GPMI, CT
The Market
MAJOR FORGED AXLE MANUFACTURER
A major forged axle manufacturer for automotive and heavy truck applications.
The Challenge
UNACCEPTABLY LOW DIE LIFE
The forger was experiencing lower than acceptable die life on a finish punch station. Typical life was only about 3,000 hits.
The solution
A WINNING COMPINATION OF MATERIAL, TREATMENTS, AND COATING
We provided a solution that included the selection of punch material, a proprietary heat treatment process including cryogenic treatment, and application of a coating designed for better graphite lube retention.
The Result
NEW PUNCHES TRIPLE DIE LIFE
The new punches achieved 9,000 hits before replacement – three times that of the previous version. The forger achieved annual tooling savings of approximately $108,000 per year.
In addition, changeover time during productive hours was reduced by 67%. With downtime cost estimated at $2,000 per hour, annual changeover savings of $140,000 to $170,000 per year was achieved.
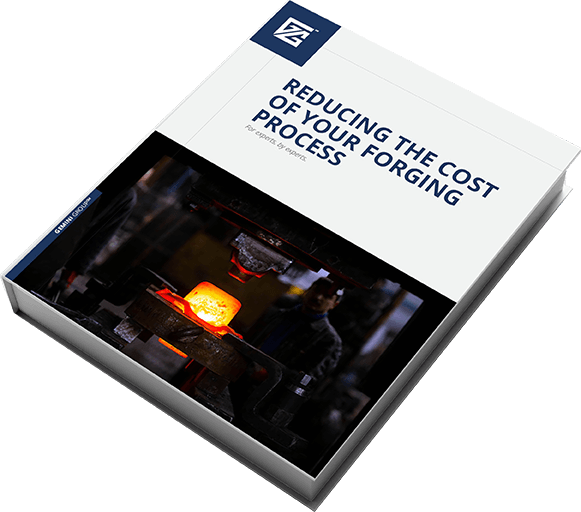
REDUCING THE COST OF YOUR FORGING PROCESS
We’ve spent decades helping forgers across the country enhance tool performance and improve operational efficiency, and we want to help you, too. Learn how to eliminate wasted time, money and other precious resources in our free e-book written by experts, for experts.