GPI, GT Plastics, Sierra, GPM
PLASTIC PROFILE EXTRUSION AND CO-EXTRUSION FOR THE MOST DEMANDING APPLICATIONS
Complex and highly functional plastic profiles are no match for our extrusion specialists. We have decades of experience with specialty materials, enabling us to produce parts with advanced material properties and intricate geometries that meet the most demanding functional and aesthetic requirements.
YOUR SINGLE SOURCE FOR EVERY PLASTIC PROFILE EXTRUSION NEED
From design and prototyping to extruding and finishing, we have complete in-house capabilities for your extrusion needs.
IN-HOUSE TOOLING
From prototype to production, we design and build all extrusion, fabrication, and quality assurance tooling in-house. Having complete control over the entire process ensures superior quality and reduces tooling costs and lead times for customers.
MATERIAL EXPERTISE
We take the headache out of choosing the best material for your plastic profile extrusion. We work with virtually all materials and specialize in hard-to-process materials, enabling us to run single or multi-durometer, color match, and produce Class A surfaces.
RAPID PROTOTYPING
Will your extruded part meet your requirements? Our rapid prototyping capabilities help reduce risk and optimize your profile design before any production tooling is ever built. Better yet, we do it in record time with in-house tooling design and build.
IN-LINE PROCESSING & AUTOMATION
In-line processing allows us to achieve third dimensions and further enhance the functionality and aesthetics of extruded profiles. This, along with our heavy investment in automation, helps lowers costs, improve repeatability, and reduce lead times for customers.
CO-EXTRUSION CAPABLE
By extruding multiple materials at once, co-extrusion allows us to create profiles with diverse properties, such as rigid and flexible components or two colors. This technique can eliminate the need for assembly, enhance functionality and aesthetics, and offers greater design flexibility to customers.
MARKET LEADER
With decades of experience and massive production capabilities, our extrusions are everywhere, including 70% of North American automobiles. In fact, we’ve helped develop over 7,000 profiles. If one of our existing profiles won’t work for you, we’re more than capable of making one that does.
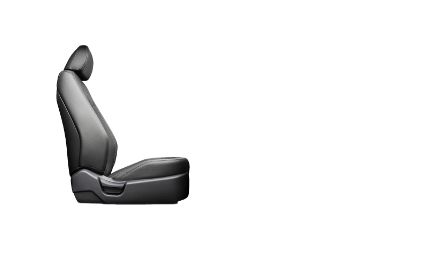
APPLICATIONS
From seals to seating, safety to structural, and so much more, our innovative plastic extrusions are found in more than a dozen industries, including automotive, building and construction, and agriculture. If you can dream it, we can make it.
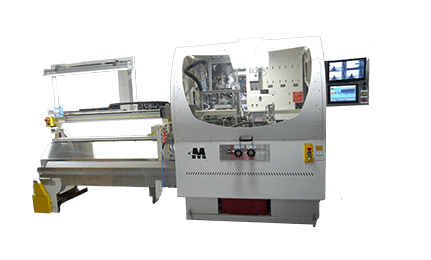
MANUFACTURING CAPABILITIES
From concept to production, we have the manufacturing capabilities to keep it in-house. This includes the design and build of all tooling, prototype and production processing, and all secondary operations. Our control over the entire process helps reduce costs and lead times for customers.
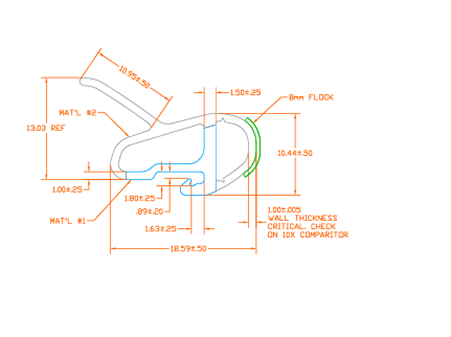
DESIGN & ENGINEERING
We’re not just a manufacturer, we’re a partner in engineering. We take a DFMA approach to simplify and re-engineer extrusion profiles with a focus on driving cost out and improving lead times, all while maintaining or improving the form, fit, and function of your part.
