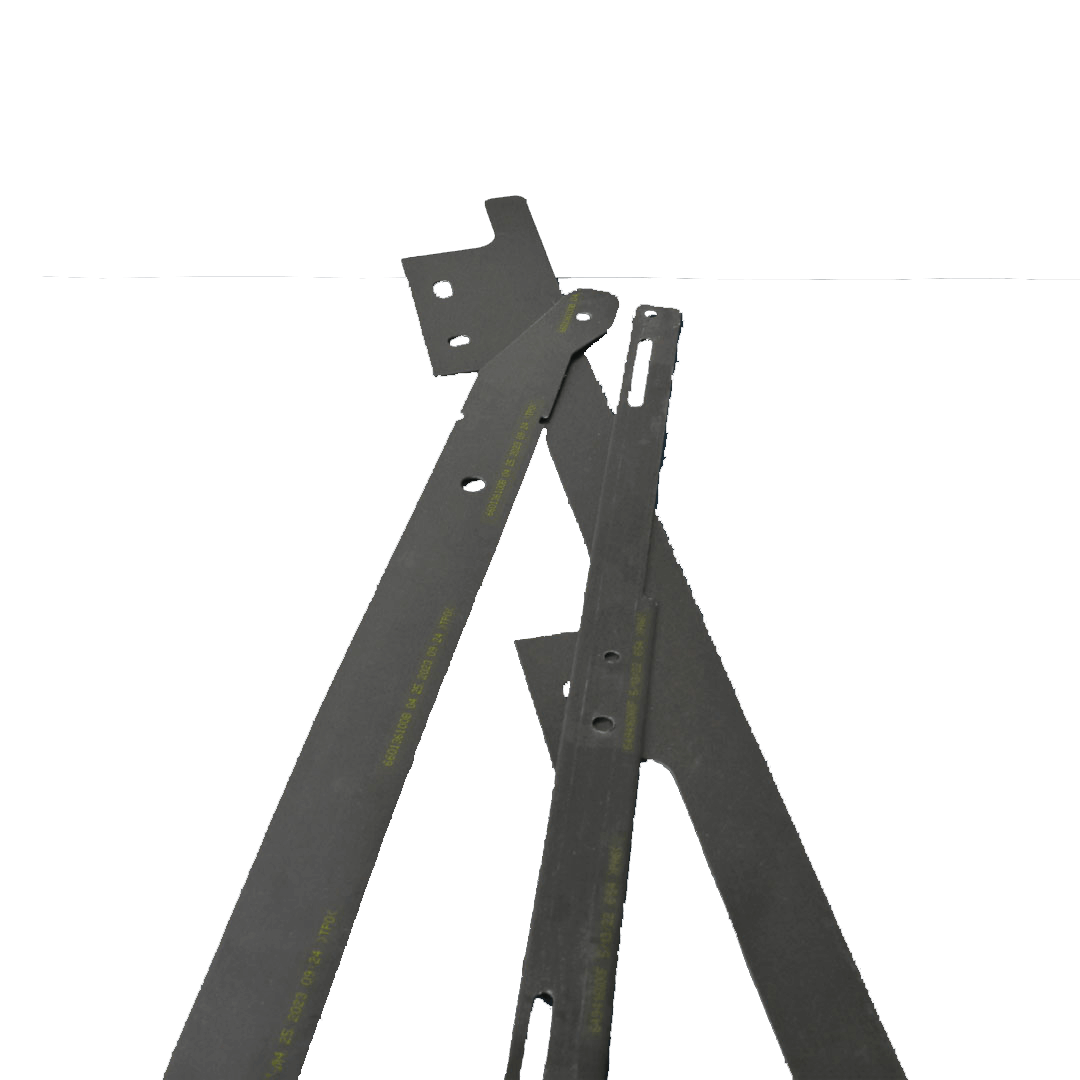
Stiffeners
Our stiffeners, also known as flat strips, are engineered to enhance the structural integrity of seating components while emphasizing seating contours. They ensure longevity and stability in seating applications.
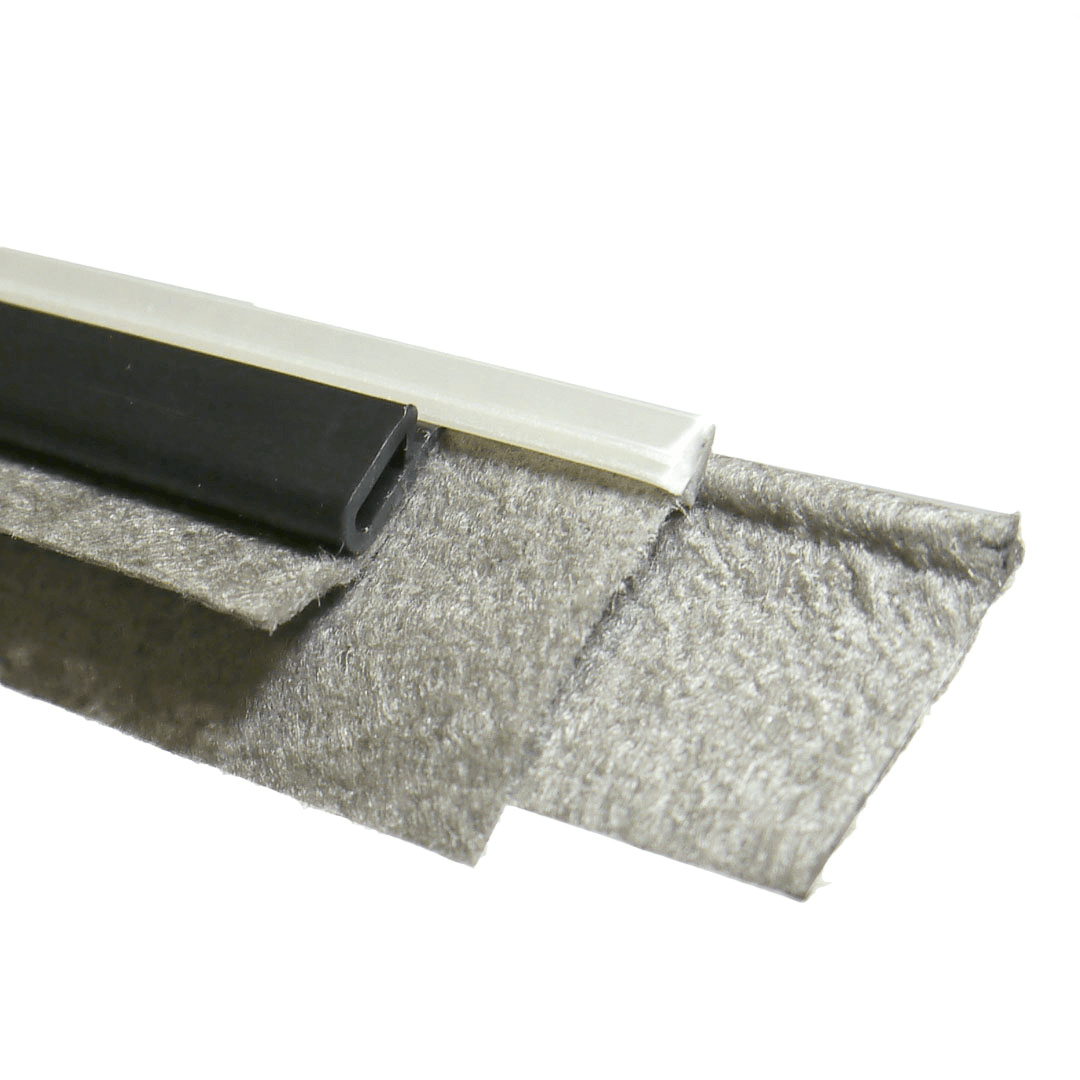
Beaded Duon / Tie-Downs
Our beaded duon extrusions are widely used as tie-downs to fasten seat covers to the foam-wire frame, creating beautiful contours while reducing sewing operations and accelerating assembly times for our customers.
ADVANTAGES
Our plastic seating extrusions offer numerous advantages that set our products apart:
Decrease warranty claims
Our extrusions are designed to enhance the overall quality and durability of seating components, reducing the likelihood of warranty claims and associated costs.
Lower cost than zippers
Compared to traditional zipper systems, plastic extrusions offer a more cost-effective solution without compromising on functionality or performance.
Cut to length
Our extrusions can be easily customized to meet your specific requirements, ensuring a perfect fit for your seating applications.
Ease of installation
With user-friendly designs and precise engineering, our extrusions simplify the installation process, reducing the risk of error and accelerating assembly time for our customers.
High production rates
Our plastic extrusion processes enable high-speed production, ensuring efficient and timely delivery to our customers.
Low-cost tooling
We understand the importance of cost-efficiency. That’s why we offer low-cost tooling options, allowing you to achieve your desired seating solutions without breaking the bank.
Short tooling lead times
We build nearly all prototype and production tooling in-house, resulting in shorter lead times and ensuring quick turnaround for your projects.
