Regency
The Market
TIER 1 AUTOMOTIVE SUPPLIER
The customer is a Tier 1 Automotive supplier, specializing in systems, components, and engineering services that enhance the safety, sustainability, and connectivity of motor vehicles.
The Challenge
NAVIGATING DESIGN COMPLEXITIES FOR SEAMLESS INTEGRATION INTO AN EXISTING UNDERHOOD SYSTEM
The customer needed help developing a washer fluid tank for an automotive OEM. As the last part to be added into the underhood system, washer fluid tanks need to fit into the oddly-shaped space between existing components and the walls of the engine compartment. The design and manufacturing of the tank is inherently challenging.
Adding to the challenge was the requirement that the reservoir was fixed-capacity with a separate fill neck with a leak-proof interface and retention pockets for the washer fluid pump and level sensor.
In addition, all features had to be integrated without the use of additional assembly or secondary operations and the material had to pass freeze-thaw cycle tests.
The solution
ENGINEERING EXCELLENCE: INNOVATIVE MOLD DESIGN AND MANUFACTURING EXPERTISE
With countless OEM washer bottle programs under our belt, we hit the ground running. To tackle the fill neck’s leak-proof interface, we machined the OD on the wall of the neck and fitted the ID with a flexible gasket.
Next, we added the pump and sensor retention features as independent inserts into the mold that could be moved in the event of engineering changes.
Finally, we optimized the part design with a blow molding process simulator.
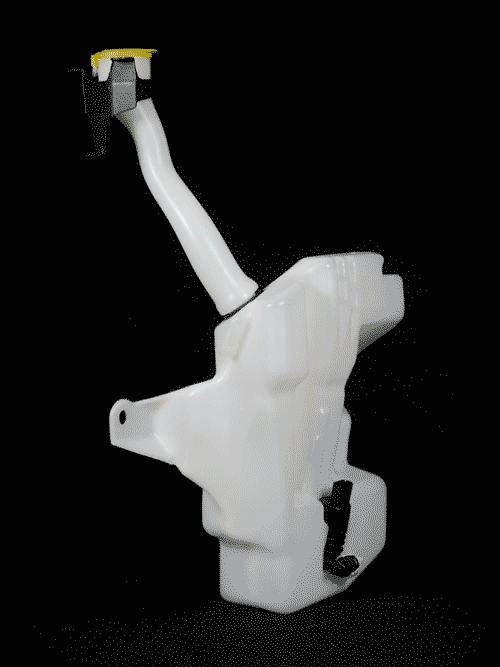
The Result
SUPPLIER SCORECARD SOARS: A FLAWLESS PRODUCT, ON-TIME AND IN-COST
As with any complex engineering program, the customer could have easily suffered last-minute design changes and late delivery, tarnishing their reputation with the OEM. Instead, they recruited us to guide them to the finish line.
In the end, the customer had a product that met performance expectations, delivered on-time and in-cost on a high-volume program of 400,000 parts annually. It’s likely the customer will be the first to be called on the OEM’s next washer fluid tank program.
