Regency
The Market
AGRICUTLURAL EQUIPMENT OEM
Distinguished by a signature green and yellow color scheme, our customer is the world’s largest producer of agricultural machinery, as well as a leading OEM for heavy equipment for the construction, forestry, and lawn care industries.
The Challenge
INEFFICIENT MANUFACTURING PROCESS: FUNCTIONALITY, REPEATABILITY, AND SCALABILITY ISSUES
To function correctly, each component of an HVAC system must have a certain degree of insulation. If any component is thermally inefficient, the entire system will suffer. Such was the case with the customer’s K-duct, so named because of its distinctive “k” shape.
The K-duct had always been produced using the rotomolding manufacturing process, a process that doesn’t scale well. Moreover, the tooling for rotomolding is soft, causing repeatability issues in both manufacturing and assembly.
As an alternative manufacturing process, blow molding is scalable and becomes more cost-efficient as production volumes increase. So it was a no-brainer for the customer — they had to switch to blow molding.
The solution
DESIGN OVERHAUL: ALTERNATIVE MATERIAL AND MANUFACTURING METHOD
With over four decades of technical blow molding experience, we were quickly identified as a capable supplier. Our additional expertise in material selection was the icing on the cake.
For the insulation challenge, HDPE was combined with a foaming agent to create an expanded foamed wall. This added thermal properties and created structural rigidity.
Next, the design was optimized for manufacturing and assembly. The K-duct, originally assembled from 43 different parts, would be made in two pieces and joined using infrared (IR) welding.
The Results
IMPROVED PART WEIGHT AND PERFORMANCE, DELIVERED AT A LOWER COST
After a successful development project, the OEM was confident in choosing us to produce their enhanced design using the blow molding manufacturing process. They would no longer face issues with functional requirements or constrained capacity. They would no longer fear the possibility of field failure and warranty issues due to inconsistency.
In the end, the customer had a part with decreased weight and cost, increased thermal properties and structural rigidity, a quicker turnaround, and increased annual volume capacity.
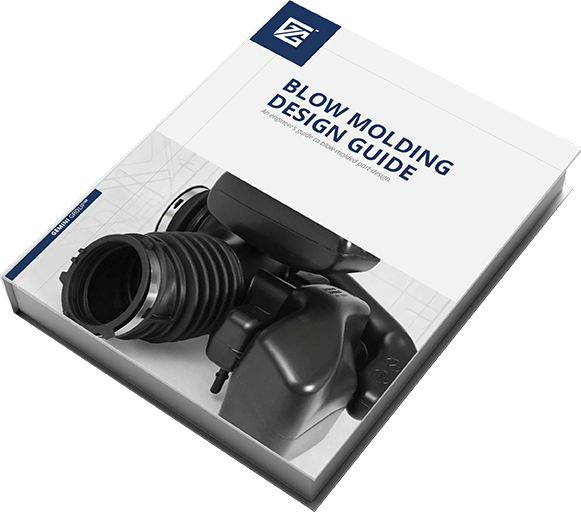
BLOW MOLDING DESIGN GUIDE
Are you new to blow molding and don’t know where to start with your part design? Then our Blow Molding Design Guide is for you! Created by engineers, for engineers, this guide is the ultimate starting point to kick off a successful product design for the blow molding process.