GPI, GT Plastics, Sierra, GPM
PLASTIC EXTRUSIONS FOR SAFETY APPLICATIONS
When your customer relies on your product to save their life in the event of an accident, you need to have confidence that every component performs under the most extreme conditions. Our extrusions undergo air bag deployment testing to ensure performance at temperatures as low as -40° Celsius.
AIR BAG APPLICATIONS
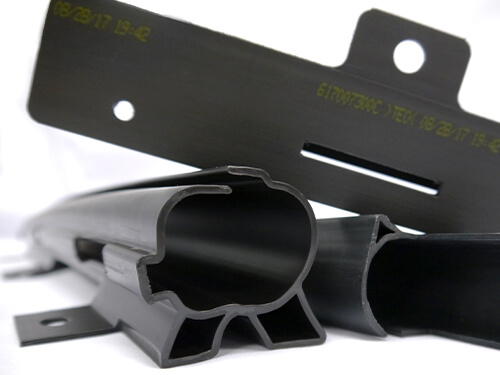
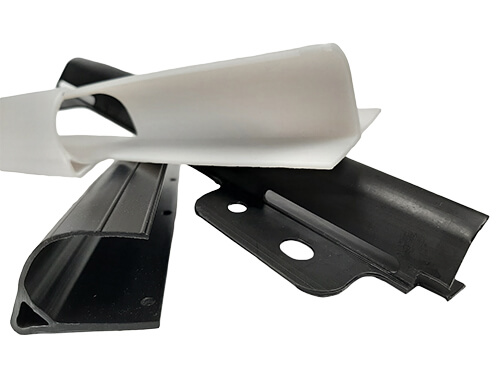
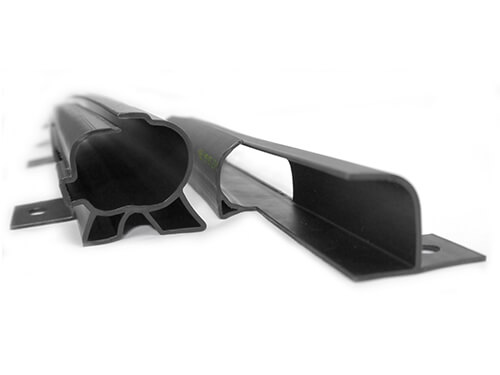
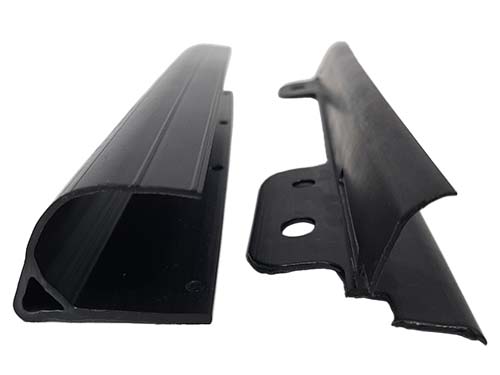
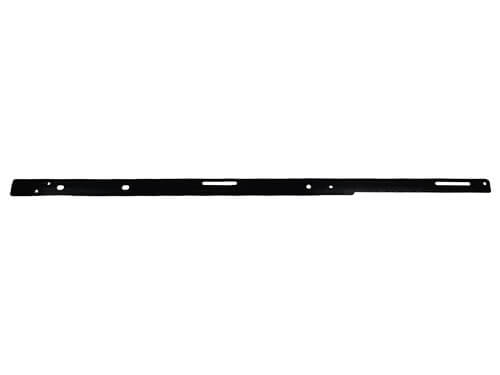
Whether you need a pillar, ramp, housing, or shape maintainer for a safety-related application, you can rely on us to deliver the most innovative and reliable solutions available in the marketplace. Our engineers will help optimize your design and material, ensuring it meets the highest standards of integrity and reliability.
PILLARS/RAMPS/HOUSINGS
Our extrusions for pillars, ramps, and housings ensure the protection of your compact air bag in storage and proper direction of deployment. They’re designed to be lightweight, yet strong enough to withstand high impact forces.