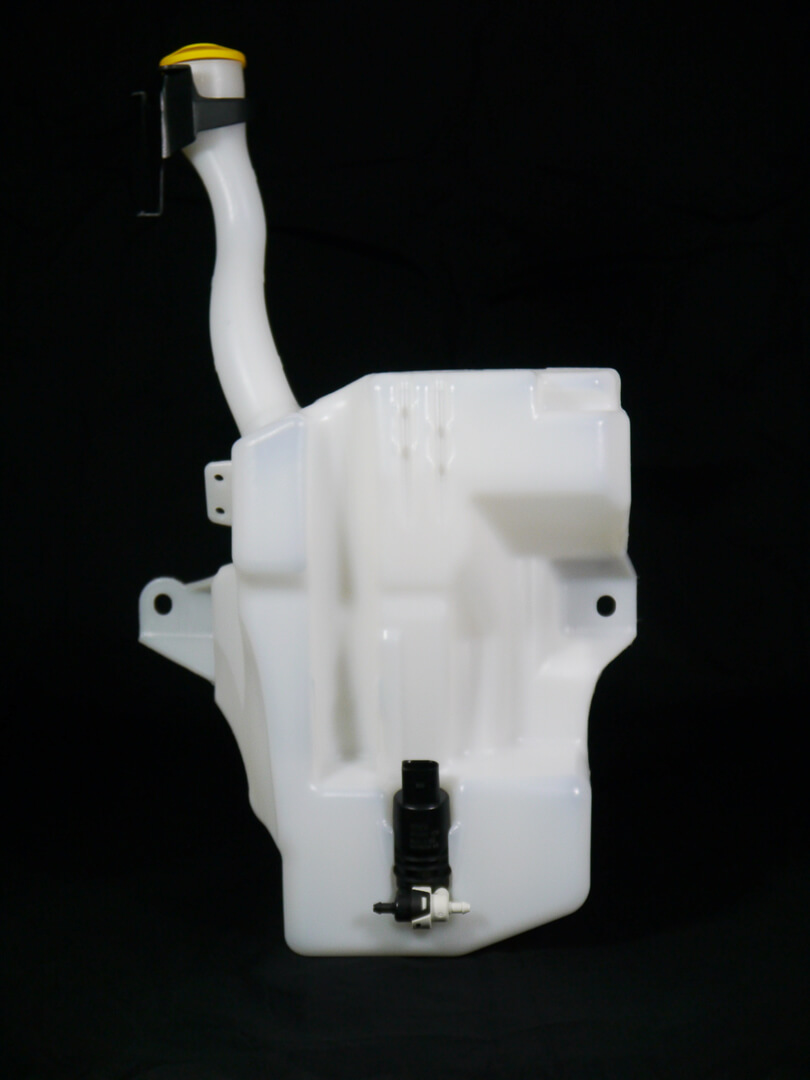
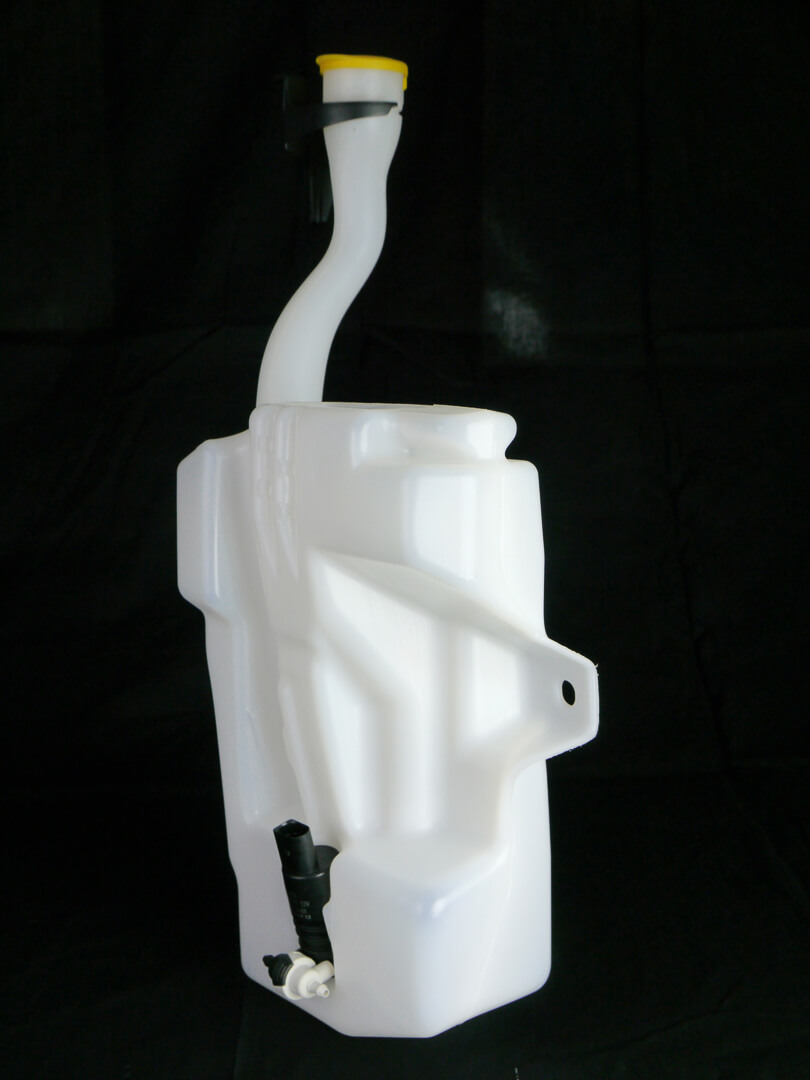

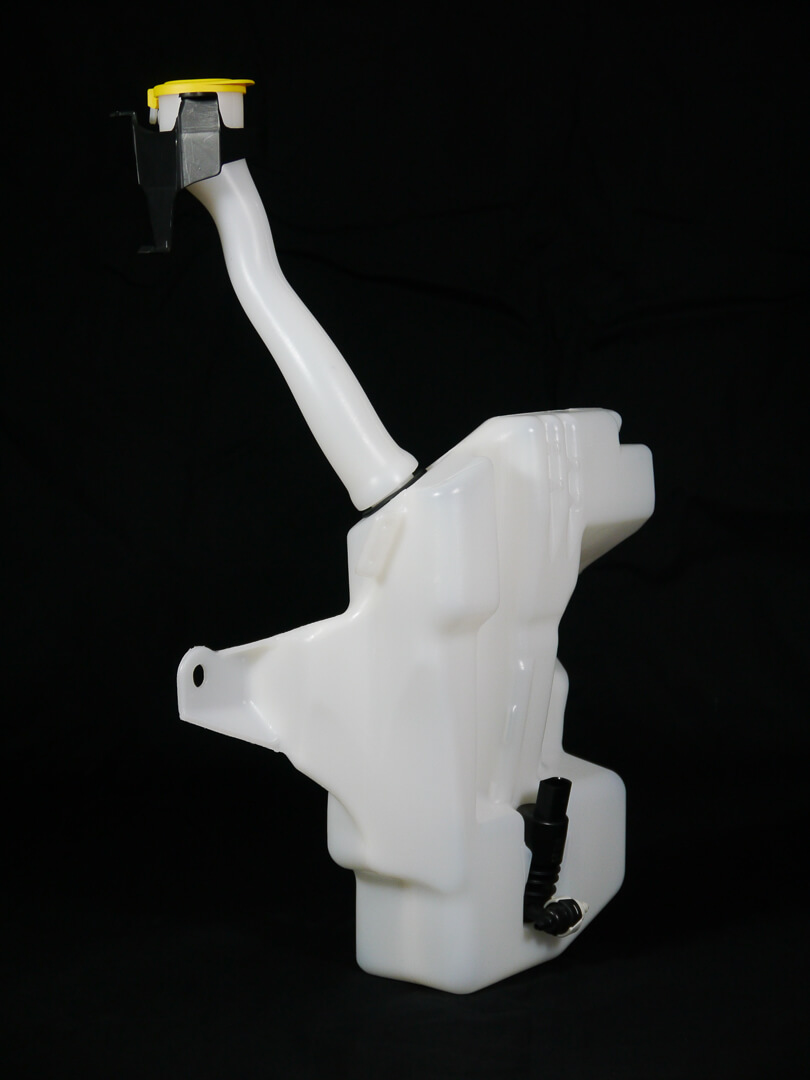
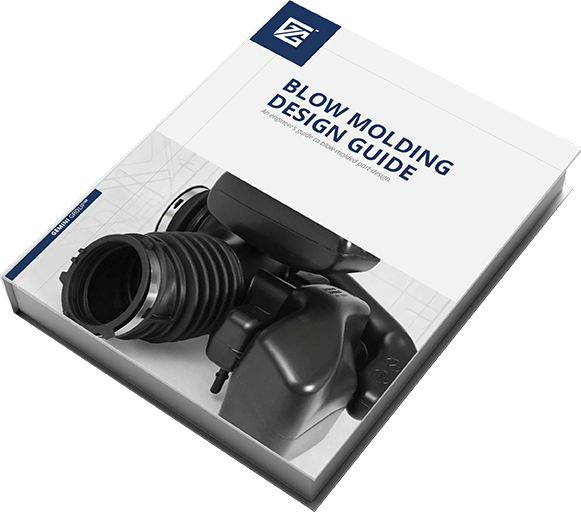
BLOW MOLDING DESIGN GUIDE
Are you new to blow molding and don’t know where to start with your part design? Then our Blow Molding Design Guide is for you! Created by engineers, for engineers, this guide is the ultimate starting point to kick off a successful product design for the blow molding process.