GPMI, CT
The Market
LARGE COMMERCIAL AUTOMOTIVE FORGER
A large commercial forger producing a tight-tolerance automotive front end steering component.
The Challenge
DIE WEAR, EXCESSIVE DOWNTIME, AND COSTLY REPAIRS
The forger was experiencing excessive downtime due to impression die tooling wear. The changeover time for worn dies was typically 2.5 hours and repairing them involved flood welding and then re-sinking (re-machining).
The solution
GET THAT DIE SOME SHOES!
We helped redesign the hammer dies into die shoes that hold quick-change inserts. The inserts are made from a harder and more durable material than the original die and allow the bender and buster to remain in place during changeout.
The Result
EXTENDED DIE LIFE, STREAMLINED CHANGEOVERS, AND A HAPPY TOOLROOM
In short, our quick-change inserts benefit the forger with improved die life, reduced changeover time, and lower die maintenance and replacement costs.
The harder and more durable insert material improved die life from 25,000 pieces to 40,000 pieces, a 60% improvement in number of hits per die.
With no need modify the height of the bender/buster to service the die and no need to remove them to replace the die, the quick-change inserts offered a maintenance cost savings of $1,000-1,200 per die set and a changeover time reduction of 83% – from 2.5 hours down to just 25 minutes!
Lastly, the new design allowed the forger to eliminate two repair processes (flood welding and re-sinking), conserving internal resources and avoiding issues associated with those processes.
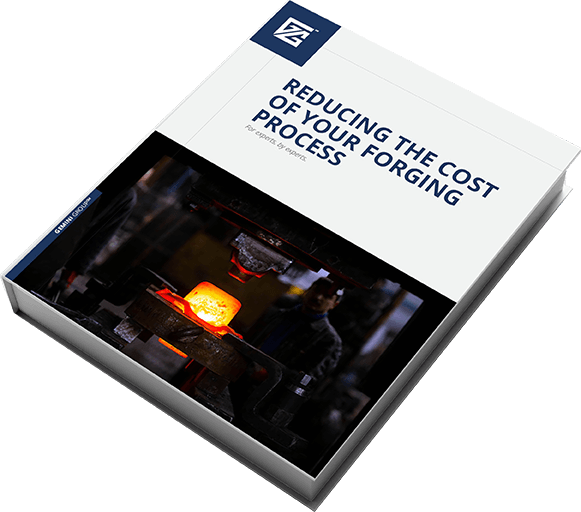
REDUCING THE COST OF YOUR FORGING PROCESS
We’ve spent decades helping forgers across the country enhance tool performance and improve operational efficiency, and we want to help you, too. Learn how to eliminate wasted time, money and other precious resources in our free e-book written by experts, for experts.