SHAPE MAINTAINERS/
ANTI-TWIST STRAPS
Shape maintainers, or anti-twist straps, are used to secure air bags in place and prevent unwanted rotation during deployment. Our plastic extrusions for anti-twist straps are designed to provide secure attachment and stability.
AIR BAG Materials
TPO
Commonly used for air bag pillars, ramps, and housings, TPO is a durable and flexible material that offers excellent impact resistance, weatherability, and has a high strength-to-weight ratio.
PA-6, TPO, PP
Commonly used for anti-twist straps and shape maintainers, PA-6, TPO, and PP provide excellent strength, flexibility, and resistance to deformation, ensuring secure attachment and stability of air bags.
AIR BAG FEATURES
COMPLEX PROFILES
Our plastic extrusions can have complex profiles, allowing for precise fit and integration within the air bag system.
TEAR SEAMS
We can engineer tear seams into your extruded air bag component facilitate controlled deployment.
LIVING HINGES
Our living hinges provide flexibility and allow for repeated opening and closing of air bag compartments during maintenance or inspections.
FLEXIBLE FLAPS
We protect air bag openings from dirt, dust, and other contaminants with flexible flaps that seal out environmental hazards.
PUSH PINS
We can integrate push pins to secure our extrusions in place within the air bag system, providing quick and easy installation and ensuring proper positioning.
TAPE
Tape can be applied for additional adhesion and sealing, enhancing the overall performance and reliability of your air bag system.
PRINTING
Our in-line printing capabilities allow for the inclusion of important information directly on the extrusion for easy identification and reference.
Seat belt APPLICATIONS
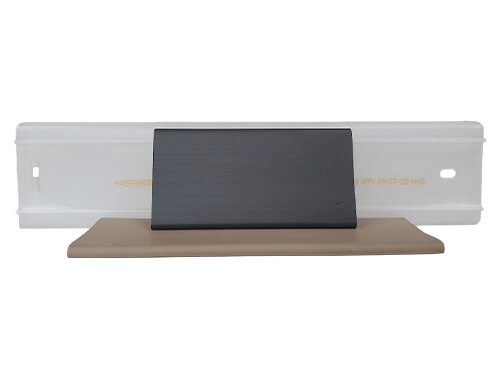
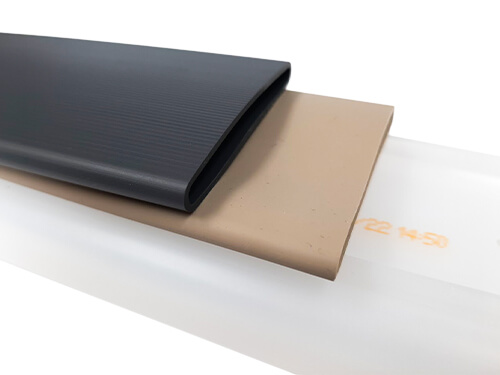
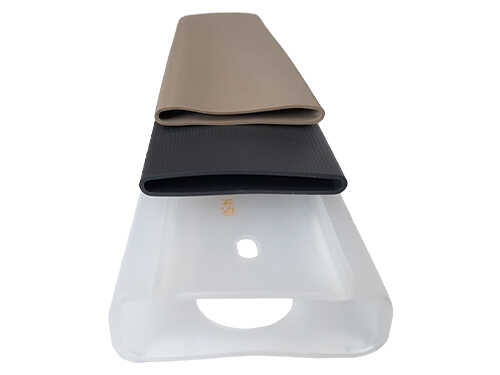
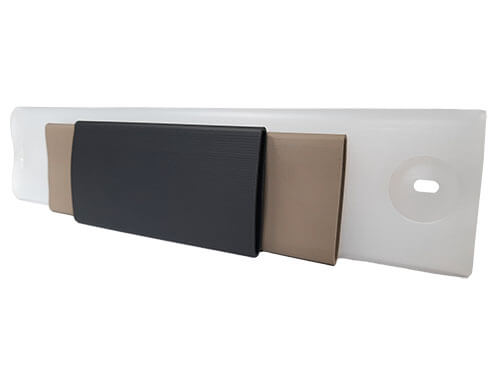
SLEEVES
Seat belt sleeves are used to cover and protect seat belt components, ensuring smooth operation and preventing wear and tear. Our plastic extrusions for sleeves provide durability and reliable performance.