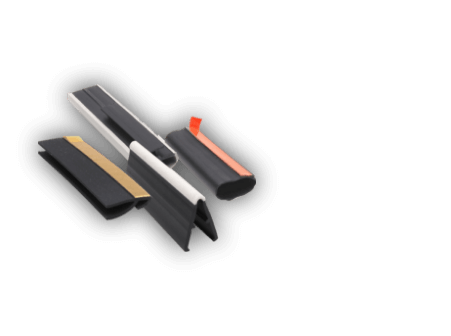
MATERIALS
Extensive thermoplastic extrusion experience helps us make material recommendations that ensure optimum performance at the lowest cost. We’re experts at extruding a variety of materials, especially those that are difficult to process.
PROVEN PLASTIC PROFILE EXTRUSION LEADERSHIP
With more than 7,000 plastic extrusion profiles developed, we have the experience to achieve the right profile for your application.
Our designers and engineers are specialists in creating complex extrusion designs; we work with virtually all materials and offer advanced profile features such as hollows, living hinges, and dual and multi-durometer composites.
You save time and money because we design and build all tooling and perform all secondary operations in-house.
Frequently Asked Questions
General FAQs
Who do you work with?
We typically work with large customers such as OEMs and Tier 1 suppliers. The majority of our accounts require at least 10,000 parts annually and have an annual buy north of $100,000. If this sounds like you, we should connect. Drop us a note online, give us a call at (248) 435-7271, or shoot us an email at plasticsales@geminigroup.net.
How do I contact you? Where are you located?
Gemini Group has four profile extrusion companies: GPI, GT Plastics, Sierra Plastics, and GPM. GPI is located in Ubly, Michigan; GT Plastics in Oscoda, Michigan; Sierra Plastics in El Paso, Texas; and GPM in Saltillo, Mexico. Please visit our Locations page for location details and contact information.
What are your capabilities?
65 extrusion & co-extrusion lines
- Hollow profiles, living hinges
- Dual and multi-durometer
- Two or more colors
Secondary operations
- Insert and overmolding (corners and sections)
- Thermal bending
- Welding (ultrasonic, hot plate)
- Lamination
- Assembly
- CNC routering
In-line processing and fabrication
- Wire and metal carrier reinforcement
- Tape (PSA, foam-backed)
- Slipcoat application, including silicone
- Flock application
- Graining
- Inkjet printing
Advanced testing laboratory
- Tensile/elongation testing
- Flowability
- Hardness (rockwell)
- Cold impact
- Component-level validation
- CMM
- Dimensionals
In-house tooling design and build
- Extrusion and co-extrusion dies
- Trim/fabrication tooling
- Assembly fixtures
- Quality gauges
Rapid prototyping
- FEA
- Process simulation
- 3D printing
- Dedicated prototyping lines
What certifications do you have?
Gemini Group has four profile extrusion companies: GPI, Sierra Plastics, and GPM. GPI and Sierra Plastics are ISO 14001:2004, ISO/TS 16949:2009, and WBENC certified. GPM is ISO/TS 16949:2009. You can view our certifications here.
What materials do you work with?
We work with a variety of multi-durometer plastic-rubber blends, including:
- TPV
- TPR
- T TPO
- TPE
- TPU
- 50+ engineered resins!
For a complete list, please visit our Materials page. If you need help choosing the best material for your unique application, we can help! Contact us online or learn more about material selection in The Engineer’s’ Guide to Selecting an Extruded Seal Material.
How do I design an extrusion profile?
We’d be remiss to provide an answer without understanding the scope of your challenge. That’s why we've developed an Extrusion Design Guide. It provides the basic facts you’ll need to start the plastic extrusion design process
How much does extruded plastic cost?
Every extrusion solution is unique and deserves a custom quote. Though much of our work is custom-engineered, we can help you determine if an existing profile will work for your project. Request a Quote to learn more.
My project requires an NDA. How do I submit that?
