WATERPROOFING AN ENCLOSURE: SYSTEM AND SEAL DESIGN
Waterproofing is a challenge. That’s why you hear phrases such as “Water always wins.” And that’s why most waterproof enclosures can only be referred to as “water resistant” or even “water repellant”. But waterproofing is a real need, and despite the challenges from rain, humidity, and seal failure – not to mention the lack of definitive information on seal design – we aim to arm you with truly helpful information to help you develop a watertight seal design.
But step one in waterproofing is understanding water management. You can have a great seal design but if you haven’t done everything you can to manage the water that could reach the area you intend to protect, your design may be destined to drown.
Overall System Design
Protecting an area from water is like defending an end-zone. The seal is the safety, the last line of defense. It’s a position that would be ineffective without the support of the surrounding system comprised of defensive linemen, linebackers, and cornerbacks. Even with a solid defensive strategy, that last line of defense – the safety, the seal – must be adaptable and strong enough to guarantee coverage across the entire end line.
Likewise, a watertight design requires an adequate seal, as well as a strategy to protect it. When designing a waterproof enclosure, it is key to consider whether there’s a way to divert water away from the critical area. Designs with appropriate sloping or guttering can be a significant help to your seal. Additionally, positive pressure along the edge of the seal and even external hinges can be useful water diverters.
Seal Function
Beyond the seal system design, the seal’s actual function should be taken into consideration. The key issue here is the level of protection needed in the application. Is it truly providing a waterproof enclosure? Does the seal environment face dripping water, spraying water, splashing water, water jets of varying pressures, or immersion? And if it is immersed, at what depth? Sealing to the extreme has the potential to add product size and cost so it’s always best to know “how sealed is sealed” for you.
Moreover, there may be other functions the seal is expected to perform, such as weatherproofing, reducing friction, mitigating shock or vibration, providing a spring force and whether the seal needs to protect against solids or air. All of these should be taken into consideration, especially in watertight design applications.
Key Questions In Design Of Sealing Environment
As for the seal environment, ask these key questions:
- What temperature will the seal reach and for how long?
- Will the seal be directly exposed to UV rays or ozone?
- Are industry recognized flame ratings required such as UL-V0, UL-HBF, or MVSS-302?
- Will the seal contact chemicals or fluids that could compromise it’s function?
- Does the seal need to insulate against electrical shock?
- What is the thickness range of the gap to be sealed?
- What will be the closing force and direction of the load on the seal?
- Will the seal need service or maintenance? Will it be affected by the service to or maintenance of the surrounding system?
Choosing a Seal Material
Finally, the seal’s material properties can significantly impact the seal design of a waterproof enclosure.
Physical properties
- Tensile strength
- Hardness range or compression deflection requirements
- Compression set at room and operation temperatures
- Aging in sunlight, ozone, heat, storage, etc.
- Color (if color matching is desired or necessary)
- Aesthetics
Resistance properties
- Reaction to acids or caustics
- Abrasion
- Hydrocarbon solvents
- Oxygenated solvents
- Flame or temperature extremes
- Tearing
Mechanical properties
- Speed or recovery from deflection
- Flexibility
- Permeability to gases
As you know, each material has its strengths and weaknesses when it comes to rigidity, heat stability, chemical resistance, impact strength, and relative cost. These are outlined in the following chart:
Material Type | Rigidity | Heat Stability | Chemical Resistance | Impact Strength | Relative Cost |
---|---|---|---|---|---|
Polypropylene | Excellent | Excellent | Excellent | Excellent | Low |
Low Density Polyethylene (LDPE) | Poor | Poor | Good | Excellent | Low |
Medium Density Polyethylene (MDPE) | Good | Poor | Good | Excellent | Low |
High Density Polyethylene (HDPE) | Excellent | Poor | Good | Excellent | Low |
ABS | Excellent | Poor | Poor | Excellent | Medium |
TPR, TPV, TPO, TPE | Varies | Excellent | Excellent | Excellent | High |
PVC – rigid and flexible | Varies | Poor | Poor | Excellent | Medium |
Polycarbonate (PC) | Excellent | Excellent | Fair | Excellent | High |
Nylon | Excellent | Excellent | Excellent | Excellent | High |
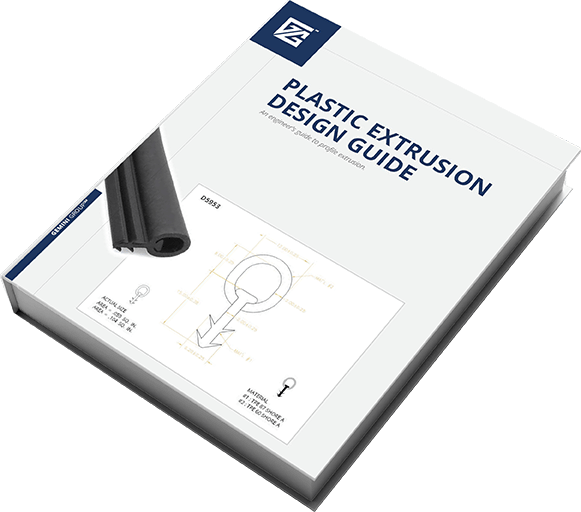
EXTRUDED SEAL DESIGN
We are proud to present to you the cumulation of over 50 years of experience in extrusion. We’ve helped thousands of engineers just like you with their extruded seal design – and this guide truly is the next best thing to working directly with our seals specialists.