BOOTS
Seat belt boots are used to cover the joint areas of seat belt mechanisms, protecting them from dust, debris, and other external elements. Our plastic extrusions for boots offer excellent sealing properties and ensure long-lasting performance.
SEAT BELT Materials
TPV
TPVs are a type of elastomer that combines the properties of rubber and plastic. TPV materials are often used for seat belt components due to their excellent weather resistance and flexibility.
PVC
PVC is a commonly used material for both boots and sleeves. It offers excellent flexibility, durability, and resistance to impact.
TPO
TPO is a versatile material that combines the properties of PP and EPDM rubber. It’s often used for seat belt components due to its excellent impact resistance, weatherability, and cost-effectiveness.
PP
PP is a lightweight and rigid material that offers excellent strength and chemical resistance. PP is commonly used for seat belt components, providing reliable performance and long-term durability.
LDPE
LDPE is a lightweight and flexible material with good chemical resistance and low moisture absorption, ensuring the longevity and performance of seat belt systems.
SEAT BELT FEATURES
HOLLOW OR SPLIT
Seat belt boots and sleeves can be designed with hollow or split profiles, allowing for ease of installation and maintenance.
CLASS-A SURFACES
Our plastic extrusions for seat belt components can achieve Class-A surfaces, ensuring a visually appealing and consistent appearance.
TEXTURED SURFACES
Textured surfaces can be incorporated into our seat belt extrusions to provide enhanced grip and tactile feedback, improving user comfort and safety.
COLOR-MATCH
Our plastic extrusions can be color-matched to meet specific design requirements, allowing for seamless integration with the overall seat belt system and vehicle interior.
WHY CHOOSE US?
With years of experience and a commitment to quality and reliability, we are a trusted partner and industry leader in plastic extrusions for safety applications.
SUPERIOR EXPERTISE
in designing and manufacturing plastic extrusions for safety products.
ADVANCED MATERIALS
and manufacturing processes to ensure durability and reliability.
RAPID PROTOTYPING
capabilities for fast iteration and efficient development.
CUSTOMIZED SOLUTIONS
tailored to meet your specific requirements.
EXCEPTIONAL CUSTOMER SERVICE
and support throughout the entire process.
Wherever You’re Located, We’re Here to Help
17 strategic locations in North America to meet the needs of our diverse customer base.
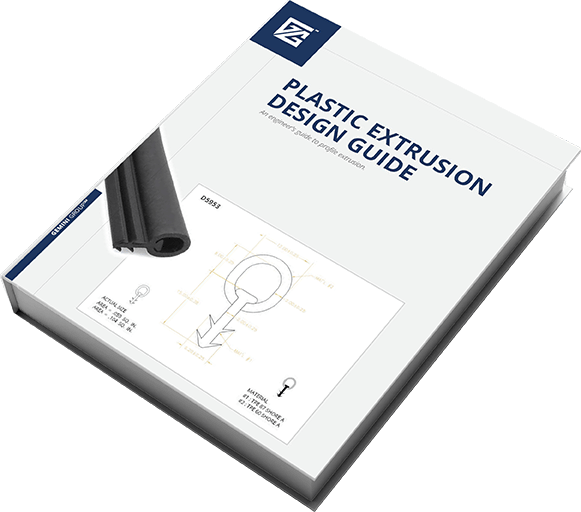
PLASTIC EXTRUSION DESIGN GUIDE
Is your extrusion design optimized to meet the constraints of the extrusion process? This free guide offers a solid foundation in the requirements for successful extrusion design. Created by engineers for engineers, and based on decades of extrusion development and manufacturing experience.
Insights
Get to know us. Get in touch today.
We have the resources to meet any part or production challenge. Let’s talk about what that means for you.
"*" indicates required fields