You can attach your NDA to our RFQ form or send it directly to plasticsales@geminigroup.net.
Seal FAQs
What material is best for sealing?
There is no “one size fits all” material that works for every seal application. That’s why we've developed The Engineers’ Guide to Selecting an Extruded Seal Material. It provides stats and specs for dozens of extrusion materials and will guide you through the most critical considerations so you can make the best choice possible for your unique application.
How can I prevent seals from buzzing, squeaking, and rattling (BSR)?
Buzzes, squeaks, and rattles (BSRs) are 100% preventable, yet they remains a major source of warranty claims. This is typically the result of improper material friction characteristics, chemical reactions, and/or environmental factors. To prevent seal chatter, take a look at the surrounding system.
- To what, and how, will the seal be attached?
- What is its proximity to other components?
- Will it be exposed to extreme temperatures, chemicals, or ozone?
Once you have an understanding of the application’s environment, you can predict potential BSRs and determine the best method of prevention. Some of the most common solutions include the application of a slip-coat, blending a slip-agent directly into the seal material, and applying flock tape or spray to exposed surfaces.
How can I prevent a rubber seals from staining or bleeding?
Staining and bleeding have long plagued rubber seal applications. Fortunately, you can prevent it.
Staining happens when additives in the rubber have some solubility with a mating surface; such is the case with the infamous rubber-footed table stain in the linoleum-floored kitchen. You can prevent this by creating a barrier between the mating materials.
Bleeding is the seepage of rubber additives, namely oils. There are some rubber compounds that are resistant to bleed, but the only way to prevent it entirely is to use an alternative material such as TPV.
What is the white powdery substance that builds up on the surface of a rubber part?
This phenomenon is referred to as “blooming,” and occurs when compounding agents in the rubber migrate, or bloom, to the surface. This is due to the agents’ limited compatibility with the rubber elastomer. It affects the tensile strength, adhesion properties, and appearance of your part.
What are the alternatives to rubber seals?
Depending on your seal application, you may have numerous alternatives to rubber. The most common is TPV, a rubber-like material that can be processed and recycled like plastic, but without the stain, smell, and blooming you see with rubber. It’s like a simplified rubber, allowing for more flexible part design, quicker manufacturing, reduced part/system costs, and weight reduction. Some other alternatives to rubber include TPO, TPU, TPZ, and PVC among others. To help you navigate the sea of options, we've developed the The Engineers’ Guide to Selecting an Extruded Seal Material.
Our Customers
Wherever You’re Located, We’re Here to Help
17 strategic locations in North America to meet the needs of our diverse customer base.
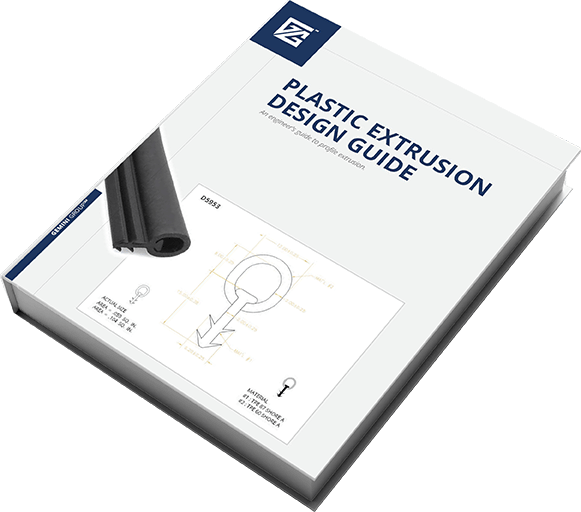
PLASTIC EXTRUSION DESIGN GUIDE
Is your extrusion design optimized to meet the constraints of the extrusion process? This free guide offers a solid foundation in the requirements for successful extrusion design. Created by engineers for engineers, and based on decades of extrusion development and manufacturing experience.
Insights
Get to know us. Get in touch today.
We have the resources to meet any part or production challenge. Let’s talk about what that means for you.
"*" indicates required fields