Material flexibility
Our expertise in PP, LDPE, ABS, and over 50 specialty resins gives you the flexibility to choose the best option for your seating applications.
Disadvantages
While our plastic seating extrusions offer several advantages, it’s important to consider a few limitations:
Surface standards
Depending on the material used, the surface area of our extrusions may not meet class-A surface standards. However, our team is dedicated to delivering high-quality finishes that meet industry standards.
Tolerances
Compared to injection molding, plastic extrusions may have slightly larger tolerances. Our engineers work diligently to minimize these variances and ensure precise fit and function.
Third dimensions
In certain cases, achieving complex three-dimensional shapes may require additional secondary operations. Our team is equipped to handle these requirements efficiently and effectively.
WHY CHOOSE US?
We’re committed to providing exceptional plastic extrusions for seating applications. Our dedication to quality, innovation, and customer satisfaction sets us apart in the industry.
Wherever You’re Located, We’re Here to Help
17 strategic locations in North America to meet the needs of our diverse customer base.
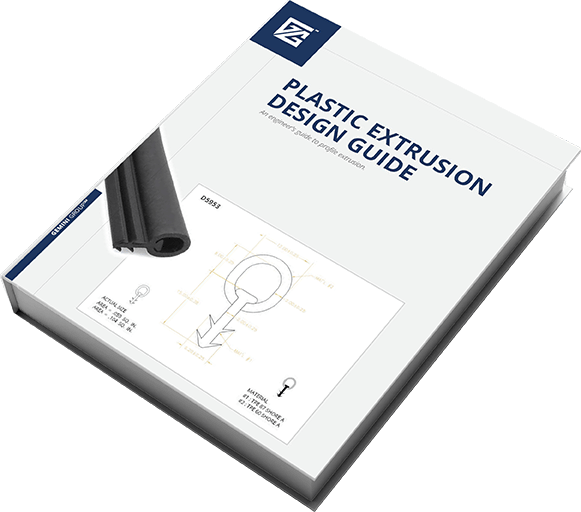
PLASTIC EXTRUSION DESIGN GUIDE
Is your extrusion design optimized to meet the constraints of the extrusion process? This free guide offers a solid foundation in the requirements for successful extrusion design. Created by engineers for engineers, and based on decades of extrusion development and manufacturing experience.
Insights
Get to know us. Get in touch today.
We have the resources to meet any part or production challenge. Let’s talk about what that means for you.
"*" indicates required fields