GPMI, CT
The Market
FORGER OF HEAVY TRUCK COMPONENTS
A forger of heavy truck components utilizing an automatic forging line to manufacture medium production volumes.
The Challenge
TOOLING CONSTRAINTS AND IMPEDED CHANGEOVERS
After purchasing a turn-key automated forging line, the forger was limited by the constraints of the tooling design and experienced problems with a rather long extrusion punch. The bolster and die holders were designed in such a way that the full bolster had to be dropped to service or change out a finish punch from the top side.
This activity would typically take 2.5 hours to complete, often at the expense of valuable production hours.
The solution
PUNCH HOLDER PERFECTION WITH EASY ACCESS AND INSTALLATION
We recommended an alternative punch holder design whereby the holder could remain attached to the bolster while a worn or damaged punch was accessible from the working surface. This eliminated the need to drop the entire bolster to gain access to the punch.
A new punch design allowed for use of a shorter punch with a threaded feature facilitating installation with a standard impact gun. A square driver feature was incorporated into the end of the punch for even greater ease of installation.
The Result
87% REDUCTION IN DOWNTIME AND SO MUCH MORE
Downtime was reduced from 2.5 hours to 15 minutes with the improved design and simplified changeover – an 87% reduction. This equated to over $300,000 in annualized savings.
Additional benefits include a 10% savings on tooling due to the shorter punch design, an elimination of runout issues, and improved quality of the finished forged parts.
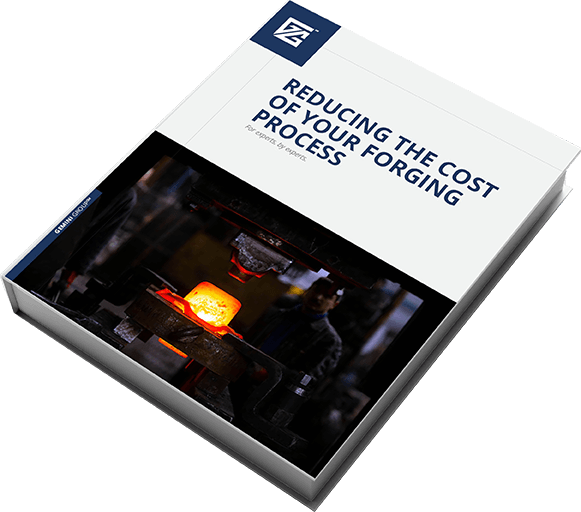
REDUCING THE COST OF YOUR FORGING PROCESS
We’ve spent decades helping forgers across the country enhance tool performance and improve operational efficiency, and we want to help you, too. Learn how to eliminate wasted time, money and other precious resources in our free e-book written by experts, for experts.