Valley Enterprises, GGIT
COMPRESSION MOLDING
Compression molding: where precision meets innovation. This process involves manufacturing parts by placing material within a heated metal mold and applying controlled pressure. The trifecta of material, heat, and force are delicately orchestrated to ensure that the final product achieves the exact geometry and shape envisioned.
Advantages of Compression Molding
Large & Intricate Moldings
This method is perfect for crafting intricate large components, lending itself to creating detailed designs that truly stand out.
Cost-Effectiveness
Compared to other molding techniques, compression molding is one of the lowest cost options for the molding of interior trim components.
Minimal Waste
Compression molding results in very little wasted material, making it a great choice for processing a variety of materials including expensive compounds.
High Production Efficiency
The process is well-suited for high-volume production runs. Multiple cavities can be incorporated into the mold, allowing for the simultaneous production of multiple parts in each cycle.
Consistent Quality
Compression molding provides excellent control over part dimensions and tolerances. The process allows for consistent quality and precision in the manufactured parts.
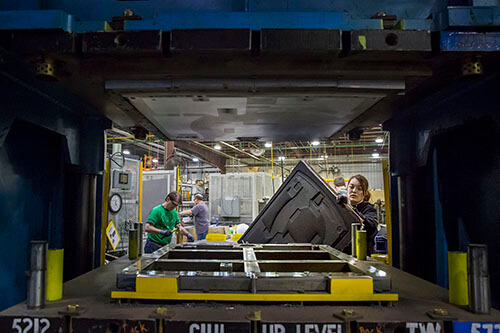
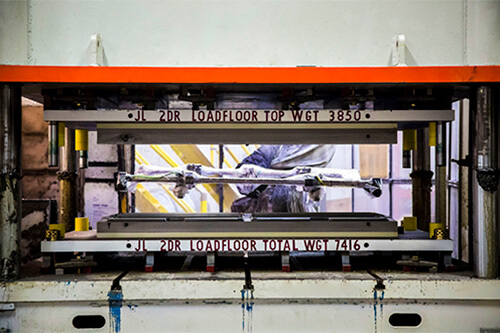
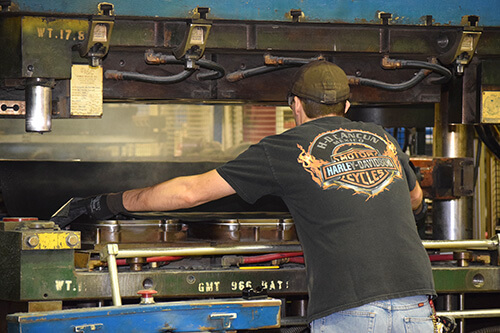
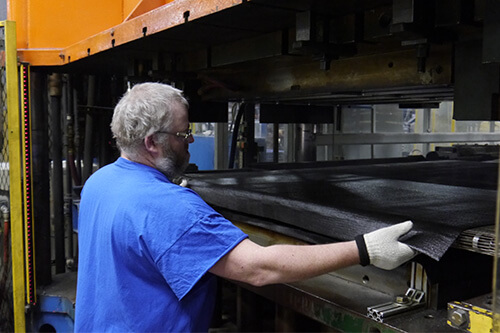
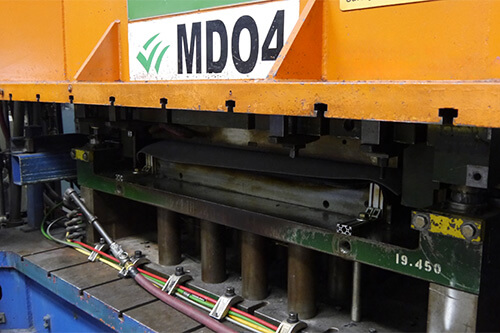
Wherever You’re Located, We’re Here to Help
17 strategic locations in North America to meet the needs of our diverse customer base.
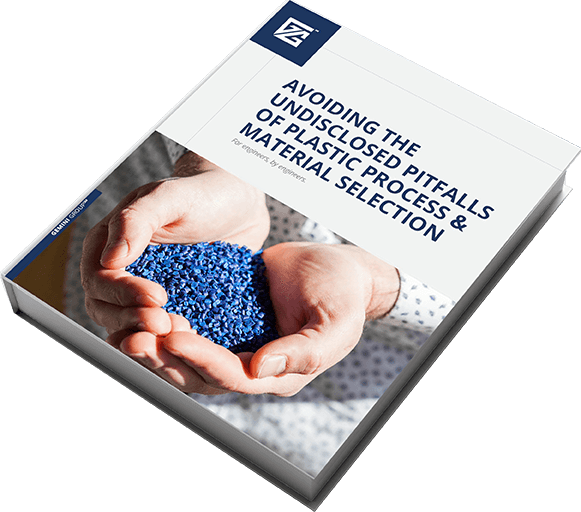
Molding Process Selection
Though compression molding has several advantages over other molding processes, there are still restrictions and several different ways the compression molding process can be accomplished.
For more information on choosing the ideal process for your parts, download a free copy of Avoiding the Undisclosed Pitfalls of Plastic Process & Material Selection
Insights
Get to know us. Get in touch today.
We have the resources to meet any part or production challenge. Let’s talk about what that means for you.
"*" indicates required fields